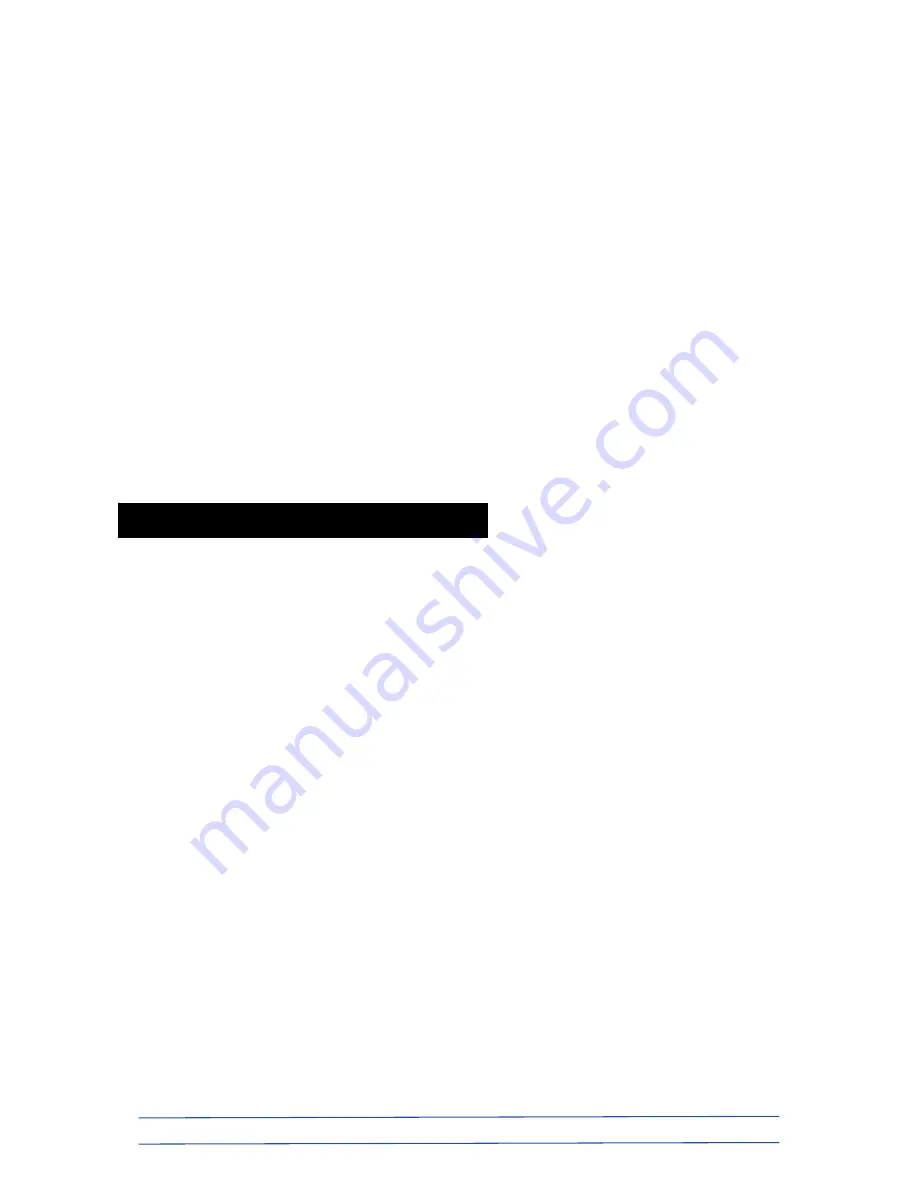
OMRON ELECTRONICS LTD
●
Technical Support: 0870 752 0871 or visit www.myOMRON.com
17
Connecting the control I/O signals between the SmartStep2 and PLC;
The PLC provides output signals to the SmartStep2 for RUN, RESET, ECRST (deviation
counter reset), CW (clockwise pulses) and CCW (counter-clockwise pulses).
The SmartStep2 provides the following signals back to the PLC; /ALM (alarm condition,
normally closed), INP (positioning completed) and Z (encoder Z phase). For 100W, 200W
and 400W SmartStep2 servo amplifiers, these output signals are NPN only. To
accommodate this, the PLC inputs are wired accordingly as NPN (sinking), i.e., for the
inputs, the commons are connected to +24VDC
The output signals from the PLC to the SmartStep2 are wired as PNP or NPN, depending
on the CP1L model selected (CP1L-M
□□
DT-D has NPN outputs, CP1L-M
□□
DT1-D has
PNP outputs). Wiring diagrams for both configurations are shown on the next pages, so
be sure to follow the correct one for your chosen CP1L.
The CW (clockwise) and CCW (counter-clockwise) signals into the SmartStep2 amplifier
must be 5V TTL level compatible; as we are working with a 24VDC supply, these levels
must be ‘dropped’ using 2K
Ω
resistors, to prevent damage to the input circuitry. A resistor
module is included with the kit for this purpose. Alternatively, you may prefer to solder
(and heatshrink protect) your own 2K
Ω
resistors in series with the CW and CCW
connections.
Please refer to the diagram overleaf for full wiring details…
1. Cut-back about 25cm of the outer sheathing and braiding from the R7A-CPB001S
control I/O cable.
2. Separate the YELLOW (1 RED BAND) and YELLOW (1 BLACK BAND) wires, twist
these together and connect them (via a screw-terminal block or solder) to the +24V
terminal of the S8VS power supply.
3. Separate the GREY (3 BLACK BANDS), WHITE (3 BLACK BANDS), ORANGE (1
RED BAND), GREY (2 RED BANDS) and GREY (2 BLACK BANDS) wires, twist
these together and connect them (via a screw-terminal block or solder) to the 0V
terminal of the S8VS power supply.
4. Connect the ORANGE (3 RED BANDS) wire to input 0.06 – this is the ‘Z’ output
from the servomotor encoder, used to datum the system.
5. Connect the PINK (1 RED BAND) wire to input 1.04 – this is the ‘ALARM’ signal
(normally closed) which indicates that the system is in error.
6. Connect the PINK (1 BLACK BAND) wire to input 1.05 – this is the ‘IN POSITION’
signal which indicates that the drive has completed its move successfully.
7. Cut the GREY (3 RED BANDS) wire and connect to one side of the resistor module.
Connect the off-cut of this cable to the other side of the resistor module, then to
output 100.00 – this is the ‘CLOCKWISE PULSES’ command signal.
8. Cut the WHITE (3 RED BANDS) wire and connect to one side of the resistor
module. Connect the off-cut of this cable to the other side of the resistor module,
then to output 100.01 – this is the ‘COUNTER CLOCKWISE PULSES’ command
signal.
PNP VERSION FOR CP1L-M30DT1-D