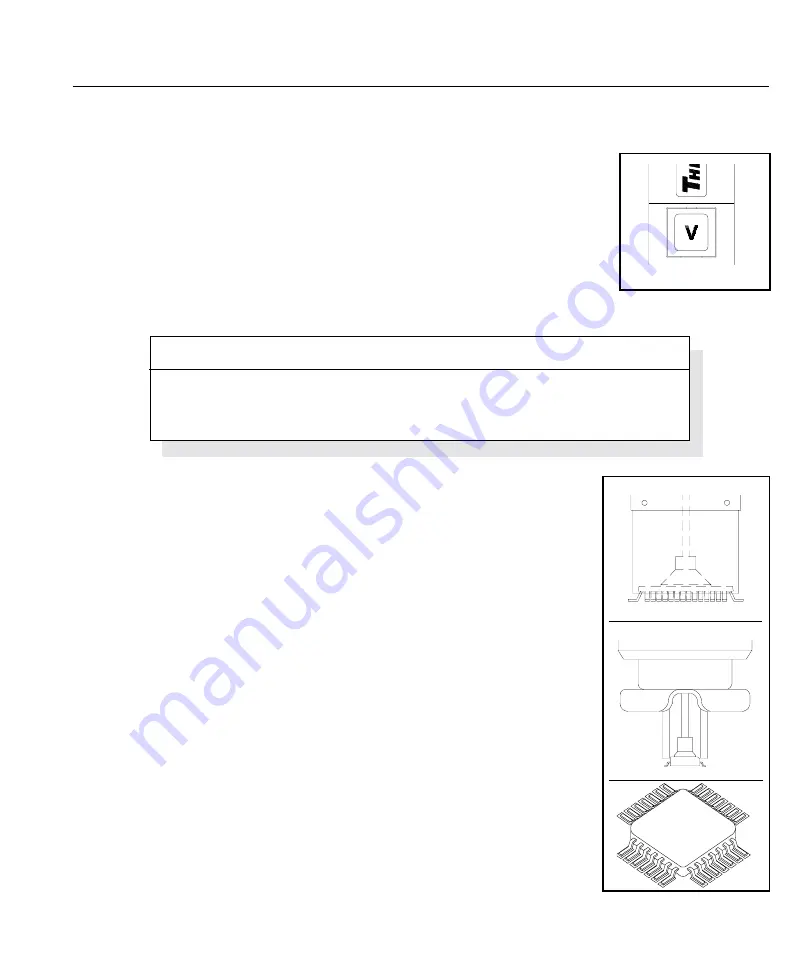
Figure 33.
Handpiece
6. Press and release Vacuum Pick Switch to activate vacuum.
NOTE
As an alternative to the component placement methods shown below in steps 7
through 10, the component (except BGAs) may be positioned and solder tacked
in place on land pattern. See “Component Positioning”.
Figure 34.
7. Position replacement component directly beneath and square to nozzle.
When using Box or V-A-N nozzles, insert component body into the
bottom of the nozzle. BGA components will rest against the walls of
the nozzle.
When using a Curved, Single Jet nozzle, position the component on its
land pattern (prefilled or with solder paste deposition). Solder tack
lead(s) if necessary.
When using Pattern nozzles, position component leads beneath and in
line with the air jets on the nozzle.
37
Operation
MANUAL MODE COMPONENT INSTALLATION (CONT'D)
Содержание TF 200
Страница 1: ...OPERATION MAINTENANCE MANUAL PROGRAMMABLETHERMOFLO TF 500 TF 500E Systems TF 200 TF 200E Units ...
Страница 2: ...MANUAL NO 5050 0420 REV C i ...
Страница 26: ...21 Quick Start ...