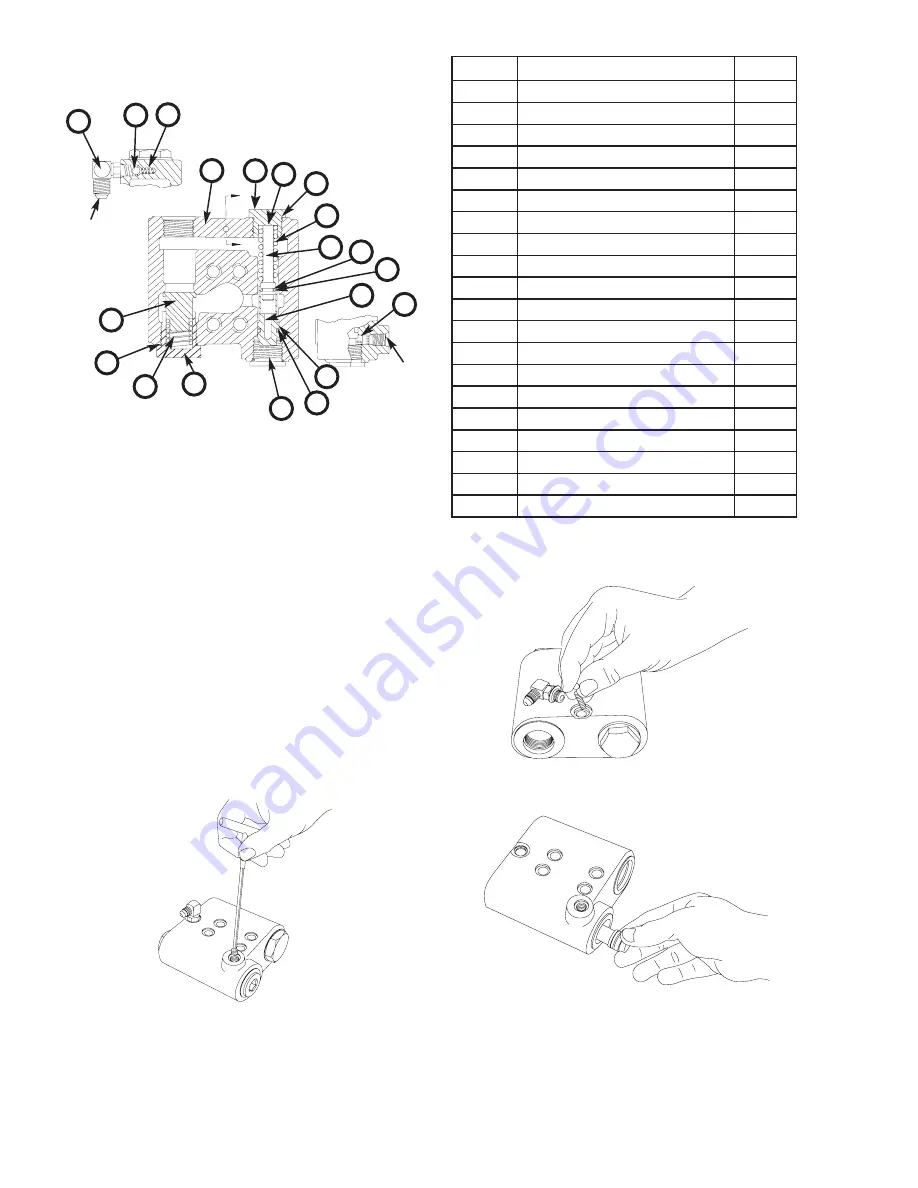
32
Th
e BRADEN brake valve is a reliable hydraulic valve with
internal components manufactured to close tolerances. Due
to the close tolerances and mating of components, the valve
housing, spool, piston and check poppet are not available as
replacement parts.
Before disassembling the brake valve, be sure you have con-
ducted all applicable troubleshooting operations and are cer-
tain the brake valve is causing the malfunction.
Th
oroughly clean the outside surfaces of the valve and work
in a clean dust free area, as cleanliness is of utmost impor-
tance when servicing hydraulic components.
DISASSEMBLY
1. Remove the pilot ori
fi
ce from the brake release (BR) port
using a 5/32 in. Allen wrench.
2. Remove the elbow
fi
tting, motor drain check ball and
spring.
3. Remove the spool spring retainer and spool spring. Check
spring free length. Replace spring if less than 1 15/16 in.
(49.2 mm) long.
4. Remove spool plug and carefully remove spool assembly.
BRAKE VALVE SERVICE
A
A
SEC. A-A
DRAIN
PORT
3
1
2
4
5
6
14
16
11
12
10
7
8
9
13
15
18
17
19
“BR”
PORT
22
ITEM DESCRIPTION
QTY
1
BRAKE VALVE HOUSING
NSS
2
VALVE SPRING RETAINER
1
3
SPRING RETAINER
1
4
PLUG
1
5
SPOOL
NSS
6
DAMPER PISTON
NSS
7
O-RING
2
8
CHECK VALVE POPPET
NSS
9
PILOT ORIFICE
1
10
CHECK VALVE SPRING
1
11
SPOOL SPRING
1
12
O-RING
1
13
O-RING
1
14
O-RING
1
15
BACK-UP RING
1
16
BACK-UP RING
1
17
STEEL BALL
1
18
COMPRESSION SPRING
1
19
ELBOW FITTING
1
22
SHIM, VALVE SPRING
AR
NSS
- NOT SOLD SEPARATELY - REPLACE COMPLETE
VALVE ASSEMBLY
AR
- AS REQUIRED
Содержание Braden PD12C
Страница 37: ...37...
Страница 38: ...38 THIS PAGE INTENTIONALLY LEFT BLANK...
Страница 40: ...40 LIT2103 R6 July 2017 Printed in USA 2017 PACCAR Inc All rights reserved...