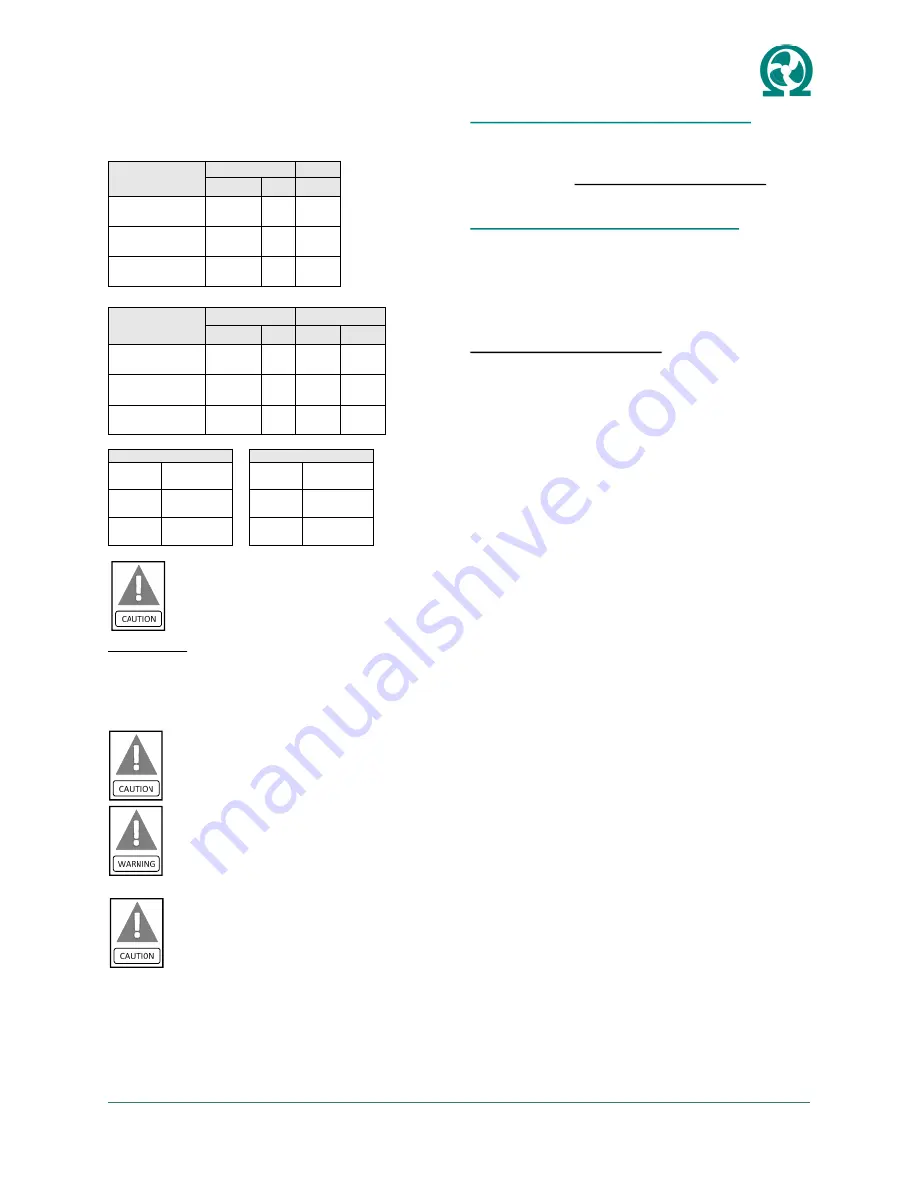
OMEGA-VSHP.F-IOM-1907
www.omega-heatpump.com
8
Operating Limits
Table 2: Unit Operation Limits
Design limits can not be combined. Combin-
ing maximum or minimum limits is not al-
lowed. This could exceed the operation and
design limits of the unit.
