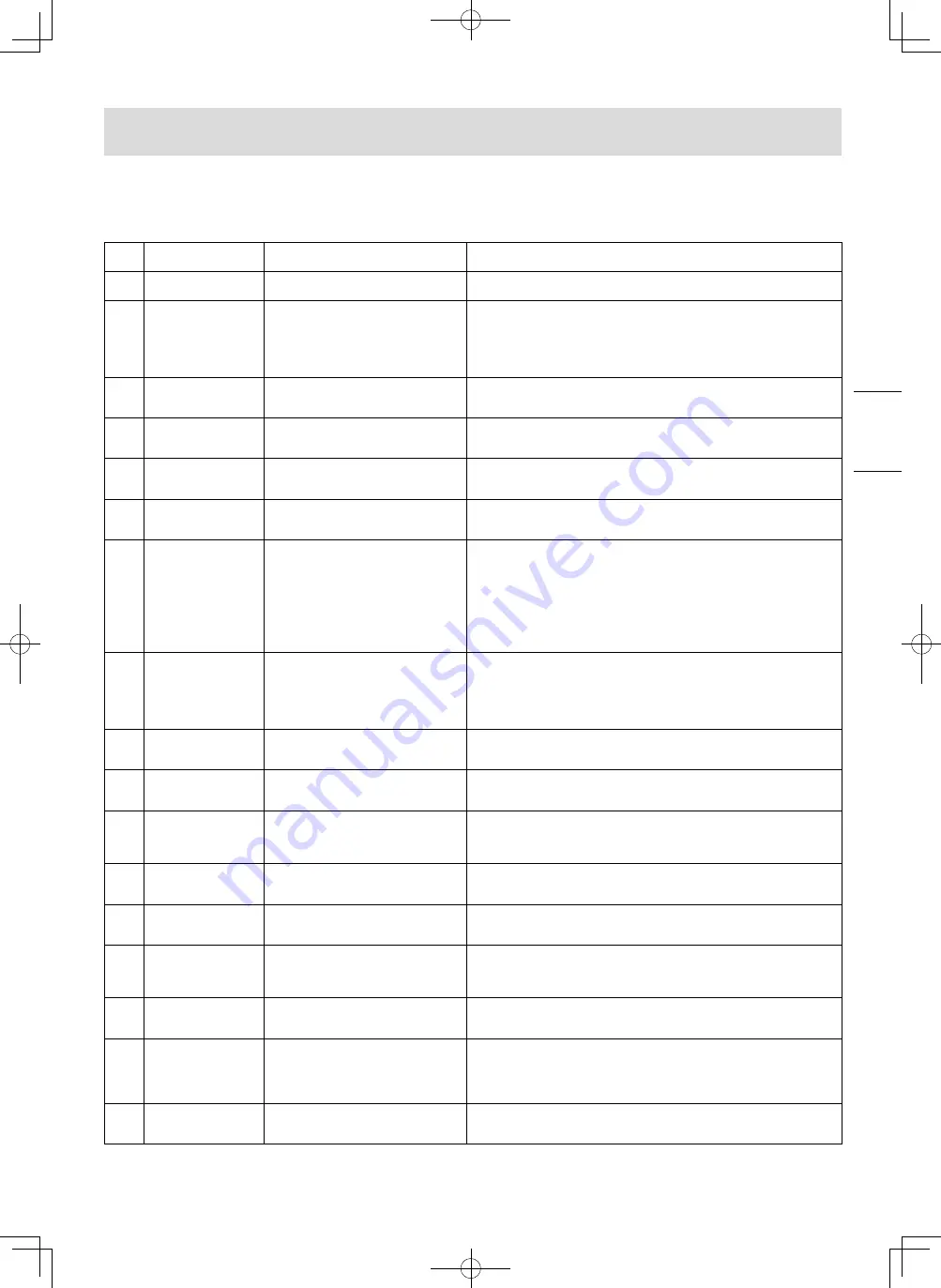
EN - 47
EN - 46
ENGLISH
Error Code
(1) When the rotary switch (knob) is at [OPERATION] position, the digital display on the control PCB alternately
displays low pressure, high pressure and error code (E ***).
< Error Code Table >
Error
code
Meaning
Cause
Correction method
E011 High pressure
anomaly (7th incident)
Increased high pressure caused a high
pressure anomaly.
(1) Investigate the cause of high pressure anomaly.
(2) Check for the presence of any anomalies of the high pressure sensor.
E031
Discharge gas
temperature anomaly
(3rd incident)
Abnormal stop caused by increased
discharge temperature to 118°C or
higher occurred three times in two
hours.
Follow the procedure shown in “Failure Diagnosis at the time of Abnormal
Discharge Gas Temperature.”
(1) Search for the cause of increasing discharge gas temperature.
(2) Check the connection of control PCB “2P4 discharge 1 connector.”
