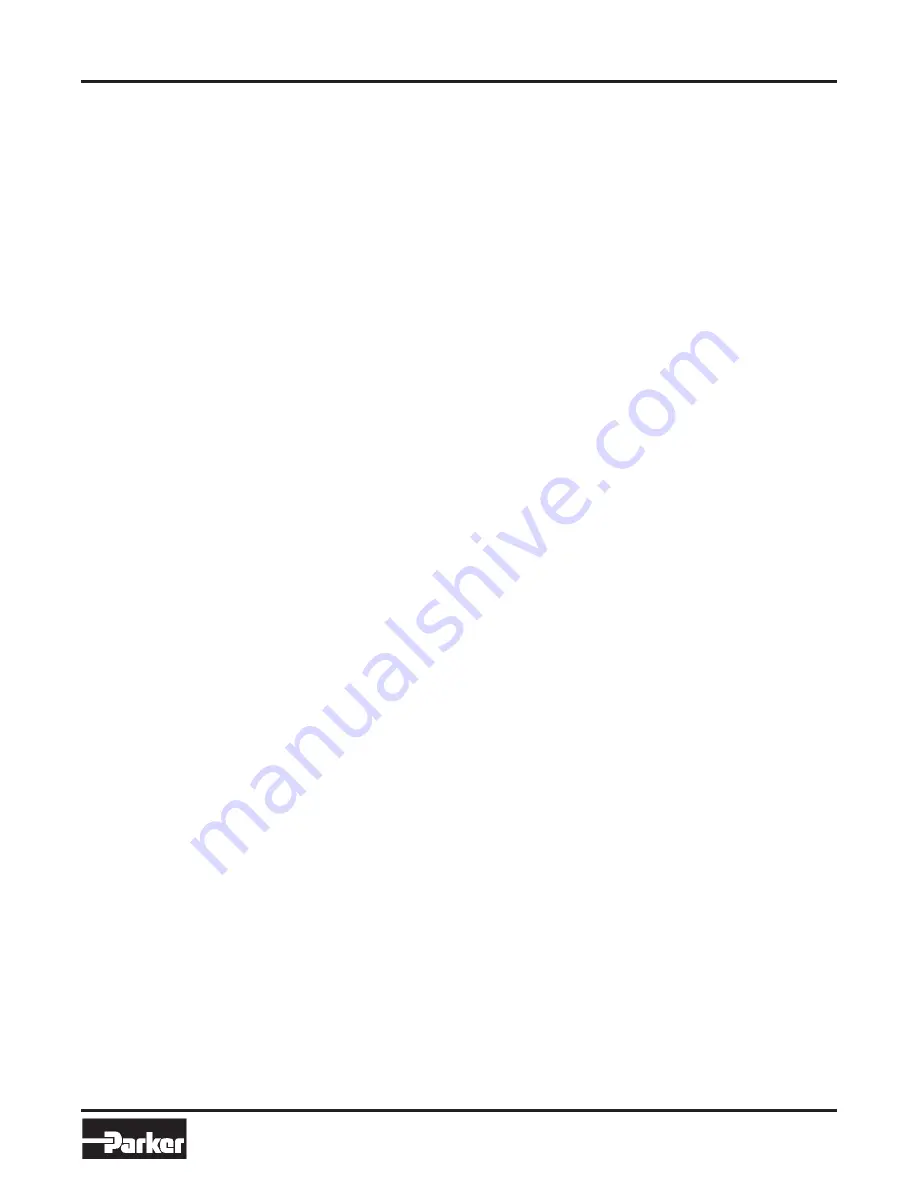
Bulletin TI-FID1000C
FID 1000 and 2500 Gas Stations
Parker Hannifin Corporation
Filtration and Separation Division
Haverhill, MA • 1-800-343-4048
www.parker.com/ags
18
No tools are needed to change the Desiccant cartridge (P/N 1647727). The cartridge should
be replaced when the color of the indicator beads turns color. (The blue beads turn to beige
or gray and the orange beads turn clear.) Once all the indicating beads have turned color, the
cartridge will have approximately 2 days of life left at 90cc/min flow.
1
Turn the Power switch to OFF and leave the user installed shutoff in the open position in
order to vent the Hydrogen from the unit. Unit must be depressurized before removing
desiccant cap. (See Figure 6)
2
Lift the top cover lid and unscrew the cap covering the desiccant cartridge. Remove the
cartridge from the unit.
3
Remove the replacement dessicant cartridge from the moisture proof bag. Add a small
amount of deionized water to wet the o-rings on the nipple end of the desiccant cartridge.
Push down firmly to seat the o-rings at the bottom of the housing (see Figures 7,8, and 9).
4
Replace and center the large o-ring inside the desiccant cap. Tighten the cap securely
by hand. Be sure the o-ring seal remains centered and the seal is visible as a black ring
around the top and sides.
Note:
Most internal leaks are found at the desiccant housing cap o-ring seal, due to improper
sealing of the cap. Be sure to seal the cap tightly.
5
Turn the power switch ON and perform the Controlled Venting purge as described in the
Startup section, then begin using the generator.
Note:
For best results, purge the system for one hour to remove any residual oxygen and
moisture from the instrument and piping downstream.
When the desiccant becomes saturated with moisture, the blue indicating color will turn beige
or gray or the orange will turn clear. The expended desiccant cartridge can be regenerated for
later use, so long as a moisture proof container is available.
Cold Vacuum Oven -
For best results, place the desiccant cartridge in
a cold vacuum oven
and ramp the temperature at 2°C/minute to 150°C while supplying a vacuum.
Do not exceed
175°C.
Regeneration will be complete in 8 hours.
Conventional Oven -
If only a conventional oven is available, place the cartridge upright inside
the oven to allow the moisture to leave from the top of the cartridge. Apply the following ramp
rate and procedure:
• 2 C/min from room temperature to 90°C ,hold at 90°C for two hours.
• 2 C/min from 90°C to 150°C and hold at 150°C for 24 hours.
• Cool the cartridge in a desiccator or low moisture environment until needed in the hydrogen
generator.
For either method, do not exceed 175°C.
The temperature will not affect the desiccant per-
formance; however, once the beads turn Black (for the Blue Indicator) or remain Clear (for the
Orange Indicator), they can no longer be used as a color indicator. Apply a light coat of Dio
water to the o-rings prior to inserting the cartridge into the generator plastic housing.
The DIO Resin bed cartridge should be rinsed and the Resin bed replaced every 6 months, or
whenever the water quality deteriorates, which is detected by a color change in the Resin bed,
ie...the color changes from a Dark brownish color to a Orange color. If 75% of the Resin bed
has changed color, then the Resin bed should be replaced. No tools are required to change
the Resin bed.
Maintenance
Cartridge Regeneration
Resin Bed Replacement
Desiccant Change