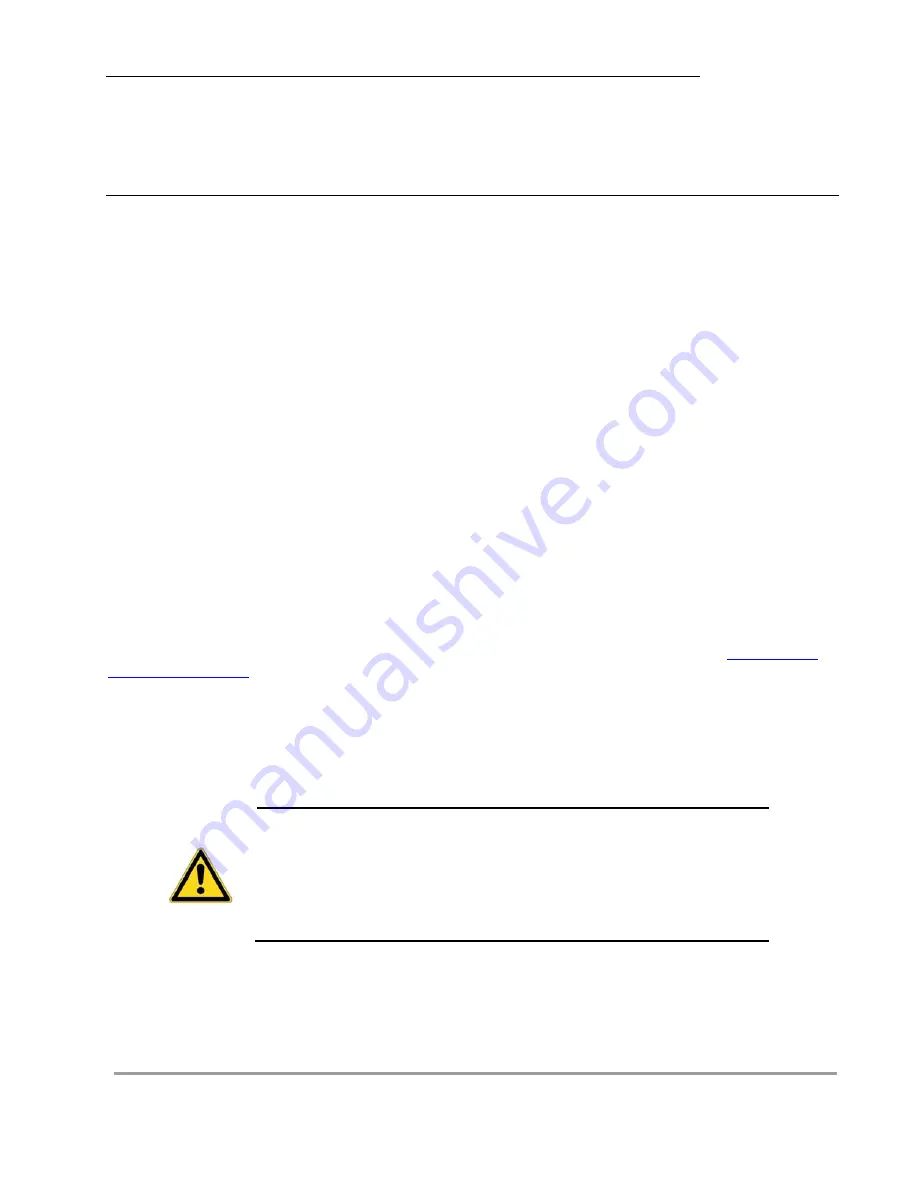
XPR2/XPC2 PowerStation Series Hardware User Guide
Page 7 of 47
I
NSTALLATION
Selecting a Location
The first step when installing the XPR2/XPC2 PowerStation is to select an appropriate location. This is the most
important aspect of the installation process because the location affects unit performance, ease of use and
life-expectancy. This section provides guidelines to follow when selecting a location.
Underwriters Laboratories UL508 Approval
In order to obtain Underwriters Laboratories (UL508) certification for the PowerStation installation, the
installation must meet the following criteria:
•
The PowerStation is suitable for mounting on the flat surface of a Type 4X Indoor Use Only or Type
12 enclosure.
•
Power to the device must be provided by a Class 2 power source. For convenience, Parker has an
AC input, model P1X-PWRAC Class 2, 24Vdc power supply available for purchase to provide
power to any of the XPR2/XPC2 PowerStation sizes.
Environmental Guidelines
In general, select a location that limits the PowerStation’s exposure to adverse conditions such as dust, oil,
moisture, condensation, and corrosive vapors.
The XPR2/XPC2 PowerStation’s touchscreen/faceplate assembly is designed to meet the NEMA Type 4X
Indoor Use Only or Type 12 rating. Mount the PowerStation in an enclosure that also supports this rating if it is
a requirement for the installation.
The touchscreen/faceplate is resistant to a variety of chemicals. Please refer to
Appendix A
,
Touchscreen
Chemical Resistance
for a complete list.
Electrical Grounding Guidelines
To minimize unwanted electrical interference, select a location away from machinery that produces intense
electrical noise (arc welders, for example). If you cannot avoid electrical noise, isolate input power to the unit
and separate all data communication cables from AC power lines.
Important
—
Use the PowerStation ground stud located on the rear of the
enclosure to connect the unit to a suitable ground reference, such as earth
ground or building steel. A short (less than 8”), heavy copper braid or <10awg
copper wire from the ground stud to chassis earth ground will provide a good
EMI path to ground. This ensures the unit is in compliance with immunity and
emissions requirements necessary for proper operation.