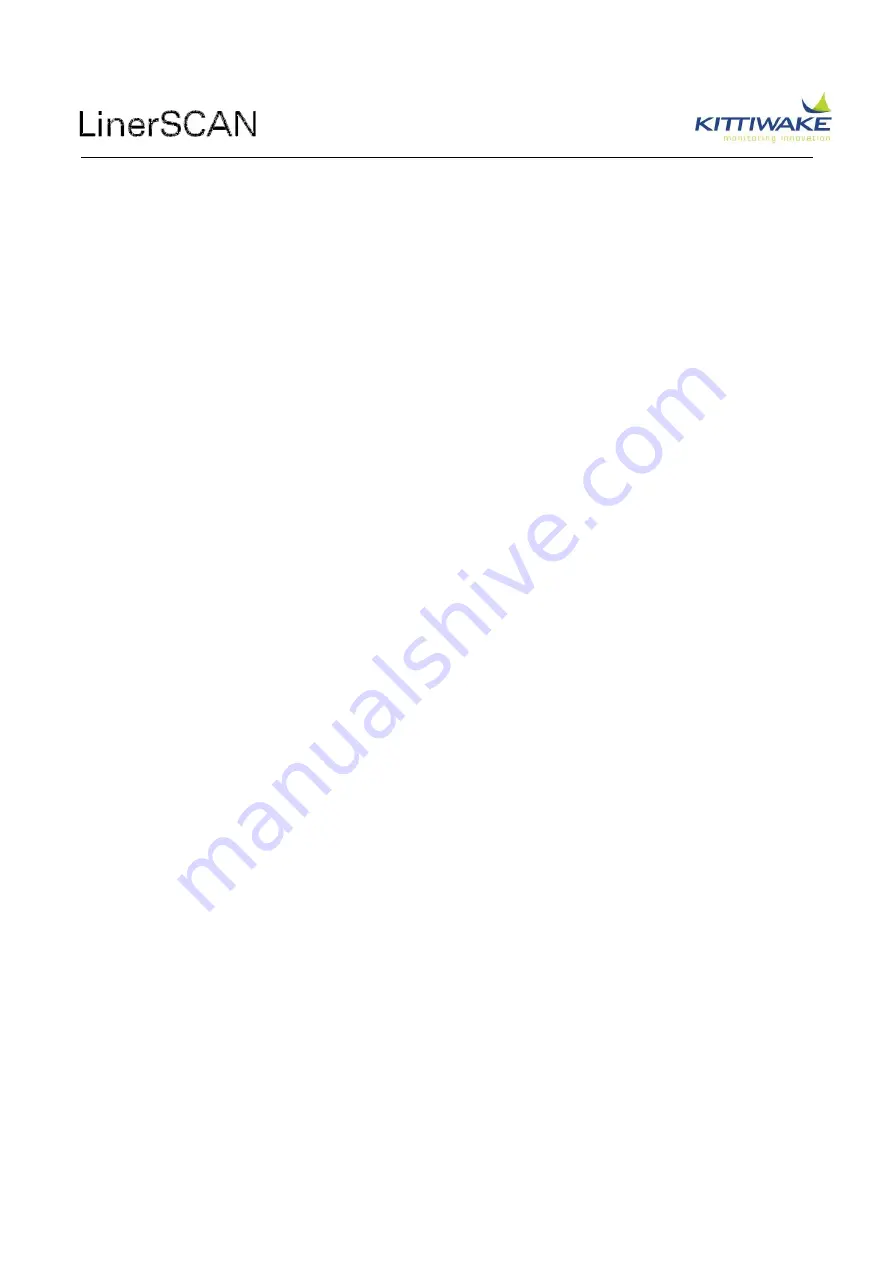
MA-K17510-KW LinerSCAN manual ISSUE P.doc
Page 80 of 93
7.6 Frequently Asked Questions
1. The Sensor readings are higher compared to lab results?
The following is an extract from Elemental Analysis - Mark Barnes ‘Practicing oil Analysis magazine’
Nearly all oil analysis labs use one of two types of atomic emission spectrometer, either an inductively
coupled plasma (ICP) instrument, or a rotating disc electrode (RDE) instrument. The basic difference
between the two lies mainly in the way in which the sample is vaporized and the atoms excited by the
high-energy source. In an ICP instrument, the oil is injected into a high-temperature argon plasma,
where the atoms are vaporized, excited and subsequently emit light. In an RDE spectrometer, also
sometimes referred to as an “Arc-Spark” instrument, the oil is vaporized and excited using a high
voltage discharge between an electrode and a rotating carbon disc.
The rest of the instrument, whether it be an ICP or RDE spectrometer, is basically the same. The light
emitted by the excited atoms is collected and focused onto the slits of the spectrometer. The
spectrometer contains a diffraction grating, which is similar to a prism in that it splits light of different
wavelength or colours into discrete wavelength, based on their angle of diffraction. The light intensity
at each angle, typically referred to as a channel, is measured using a light-sensitive photodiode and
the resultant voltage signal converted to a concentration in ppm based on a simple calibration
procedure.
Both ICP and RDE instruments suffer from size limitation effects. For ICP, only particles smaller than
approximately 3 microns can be measured. For RDE instruments, the limit is slightly higher, around 8
to 10 microns. The implication is that if an oil sample is analyzed first by ICP, then by RDE, the
concentrations of certain elements, particularly wear metals and contaminants, which may be present
as 3- to 10-micron particles will potentially be different.
http://www.noria.com/learning_center/category_article.asp?articleid=287&relatedbookgroup=OilAnalys
is
Therefore the sensor is detecting the particles, greater than 10 microns (0.010mm) [0.008”] that ICP or
RDE fails to vaporise and measure.
Far better is to view the PQ reading which some labs quote on their test sheet. This method indicates
levels of ferrous debris in the oil by Magnetometry, and is not limited by the size of particle. The
sensor also records results real time - before the iron has had time to settle, clump or become
ingested in a sample pot which the laboratory sample is taken from: there may be debris in the bottom
of the pot.
2. Why do the sensors ‘blast’ when the engine is off?
Since Scrapedown oil will continue to drain for a period after the engine has stopped, the sensor
monitors flow and ‘blast’ to avoid the risk of the sensors blocking.
3. Why does the sensor have only 10mm diameter bore?
This is a compromise between sensitivity and the ease at which oil will flow into the sensor. A sensor
with a 50mm diameter bore would not be as sensitive; conversely a highly sensitive sensor with a
3mm bore will be liable to blocking.
Содержание FG-K17401-KW
Страница 9: ...MA K17510 KW LinerSCAN manual ISSUE P doc Page 8 of 93 3 Installation Installation ...
Страница 34: ...MA K17510 KW LinerSCAN manual ISSUE P doc Page 33 of 93 4 Commissioning Commissioning ...
Страница 40: ...MA K17510 KW LinerSCAN manual ISSUE P doc Page 39 of 93 5 Operation Operation Manual ...
Страница 57: ...MA K17510 KW LinerSCAN manual ISSUE P doc Page 56 of 93 6 Interpreting Results Interpreting Results ...
Страница 89: ...MA K17510 KW LinerSCAN manual ISSUE P doc Page 88 of 93 ...