(3) Check the resistance value of the discharge gas temperature sensor
(Refer to “Method of Checking Sensor Characteristics”).
E041
Discharge gas
temperature sensor
anomaly
Discharge gas temperature sensor
became abnormal (open circuit
condition).
(1) Check the connection of control PCB “2P4 discharge 1 connector.”
(2) Check the resistance value of the discharge gas temperature sensor
(Refer to “Method of Checking Sensor Characteristics”).
E05 Low pressure sensor
anomaly
Low pressure sensor became
abnormal (open circuit condition).
(1) Check the connection of control PCB “3P1 low pressure connector.”
(2) Check the output voltage of the low pressure sensor (Refer to “Method
of Checking Sensor Characteristics”).
E06 High pressure sensor
anomaly
High pressure sensor became
abnormal (open circuit condition).
(1) Check the connection of control PCB “3P3 high pressure connector.”
(2) Check the output voltage of the high pressure sensor (Refer to
“Method of Checking Sensor Characteristics”).
E07
Suction gas
temperature sensor
anomaly
Suction gas temperature sensor
became abnormal (open circuit
condition).
(1) Check the connection of control PCB “2P9 U inlet connector.”
(2) Check the resistance value of the suction gas temperature sensor
(Refer to “Method of Checking Sensor Characteristics”).
E091 Oil level anomaly
Low oil level condition continued for
10 min.
(1) Investigate the cause of oil level anomaly.
(2) Check the connection of control PCB “6P11 electronic expansion valve
1 connector.”
(3) Check the coil attachment condition and resistance value of the oil
control electronic expansion valve (MOV1).
When checking, refer to “Method of Checking the Resistance of
Electronic Expansion Valve Coil and Oil Level Switch.”
(4) Check the oil level and add oil according to the “Oil Level Control
Method.”
E101
Discharge gas
temperature anomaly
(1st to 2nd incident)
Discharge gas temperature increased
to 118°C or higher and generated
an abnormal stop. Or discharge gas
temperature sensor shorted.
Comply with the “Failure Diagnosis at the time of Abnormal Discharge
Gas Temperature.”
(1) Search for the cause of increasing discharge gas temperature.
(2) Check the connection of control PCB “2P4 discharge 1 connector.”
(3) Check the resistance value of the discharge gas temperature sensor
(Refer to “Method of Checking Sensor Characteristics”).
E181,
E183
Inverter
communication
anomaly
No serial communication signal
between “control PCB” and “Inverter”
Check the communication line between control PCB “5P1 connector” and
Inverter A1000/V1000 connector.”
E19
Controller
communication
anomaly
No controller signal exists in
communication.
(1) Check the communication line (control PCB “5P4, 5P5 connector”).
(2) Set the communicating refrigeration unit No. to a value other than “0.”
E201
Radiator temperature
anomaly
Inverter radiator temperature increased
to 100°C or higher and stopped
abnormally.
(1) Investigate the cause of the increasing radiator temperature.
(2) Check the connection of control PCB “2P31 Cooler 1 connector.”
(3) Check the resistance value of the radiator temperature sensor (Refer
to “Method of Checking Sensor Characteristics”).
E221
Radiator temperature
sensor anomaly
Radiator temperature sensor became
abnormal (open circuit condition).
(1) Check the connection of control PCB “2P31 Cooler 1 connector.”
(2) Check the resistance value of the radiator temperature sensor (Refer
to “Method of Checking Sensor Characteristics”).
E23 Ambient temperature
sensor anomaly
Ambient temperature sensor became
abnormal (open circuit condition).
(1) Check the connection of control PCB “2P8 ambient air connector.”
(2) Check the resistance value of the ambient temperature sensor (Refer
to “Method of Checking Sensor Characteristics”).
E271 Gas cooler fan motor
anomaly
Gas cooler fan motor became
abnormal. (The fan rotation speed
significantly deviated from the set
rotation speed.)
(1) Check for the presence of a fan lock, fan dislocation, etc.
E311
High pressure
anomaly (1st to 6th
incident)
Increased high pressure caused a high
pressure anomaly.
(1) Investigate the cause of high pressure anomaly.
(2) Check for the presence of any anomalies of the high pressure sensor.
E32 Refrigerant flood back
alarm
Suction gas superheat (difference
between “suction gas temperature” and
“evaporating temperature calculated
from low pressure”) became 1 K or
below continuously for 2 min.
Check the cause of refrigerant flood back operation.
E36
Intermediate pressure
anomaly (1st to 6th
incident)
Increased intermediate pressure
caused an abnormal intermediate
pressure.
(1) Investigate the cause of intermediate pressure anomaly.
(2) Check for the presence of any anomalies of the intermediate pressure
sensor.
Failure Diagnosis
01_OCU-CR1000VF8A.indd 47
2019/08/27 10:56:09