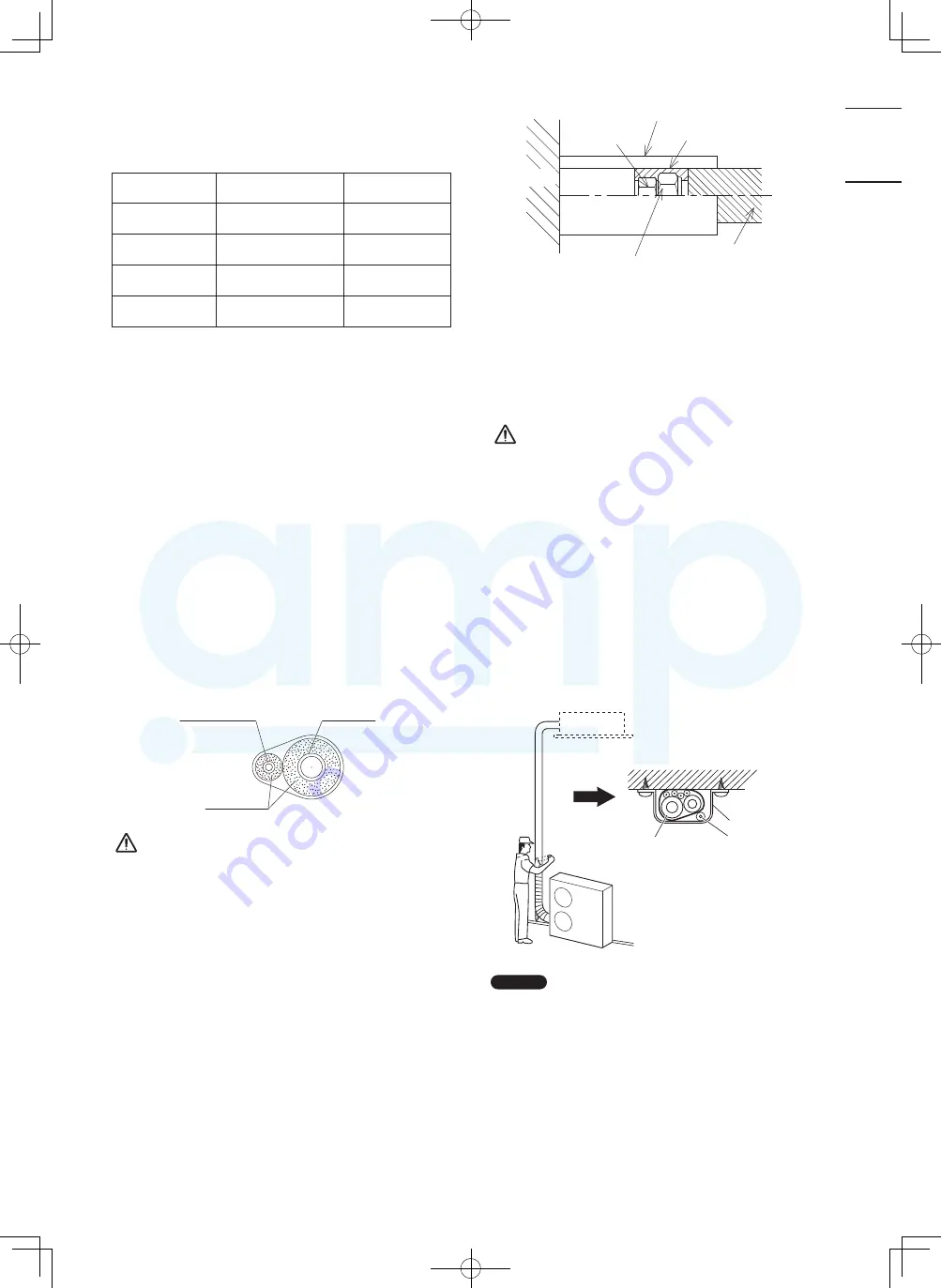
17
ENGLISH
●
For the flare nuts at tubing connections, be sure to use the
flare nuts that were supplied with the unit, or else flare nuts
for R410A (type 2). The refrigerant tubing that is used must
be of the correct wall thickness as shown in the table below.