For example: It is not allowed to combine maximum en-
tering air temperature (EAT) limits with maximum enter-
ing fluid temperature (EFT) limits.
6. CHASSIS INSTALLATION
Do not apply plumbers putty, pipe dope or
sealing tape to NPSM fittings.
Always use a back-up wrench when tightening
hoses or fittings. Damage to copper pipes and
solder joints could result in serious equipment
and property damage.
Check hoses and fittings for any visible dam-
age or debris.
INSTALLATION OF FITTINGS AND HOSES
Upon removal of service cover panel check cabinet inte-
rior for construction debris and dust. Clean out all dust
and debris.
Close riser shut-off valves and disconnect factory hoses
from riser supply or return shut off valves.
Units with NPSM Riser and Chassis Fittings
Connect the supplied hoses to the Male-NPSM riser
shut-off valves. Do not apply pipe dope or pipe sealant
to NPSM fittings.
Always use a back-up wrench
. Do
not overtighten. See Figure 9: Hose Kit Details.
Units with NPT Riser and Chassis Fittings
Connect the supplied male-male (NPT/ NPSM) cou-
plings to the Female-NPT supply and return riser shut-
off valves. Do not apply pipe dope to the NPSM fittings,
as these are JIC style fittings.
Connect the supplied hoses to the riser shut-off valves.
Always use a back-up wrench
. Do not overtighten.
CHASSIS INSTALL
1. Remove chassis packaging, leaving cardboard ship-
ping cover on the air coil cover in place. Check chassis
nameplate to verify chassis model matches cabinet
model for compatibility.
2. Align chassis with front of the cabinet and tilt chassis
so that the back aligns with the cabinet rails.
3. Slide chassis into cabinet partially. Check to ensure
wiring harnesses are not being pinched. Adjust the chas-
sis to ensure it is resting approximately centered in the
rails.
4. Connect the hoses by hand to the chassis supply and
return connections. Hand tighten, then using a back-up
wrench tighten fittings as necessary. Ensure that the
hose supply and return connections are not reversed
and matched to correct risers. Water IN and water OUT
is stamped on the chassis sheet metal enclosure.
5. If riser loop system has been commissioned and oper-
ational open the riser shut-off valves. Check for any
signs of water leaks at all water connection points.
6. Connect the chassis electrical plugs to the quick con-
nect mating plugs in the cabinet electrical box.
7. Slide the chassis into the cabinet. Check to ensure
wiring harnesses and hoses are not being pinched. Do
not push against the air coil surface.
8. Ensure hoses are not pressed against unit cabinet.
9. Remove cardboard shipping cover from the air coil.
10. Install the service cover panel and visually check
foam gasket around service cover panel perimeter is not
damaged and providing an adequate seal.
11. Insert filter into service cover panel.
12. Install Return Air Panel into the closet drywall open-
ing if not already done and secure with screws.
Air Limits
Cooling
Heating
DB
WB
DB
Std. Entering Air
Temperature (EAT)
75
o
F
63
o
F
68
o
F
Min. Entering Air
Temperature (EAT)
65
o
F
55
o
F
50
o
F
Max. Entering Air
Temperature (EAT)
85
o
F
71
o
F
80
o
F
Fluid Limits
Standard Range
Geothermal Range
Cooling
Heating Cooling
Heating
Std. Entering Fluid
Temperature (EFT)
85
o
F
70
o
F
85
o
F
60
o
F
Min. Entering Fluid
Temperature (EFT)
50
o
F
55
o
F
30
o
F
20
o
F
Max. Entering Fluid
Temperature (EFT)
110
o
F
90
o
F
110
o
F
90
o
F
CFM Limits
Fluid GPM Limits
Min. CFM/
Ton
300
Min. GPM/
Ton
1.5
Design
CFM/Ton
400
Design
GPM/Ton
3
Max. CFM/
Ton
450
Max. GPM/
Ton
4