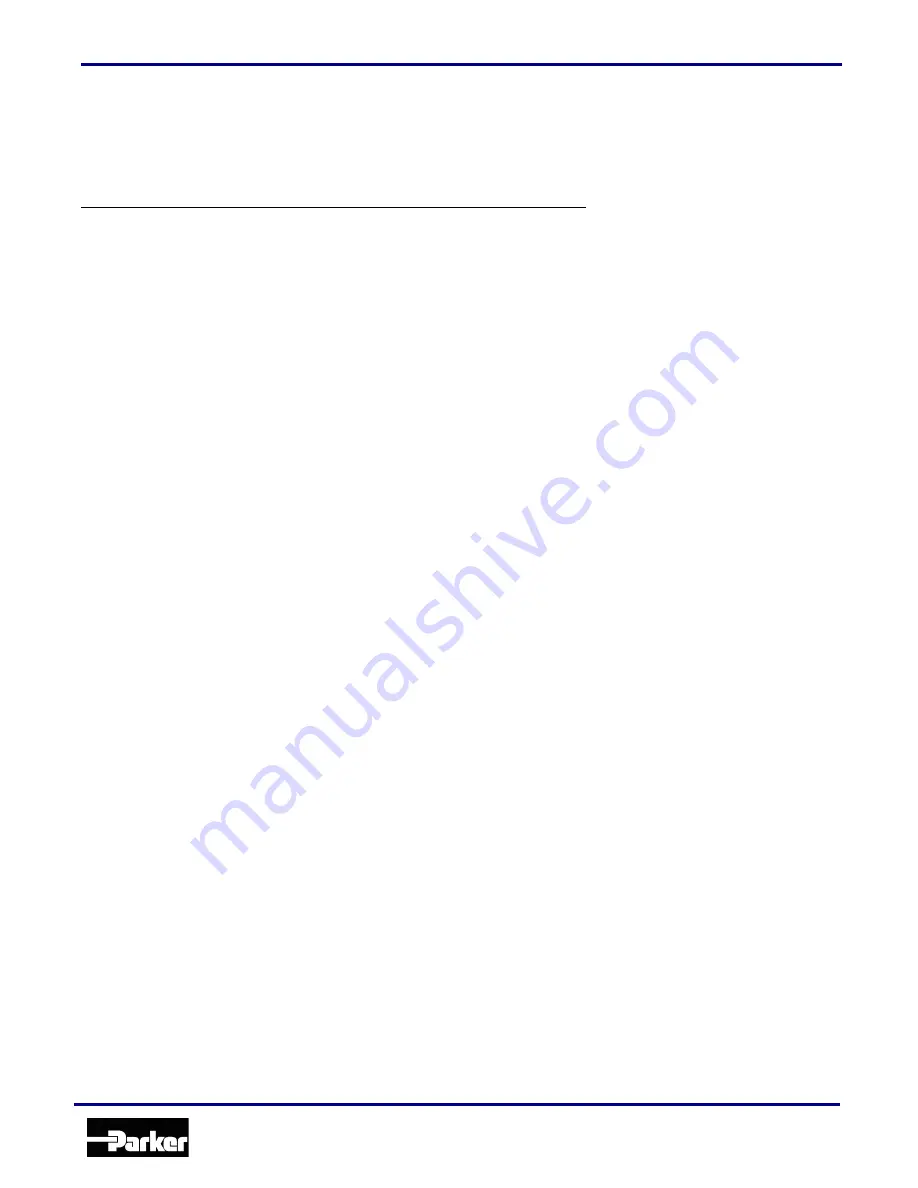
404/406XR Series Product Manual
Chapter 5 - Component Mounting Procedures
32
Parker Hannifin Corporation
1140 Sandy Hill Road
Irwin, PA 15642
www.parkermotion.com
Rotary Encoder Mounting
Tools Required For Adjustment:
Allen Key M1.5, M2, M2.5, M3, 0.050 Dial indicator
Modular Rotary Encoder offers drive screw positional feedback.
Locate and remove bearing cover plate (opposite motor end) by removing (2) button head screws.
Clean the idler end of the ballscrew shaft extending through the bearing block using a clean cloth, and
acetone or alcohol. Remove all oil or foreign material that might be present.
Locate rotary encoder and remove cover.
Locate clamp collar & mandrel. Slip the clamp collar over the large end of the mandrel and slide it up until it
contacts the shoulder. Slip the mandrel through the end block and over the extended portion of the screw
shaft. Using the access hole through the endblock, tighten the clamp collar screw.
Verify concentricity. Using a dial indicator, measure the run out (wobble) on the end of the screw shaft by
turning the drive screw. Run out should not exceed .001in”.
Align hub on the encoder with the shaft and gently push hub onto shaft until the encoder is resting on the
mounting surface. DO NOT push down on encoder - Push on hub only!
Align the set screw with one of the flats on the mandrel. This can be accomplished by spinning the mandrel
(traversing the table).
Maintain pressure on hub to insure that it is seated in centering mechanism and secure hub to shaft by
rotating setscrew clockwise until setscrew makes contact to shaft. Make sure flat on shaft is aligned with
setscrew clockwise until setscrew makes contact to shaft.
Observe the short leg of Allen wrench and rotate additional 1/4in clockwise to apply 20 oz/in torque. (Warning:
Over tightening will cause burnelling of the shaft which will make it difficult to remove the encoder if
necessary!!!).
Align the encoder with the threaded holes in the end block. Insert button head screws and tighten.
Push slide lock in completely. Visually verify that a gap is present between the disk and mask on the
underside of the PC board. If no gap is present, remove encoder and reinstall. Verify encoder mounting by
traversing carriage. The shaft and encoder PC board should spin freely without any noises or increased
torque.
Install cover by snapping it into place.
www.comoso.com