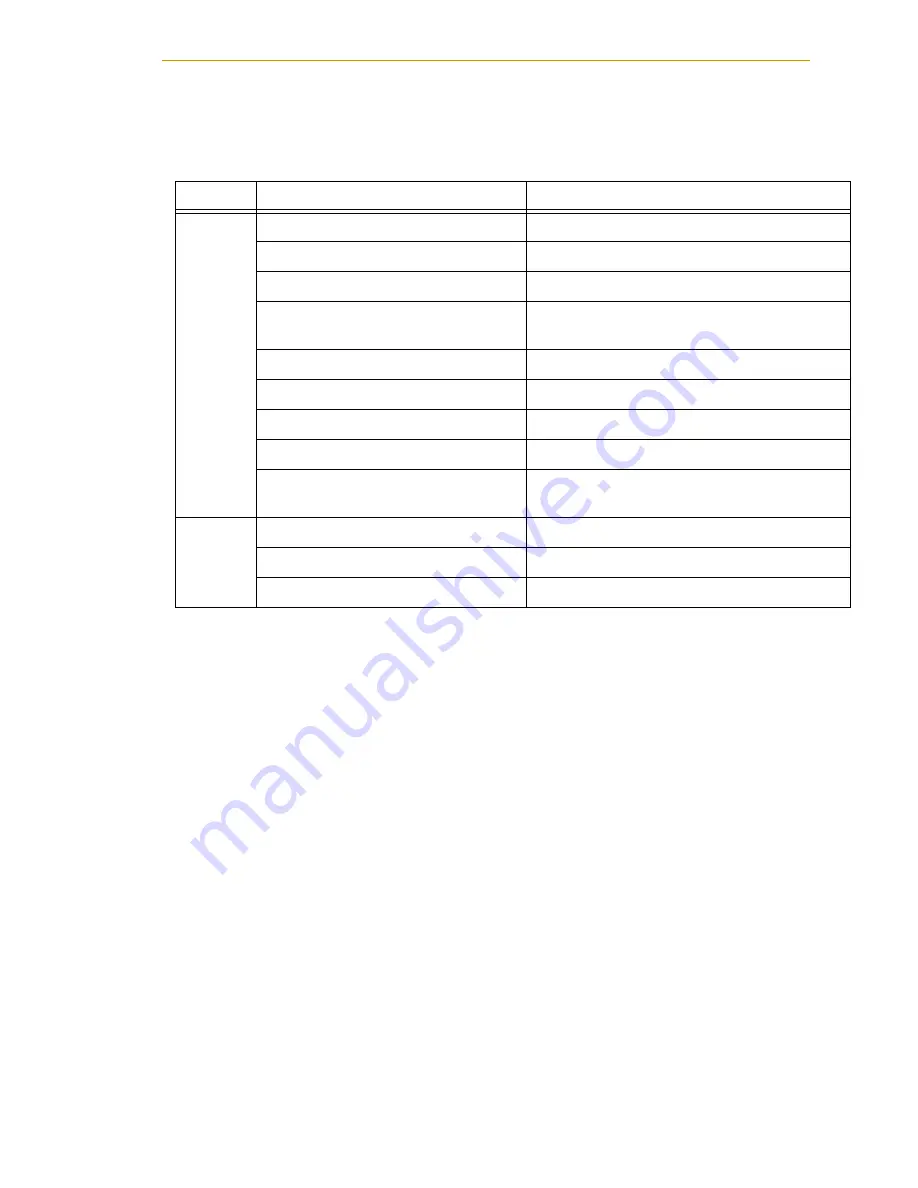
Air Lines and Signal Wiring
Adept Viper s1300 Robot User’s Guide, Rev B
27
Solenoid Valve Specifications
Table 2-4. Solenoid Valve Specifications
Item
Specifications
Valve
Switching system
2-position double
Applicable fluid
Air
Operating system
Pilot type
Effective cross section
(Cv value)
0.27 (P-->A/B) 0.3 (A/B-->EA/EB)
Lubrication
Oilless
Operating pressure range
0.1 to 0.7 Mpa
Response time
10 ms or less (at 0.5 Mpa)
Maximum operating frequency
10 Hz
Ambient temperature
-5 to 50 degrees C (No dew condensation
allowed. When dry air is used)
Solenoid
Operating voltage
24 V ±10%
Power consumption (current)
0.65 W (27 mA)
Surge voltage protection circuit
Diode
Содержание Adept Viper s1300
Страница 1: ...Omron Adept Viper s1300 Robot User s Guide...