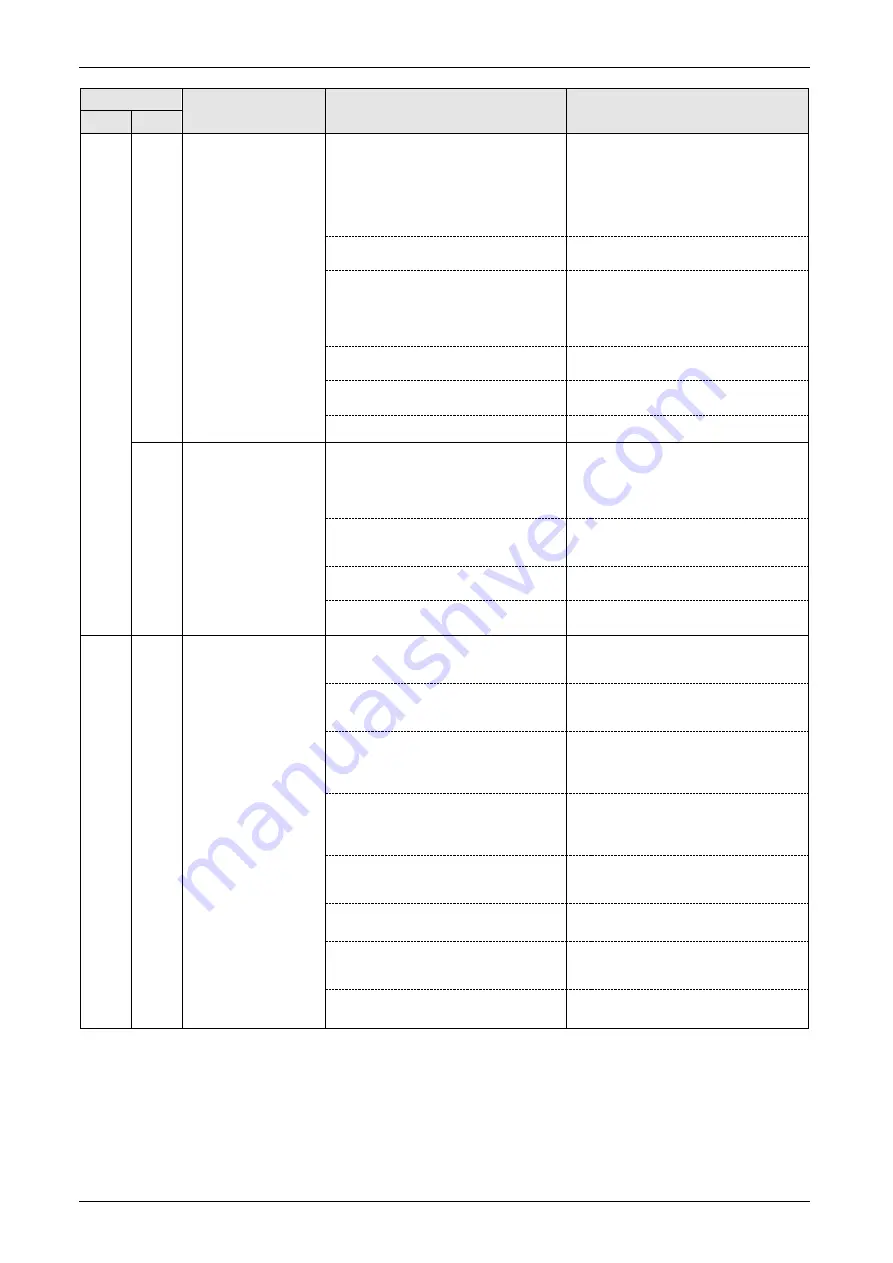
7.2Details of protective function
7-7
Error No.
Protective function
Causes
Measures
Main
Sub
13
0
DC busundervoltage
protection
(When bit 0 of Pr5.08 “L/V trip selection
upon main power off” of the driver module, if
any axis of the driver module is servo-on,
the bus bar (main power) voltage is
insufficient voltage level In the driver
module or power module. It was detected
that it decreased to the following.
Measure the applied voltage of main power
connector X102.
Check if the voltage is insufficient.
1) Instantaneous power failure has
occurred.
1) Change to the main power supply
2) Lack of power capacity...Power supply
voltage has fallen down due to inrush
current at the main power-on.
2) Increase the power capacity. For the
capacity, refer to Reference
specification SX-DSV03451 "Driver
and List of Applicable Peripheral
Equipments" of Preparation.
3) Failure of driver module (failure of the
circuit)
3) Replace the driver module.
4) Power supply module failed (circuit
failure).
4) Replace the power supply module.
5) Contact failure in bus bar
5) Check the connection of bus bar.
1
Main power supply
undervoltage protection
(AC)
On the servo-on axis of the driver module,
the power supply module detected the main
power AC400V input shut-off status for the
time set in PSM Pr.02 “Main power off
detection time”.
Measure the applied voltage of main power
connector X102.
Check if there is an instantaneous power
outage or phase loss.
1) Instantaneous power failure has
occurred.
1) Set up the longer time to PSM Pr.02
(Main power off detecting time). Set up
each phase of the power correctly.
2) Failure of driver module (failure of the
circuit)
2) Replace the driver module.
3) Power supply module failed (circuit
failure).
3) Replace the power supply module.
14
0
Over-current protection
The current flowing through the converter
part of each axis of the driver module
exceeded the specified value.
Remove the cause of overcurrent.
1) Failure of driver module (failure of the
circuit, IGBT or other components)
1) Turn to Servo-ON, while disconnecting
the motor. If error occurs immediately,
replace with a new driver module.
2) Short of the motor wire (U, V and W)
2) Check that the motor wire (U, V and W)
is not shorted, and check the branched
out wire out of the connector. Make a
correct wiring connection.
3) Earth fault of the motor wire
3) Measure the insulation resistance
between motor wires, U, V and W and
earth wire. In case of poor insulation,
replace the motor.
4) Burnout of the motor.
4) Check the balance of resister between
each motor line, and if unbalance is
found, replace the motor.
5) Poor contact of the motor wire.
5) Check the loose connectors. If they
are, or pulled out, fix them securely.
6) Welding of relay contact for dynamic
braking due to frequent servo ON/OFF
operations.
6) Replace the driver module. Do not use
servo ON/OFF during operation.
7) Timing of command input is same as or
earlier than Servo-ON.
7) Enter the commands 100 ms or longer
after Servo-ON.
(To be continued)
Содержание MINAS A6 Series
Страница 10: ...Table of contents x Blank page...
Страница 11: ...1 Introduction...
Страница 26: ...Introduction 1 16 Blank page...
Страница 27: ...2 Interface Specifications...
Страница 46: ...Interface Specifications 2 20 Blank page...
Страница 47: ...3 Front Panel Specifications...
Страница 48: ...Front Panel Specifications 3 2 3 1 Front panel configuration Front panel cover opened Front panel cover closed...
Страница 57: ...4 Basic Functions...
Страница 85: ...5 Auto Tuning Functions...
Страница 151: ...6 Application Functions...
Страница 185: ...7 Protective Functions...
Страница 224: ...Protective Functions 7 40 Blank page...
Страница 225: ...8 Advanced Safety Functions...
Страница 230: ...Advanced Safety Functions 8 6 When test pulse is used Duplex safety input Safety input...
Страница 245: ...9 List of Parameters...
Страница 281: ...10 Timing Chart...
Страница 290: ...Timing Chart 10 10 Blank page...
Страница 291: ...11 Power Supply Module...