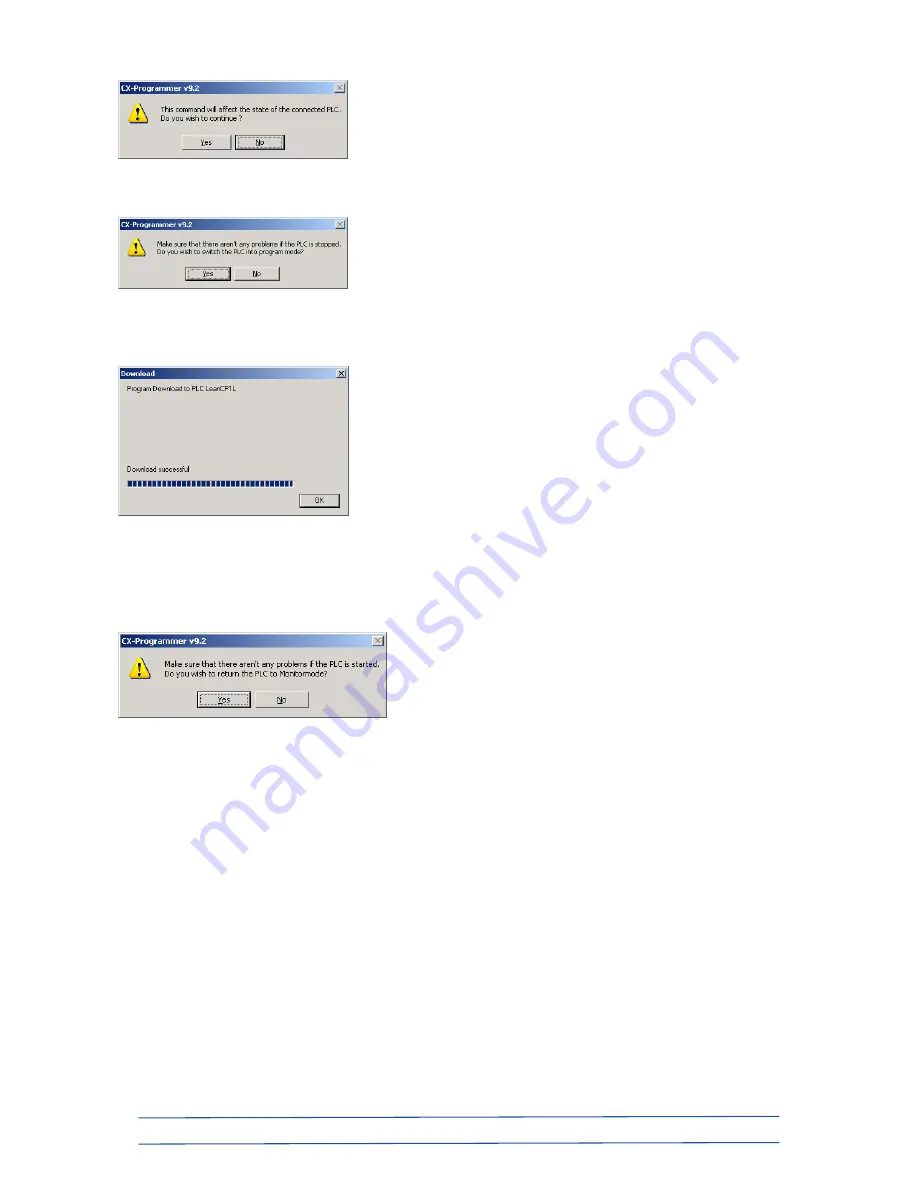
OMRON ELECTRONICS LTD
●
Technical Support: 0870 752 0871 or visit www.myOMRON.com
28
Click
Yes
again…
It will take no more than about 5 seconds to download the entire PLC application. Upon
completion, click
OK
…
If you see this message below, click
Yes
to return the PLC to Monitormode (Run).
If this is the first time you have used this PLC, at this point you will have to remove the
power to it, then re-power. With either of the above, the PLC’s POWER and RUN LED
indicators should both be lit green.
Now follow the next steps to download the application to the NQ3 HMI…