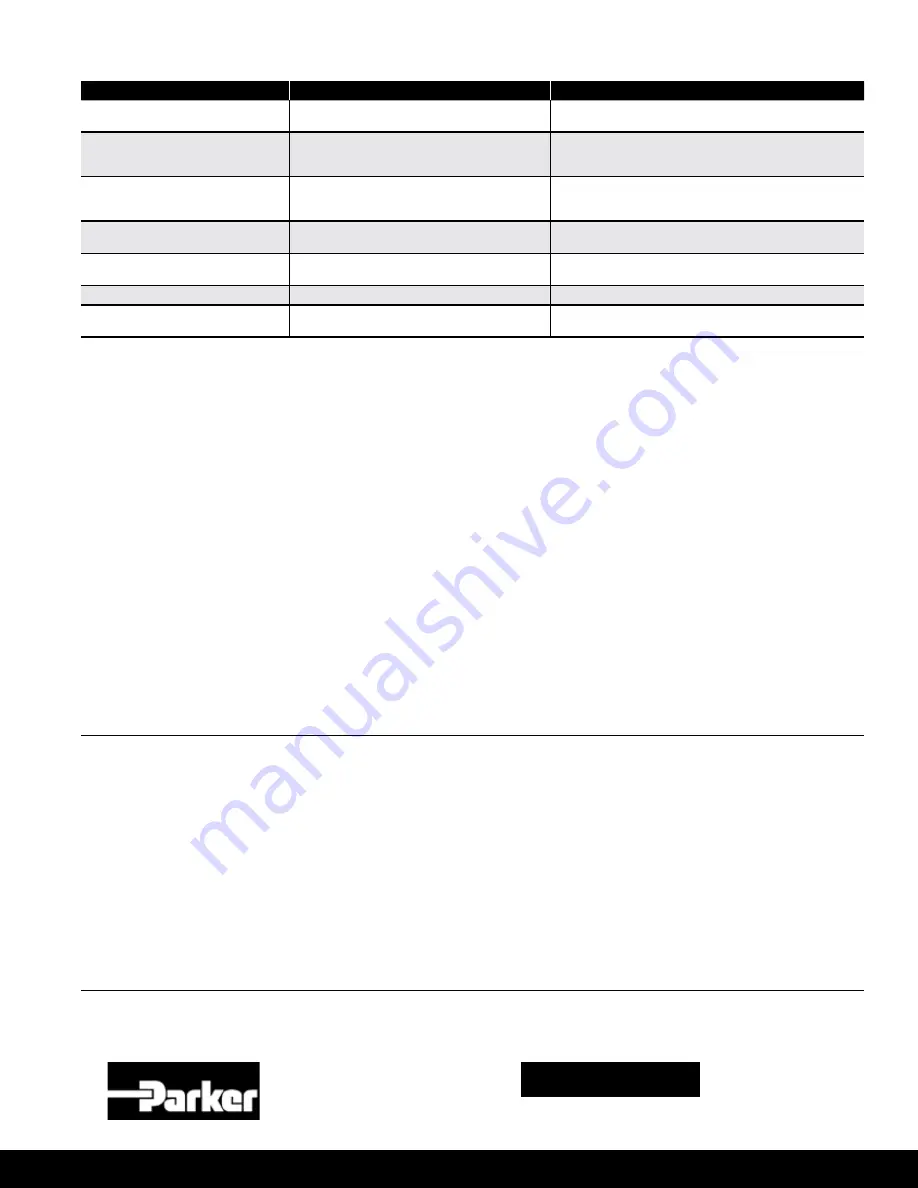
ISO 9001 CERTIFIED
© 2013 Parker Hannifin Corporation
Safe Operation (See Bulletin RSBCV)
People doing any work on a refrigeration system must be
qualified and completely familiar with the system and the
Refrigerating Specialties Division valves involved, or all other
precautions will be meaningless. This includes reading and
understanding pertinent Refrigerating Specialties Division
Product Bulletins and Safety Bulletin RSB prior to installation
or servicing work.
Where cold refrigerant liquid lines are used, it is necessary
that certain precautions be taken to avoid damage which
could result from liquid expansion. Temperature increase in a
piping section full of solid liquid will cause high pressure due
to the expanding liquid which can possibly rupture a gasket,
pipe or valve. All hand valves isolating such sections should
be marked, warning against accidental closing, and must not
be closed until the liquid is removed. Check valves must never
be installed upstream of solenoid valves, or regulators with
electric shut-off, nor should hand valves upstream of solenoid
valves or downstream of check valves be closed until the
liquid has been removed.
It is advisable to properly install relief devices in any section
where liquid expansion could take place. Avoid all piping
or control arrangements which might produce thermal or
pressure shock.
For the protection of people and products, all refrigerant
must be removed from the section to be worked on before a
valve, strainer, or other device is opened or removed. Flanges
with ODS connections are not suitable for ammonia service.
Warranty
All Refrigerating Specialties products are under warranty
against defects in workmanship and materials for a period of
one year from date of shipment from factory. This warranty
is in force only when products are properly installed, field
assembled, maintained, and operated in use and service as
specifically stated in Refrigerating Specialties Catalogs or
Bulletins for normal refrigeration applications, unless other-
wise approved in writing by the Refrigerating Specialties
Division. Defective products, or parts thereof returned to the
factory with transportation charges prepaid and found to be
defective by factory inspection, will be replaced or repaired at
Refrigerating Specialties option, free of charge, F.O.B. factory.
Warranty does not cover products which have been altered,
or repaired in the field, damaged in transit, or have suffered
accidents, misuse, or abuse. Products disabled by dirt or other
foreign substances will not be considered defective.
The express warranty set forth above constitutes the only
warranty applicable to Refrigerating Specialties products, and
is in lieu of all other warranties, expressed or implied, written
including any warranty of merchantability, or fitness for a
particular purpose.
In no event is Refrigerating Specialties
responsible for any consequential damages of any nature what-
soever. No employee, agent, dealer or other person is authorized
to give any warranties on behalf of Refrigerating Specialties, nor
to assume, for Refrigerating Specialties, any other liability in
connection with any of its products.
313172 ECN: 33071 02/05/2013
Symptom
Probable Cause
How to Detect/Repair Defect
No function
No supply voltage
Wrong supply voltage
Check power supply and connection cable
It takes a long time after power up before
the 4-20 mA signal is updated
Min./Max. calibration has been carried out several
times on-site
After power up, the green LED flashes rapidly as many times as
it has been calibrated through its lifetime. After the green LED
flash slowls down, the 4-20 mA is updated
4-20 mA output signal is to low
Oil has been accumulated in the column/standpipe
Oil falls to the bottom on ammonia systems
Drain oil out of column/standpipe. If a very large amount of oil
is present it may be necessary to take out the sensor rod and
clean it for oil
No 4-20 mA output
Not wired correctly
Green LED continues to flash rapidly. If 24 AC/DC supply:
check polarity
4-20 mA signal does not correspond to
actual liquid level
Wrong refrigerant selected
Set correct refrigerant
No 4-20 mA output and green LED is off
Electronics defect
Replace HBLT electronics
4-20 mA signal does not correspond to
actual liquid level
Operator has incorrectly calibrated probe
Fulfill a factory reset
Trouble Shooting