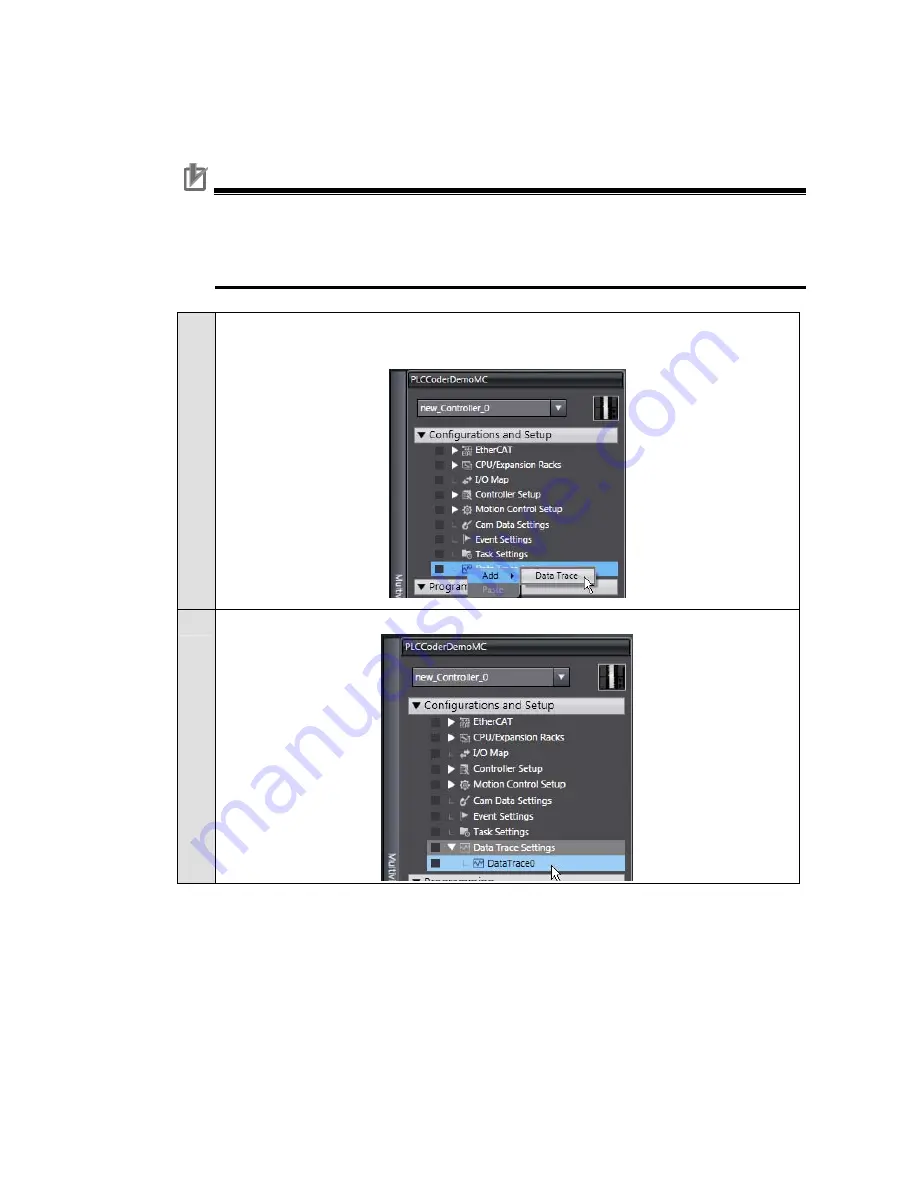
3.2.8.
System Operation Check
You execute the operation according to the programs transferred to the physical CPU Unit and
check the operation using the data trace function.
Precautions for Correct Use
The physical motor will run. Thoroughly read and understand the manuals for all devices
that make up the system to ensure that the system is used safely. Review the entire
contents of these manuals, including all safety precautions, precautions for safe use,
and precautions for correct use before the actual operation.
1
Right-click the
Data Trace Settings
in the Multiview Explorer and select
Add
-
Data
Trace
from the menu to add DataTrace0.
2
Double-click
DataTrace0
that you added.
30
Содержание DA0271
Страница 38: ...2013 0613 W529 E1 01...