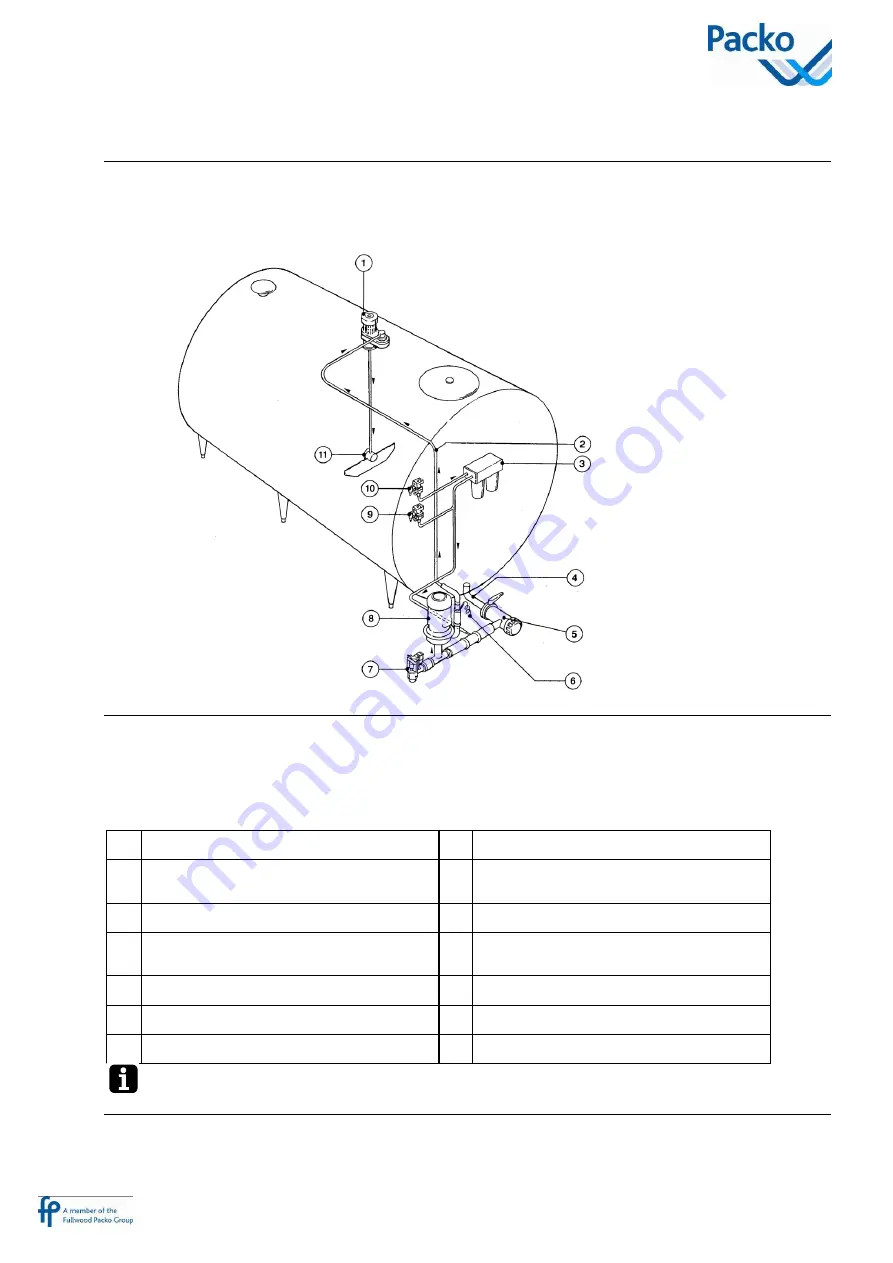
66/78
06/02/2008
1.00
The standard automatic cleaning system
Picture
This drawing represents the standard automatic cleaning system.
Parts
The table below provides an overview of the parts of the standard cleaning system. The arrows indicate the
flow of the cleaning water.
N°
Description
N°
Description
1
Agitator motor with rotating water
coupling
7
Dump valve
2
Pressure pipe
8
Cleaning pump
3
Water box with dosage cups (second
container = option)
9
Cold water inlet valve
4
Outlet tank
10
Hot water inlet valve
5
Self washing outlet
11
Roto-Jet Spray ball
6
Level sensor for the cleaning water
The standard automatic cleaning cycle can also be equipped with automatic dosage.