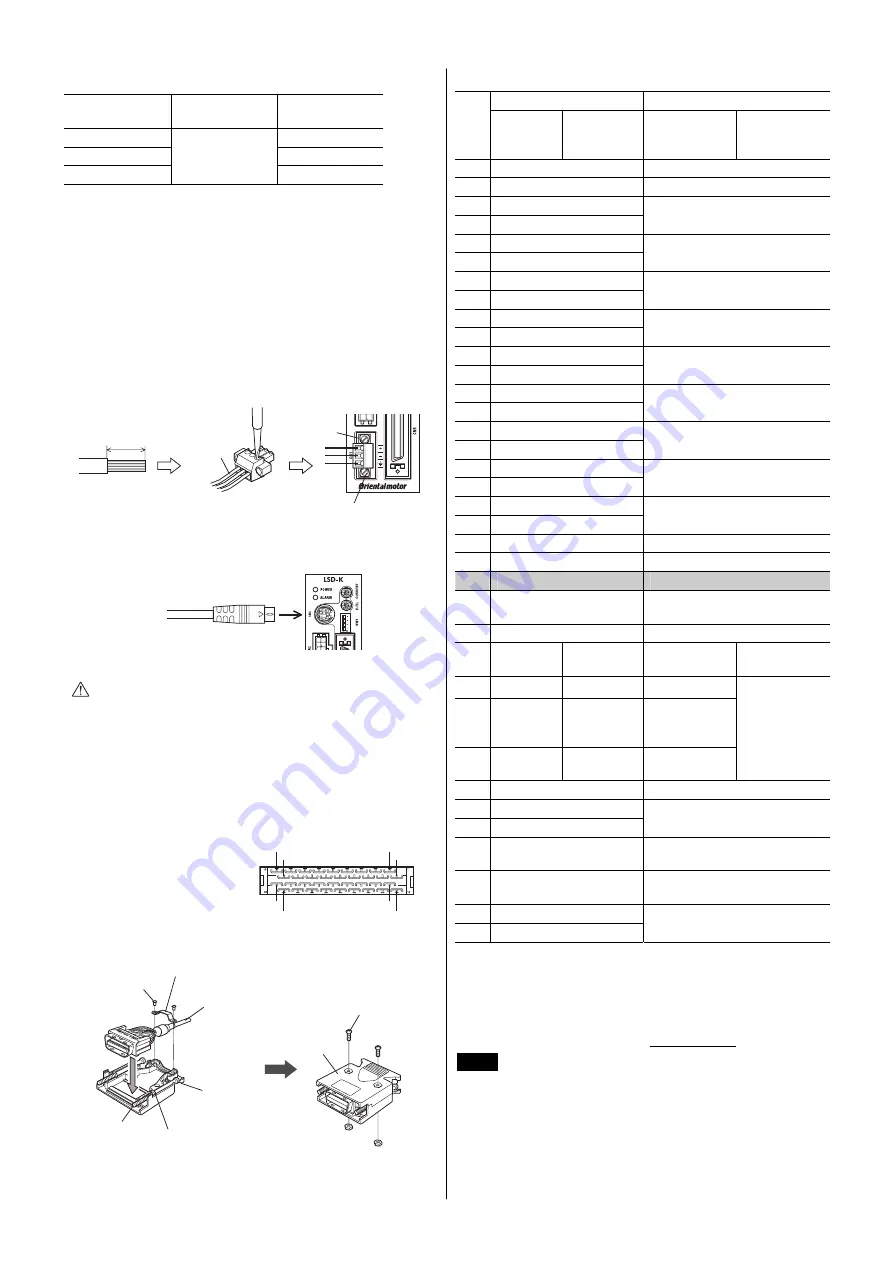
4
Power supply current capacity
Model
Input power
supply voltage
Power supply
current capacity
DG60
0.9 A or more
EAS4
1.4 A or more
EAS6
24 VDC±10%
3.1 A or more
CN1
1.
Strip the insulation cover of the lead wire by 7 mm (0.28 in.)
2.
Insert each lead wire into the CN1 connector and tighten the
screw using a screwdriver.
