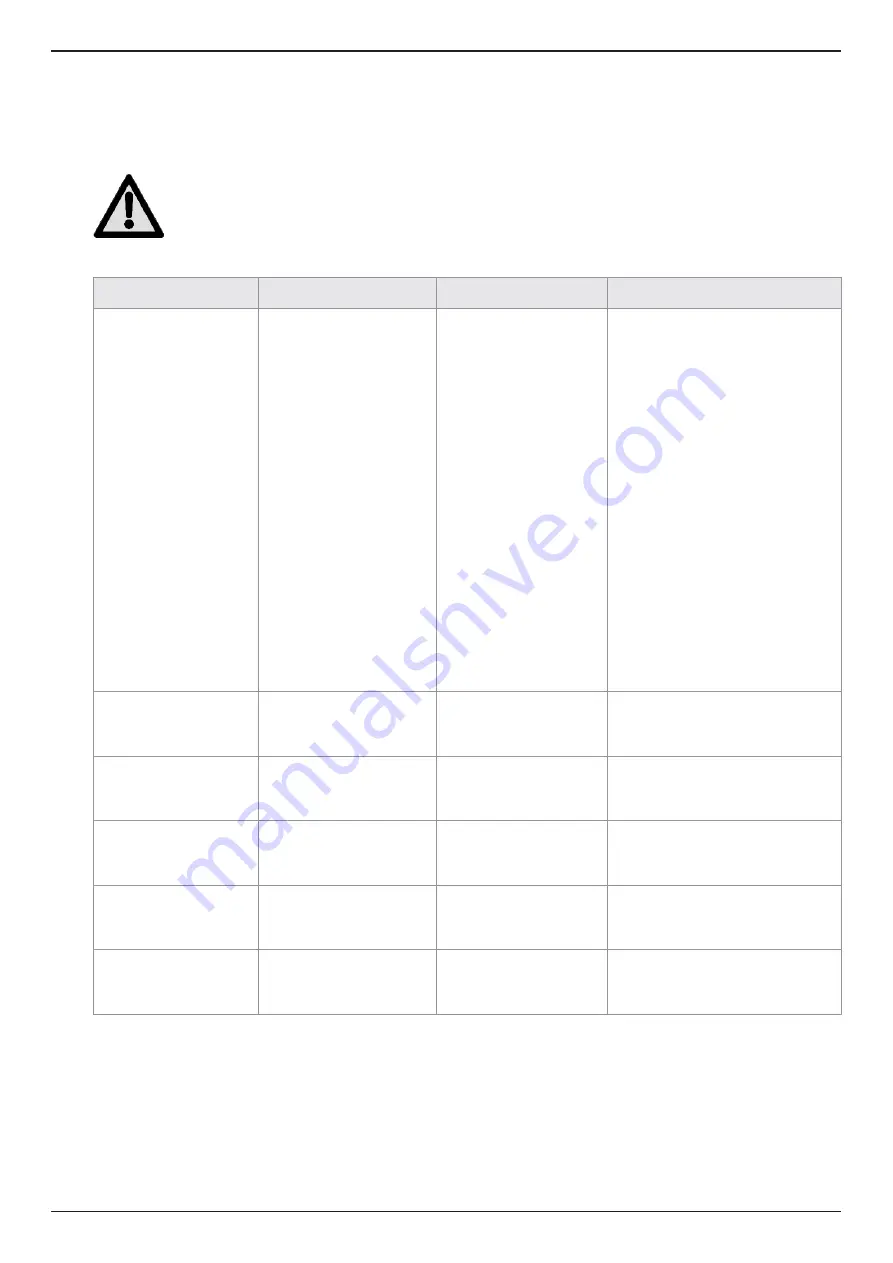
18
DME012-RX - DME080-RX
6.
Troubleshooting guide
In the unlikely event that a problem occurs on the equipment, this troubleshooting guide can be used to identify the probable cause and
remedy.
Warning
Troubleshooting should only be attempted by competent personnel. All major repair, and calibration work should
be undertaken by a domnick hunter trained, qualified and approved engineer.
Problem
Indication
Probable Cause
Remedy
Poor dewpoint
Crystals go clear in the outlet
sight glass (DME040 - 080-RX
Models only)
Entrained Water
Excessive air flow demand
Inlet pressure too low
Excessive inlet air
temperature
Insufficient purge air flow
Exhaust silencers blocked
Contaminated desiccant
Check pre-filtration drains.
Check actual flow against rated flow of
dryer
Check for recent additions to air system
Check against technical specification
Check against technical specification
Factory set for 6 bar g (87 psig) system
pressure.
domnick hunter
trained personnel to
adjust
Change by
domnick hunter
trained
personnel
Eliminate source of contamination.
Desiccant change by
domnick hunter
trained personnel
Electrical fault
Flashing Yellow LED
Hardware fault
Contact
domnick hunter
customer
services
High differential pressure
Pressure gauges
Excessive outlet flow
Check and regulate air demand
Failure to purge
No depressurisation and poor
dewpoint
Purge valve blocked or shut.
Exhaust silencers blocked.
domnick hunter
trained personnel to
adjust.
Change by
domnick hunter
trained
personnel
Outlet air flow stops
Downstream pressure drops.
Yellow LED “OFF”
Electrical fault.
Blown fuse in plug.
domnick hunter
trained personnel to
adjust.
Change by
domnick hunter
trained
personnel
Constant depressurisation
Erratic air flow from exhaust
Damaged valve.
Change by
domnick hunter
trained
personnel