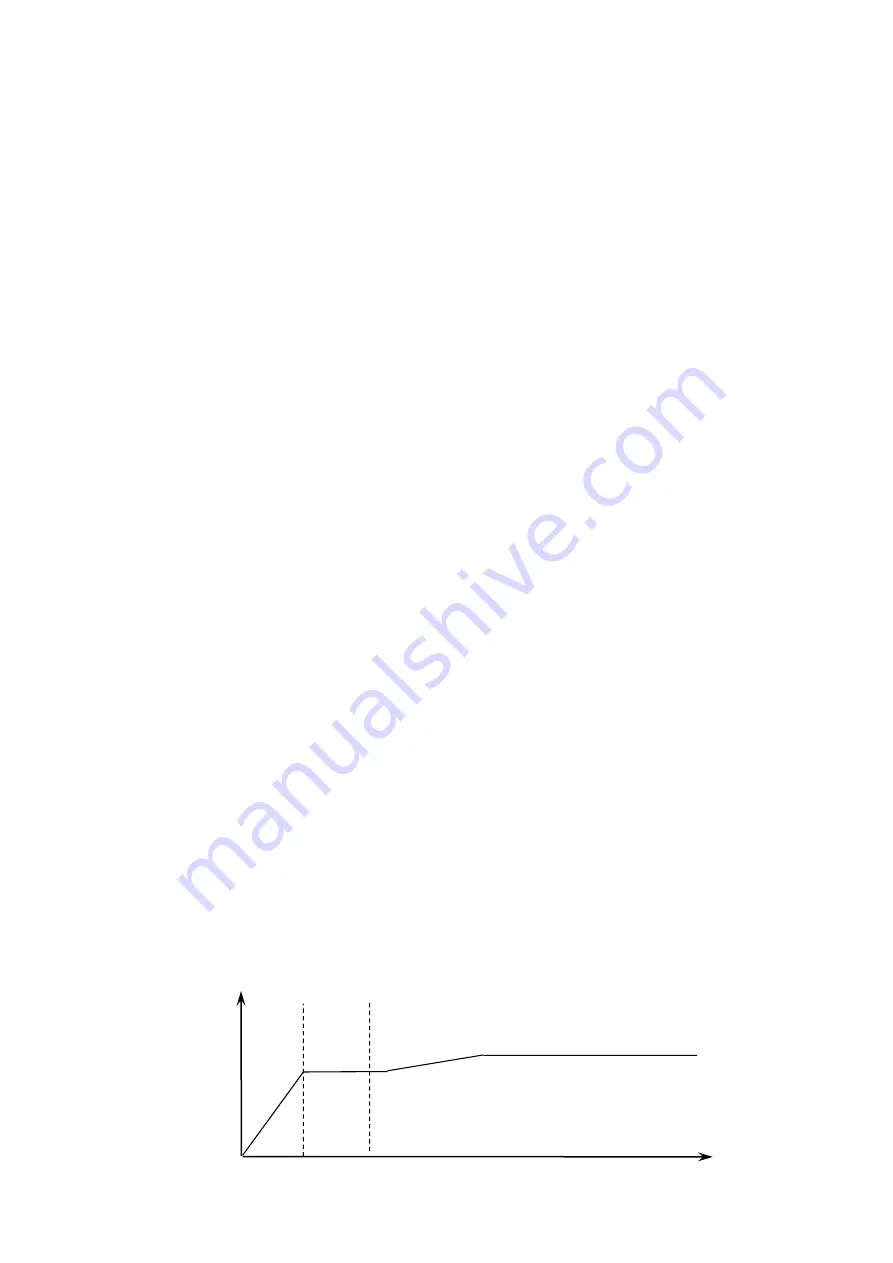
12
3.2 Selection of Inverter Driver
The function of inverter driver is to power the compressor, control the compressor running speed, protect
compressor from abnormal situations and communicate with master controller.
Make sure to choose a suitable quality inverter driver which have been passing performance test with
compressor.
A third-party driver can be used. To get the best system efficiency and reliability, consult your account
representative to verify the match of driver setting and BLDC motor parameters.
The following factors should be considered when select a driver:
1)
Driver size should match with maximum current of compressor;
2)
Driver should have compressor protection functions including discharge temperature protection, over-
current protection, reverse phase protection, loss of phase protection etc.
3)
Driver should have function to skip some specific frequency range to avoid piping resonance.
4)
Frequency limit control
When the output current of driver increases to close to the over-current protection value, the
compressor frequency should be reduced, and the compressor should be restricted from high-
frequency operation to avoid frequent fluctuations.
Compressor smoothly operation depends on a certain voltage input; the higher the speed, the higher
the voltage required. During the operation, when the output voltage of the inverter is low, it should
reduce the frequency and limit the compressor from high frequency operation to avoid stall and
shutdown of compressor.
5)
Electromagnetic noise may occur due to inverter characteristics. To adjust carrier frequency can reduce
electromagnetic noise level
3.3 Starting and maximum current of compressor
Starting current and maximum current shall be within the range mentioned in the compressor specification.
In the case of inverter compressor, if the current is over the limitation, DC brushless motor will be
demagnetized and compressor will not be started.
The over current protection must be set on the inverter driver. The protection value setting is subject to
compressor’s demagnetization current. Once an over current occurs, the driver should shut down the
compressor for more than 3minutes from next start up.
3.4 Starting of compressor
In the case of inverter compressor, operation at rather low frequency after starting is necessary to avoid
insufficient lubrication due to low oil level.
Figure 3-2 Starting
1min
50~70 rps
Time
f(rps)
Rotation
speed