Connector screw size: M2
Tightening torque: 0.22 to 0.25 N·m (31 to 35 oz-in)
3.
Insert the CN1 connector into CN1 on the driver and tighten the
screws.
Connector screw size: M2.5
Tightening torque: 0.4 N·m (56 oz-in)
7 mm (0.28 in)
CN1 connector
Tightening torque: 0.4 N·m (56 oz-in)
Lead wire
CN1
CN4
Connect to CN4
Cable for
OPX-2A
or
communication cable for data
setting software
Caution
The power supply connector (CN1), data edit
connector (CN4) and I/O signals connector (CN5)
are not electrically insulated. When grounding the
positive terminal of the power supply, do not
connect any equipment (PC, etc.) whose negative
terminal is grounded. Doing so may cause the
driver and these equipment to short, damaging
both.
CN5
Connector pin assignment
(viewed from soldering side)
1
2
17
18
19
20
35
36
•
Assembling the connector
I/O signal cable
Cable clamp
Screw (M2.5)
Case
Connector
Place the spring
washer outside
the case.
Screw (M2)
Screw (M2.5)
Tightening torque:
0.5 to 0.55 N·m
(71 to 78 oz-in)
Align the washer in the
depression in the case.
•
Pin assignment
Operating
mode
Name
Pin
No.
Positioning
operation
Push-motion
operation
∗
1
∗
3
Positioning
operation
Push-motion
operation
∗
1
∗
3
1
−
−
2 GND
Ground
connection
3 ASG+
4 ASG
−
A-phase pulse output
(Line driver)
5 BSG+
6 BSG
−
B-phase pulse output
(Line driver)
7 TIM1+
8 TIM1
−
Timing output (Line driver)
9 ALM+
10
ALM
−
Alarm output
11
WNG+
12
WNG
−
Warning output
13
END+
14
END
−
Positioning completion output
15
READY+/AL0+
∗
1
16
READY
−
/AL0
−
∗
1
Operation ready complete
output/Alarm code output 0
17
TLC+/AL1+
∗
1
18
TLC
−
/AL1
−
∗
1
Torque limit output/
Alarm code output 1
19
TIM2+/AL2+
∗
1
20
TIM2
−
/AL2
−
∗
1
Timing output (Open collector)/
Alarm code output 2
21
GND Ground
connection
22
IN-COM Input
common
23
C-ON
∗
2
Current ON input
24
CLR/ALM-RST
Deviation clear input/
Alarm reset input
25
CCM
Current control mode ON input
26
CS
T-MODE
∗
1
∗
3
Resolution
selection input
Push-motion
operation ON
27
−
M0
∗
1
∗
3
−
28
RETURN
M1
∗
1
∗
3
Return to
electrical home
operation
29
P-RESET
M2
∗
1
∗
3
Position reset
input
Push-current
setting
selection input
30
FREE Excitation
OFF
31
CW+/PLS+
32
CW
−
/PLS
−
CW pulse input/
Pulse input (+5 V or line driver)
33
CW+24 V/PLS+24 V
CW pulse input/
Pulse input (+24 V)
34
CCW+24 V/DIR+24 V
CCW pulse input/
Direction input (+24 V)
35
CCW+/DIR+
36
CCW
−
/ DIR
−
CCW pulse input/ Direction input
(+5 V or line driver)
∗1
The signal will become effective if the applicable setting has been
changed using the
OPX-2A
or
MEXE02
.
∗2
Factory setting of the C-ON input logic is "normally open." Be sure to
turn the C-ON input ON when operating the actuator. Set the C-ON input
logic to "normally closed" when the C-ON input is not used.
∗3
These signals are used to perform push-motion operation. Do not set
with the
DG
Ⅱ
Series. Refer to the USER MANUAL for details.
Note
•
The driver I/O signals of the
DG
Ⅱ
Series and
EAS
Series are in common with those of the
AR
Series,
but the signals are not compatible with the drivers of
other series. Do not connect the I/O signals with pin
assignments of other series.
•
Do not perform push-motion operation or sensorless
return-to-home operation with the
DG
Ⅱ
Series.
Doing so may result in damage to the actuator.