Tube diameter
Tightening torque
(approximate)
Tube thickness
ø6.35 (1/4")
14 – 18 N · m
{140 – 180
kgf
· cm}
0.8 mm
ø9.52 (3/8")
34 – 42 N · m
{340 – 420
kgf
· cm}
0.8 mm
ø12.7 (1/2")
49 – 61 N · m
{490 – 610
kgf
· cm}
0.8 mm
ø15.88 (5/8")
68 – 82 N · m
{680 – 820
kgf
· cm}
1.0 mm
Because the pressure is approximately 1.6 times higher than
conventional refrigerant pressure, the use of ordinary flare
nuts (type 1) or thin-walled tubes may result in tube rupture,
injury, or asphyxiation caused by refrigerant leakage.
●
In order to prevent damage to the flare caused by over-
tightening of the flare nuts, use the table above as a guide
when tightening.
●
When tightening the flare nut on the liquid tube, use an
adjustable wrench with a nominal handle length of 200 mm.
5-3. Insulating the Refrigerant Tubing
Tubing Insulation
●
Thermal insulation must be applied to all units tubing,
including distribution joint (field supply).
* For gas tubing, the insulation material must be heat
resistant to 120°C or above. For other tubing, it must be
heat resistant to 80°C or above.
Insulation material thickness must be 10 mm or greater.
If the conditions inside the ceiling exceed DB 30°C and RH
70%, increase the thickness of the gas tubing insulation
material by 1 step.
Two tubes arranged together
Liquid tubing
Gas tubing
Insulation
Fig. 5-7
CAUTION
If the exterior of the outdoor unit valves has been finished
with a square duct covering, make sure you allow sufficient
space to access the valves and to allow the panels to be
attached and removed.
Taping the fl are nuts
Wind the white insulation tape around the flare nuts at the gas
tube connections. Then cover up the tubing connections with
the flare insulator, and fill the gap at the union with the supplied
black insulation tape. Finally, fasten the insulator at both ends
with the supplied vinyl clamps. (Fig. 5-8)
Flare insulator (supplied)
Insulation tape
(supplied)
Tube insulator
(not supplied)
Heat resistant
120°C or above
Flare union
Flare nut
Unit side
Fig. 5-8
Insulation material
The material used for insulation must have good insulation
characteristics, be easy to use, be age resistant, and must not
easily absorb moisture.
CAUTION
After a tube has been insulated, never try to bend it into
a narrow curve because it can cause the tube to break or
crack.
Never grasp the drain or refrigerant connecting outlets
when moving the unit.
5-4. Taping the Tubes
(1) At this time, the refrigerant tubes (and electrical wiring
if local codes permit) should be taped together with
armoring tape in 1 bundle. To prevent condensation from
overflowing the drain pan, keep the drain hose separate
from the refrigerant tubing.
(2) Wrap the armoring tape from the bottom of the outdoor
unit to the top of the tubing where it enters the wall. As you
wrap the tubing, overlap half of each previous tape turn.
(3) Clamp the tubing bundle to the wall, using 1 clamp approx.
each meter. (Fig. 5-9)
Insulated tubes
Drain hose
Clamp
Fig. 5-9
N OT E
Do not wind the armoring tape too tightly since this will
decrease the heat insulation effect. Also ensure that the
condensation drain hose splits away from the bundle and drips
clear of the unit and the tubing.
Pana̲indoor̲all.indb 17
Pana̲indoor̲all.indb 17
2013/12/16 15:15:17
2013/12/16 15:15:17
AMP Air Conditioning
www.ampair.co.uk | [email protected]