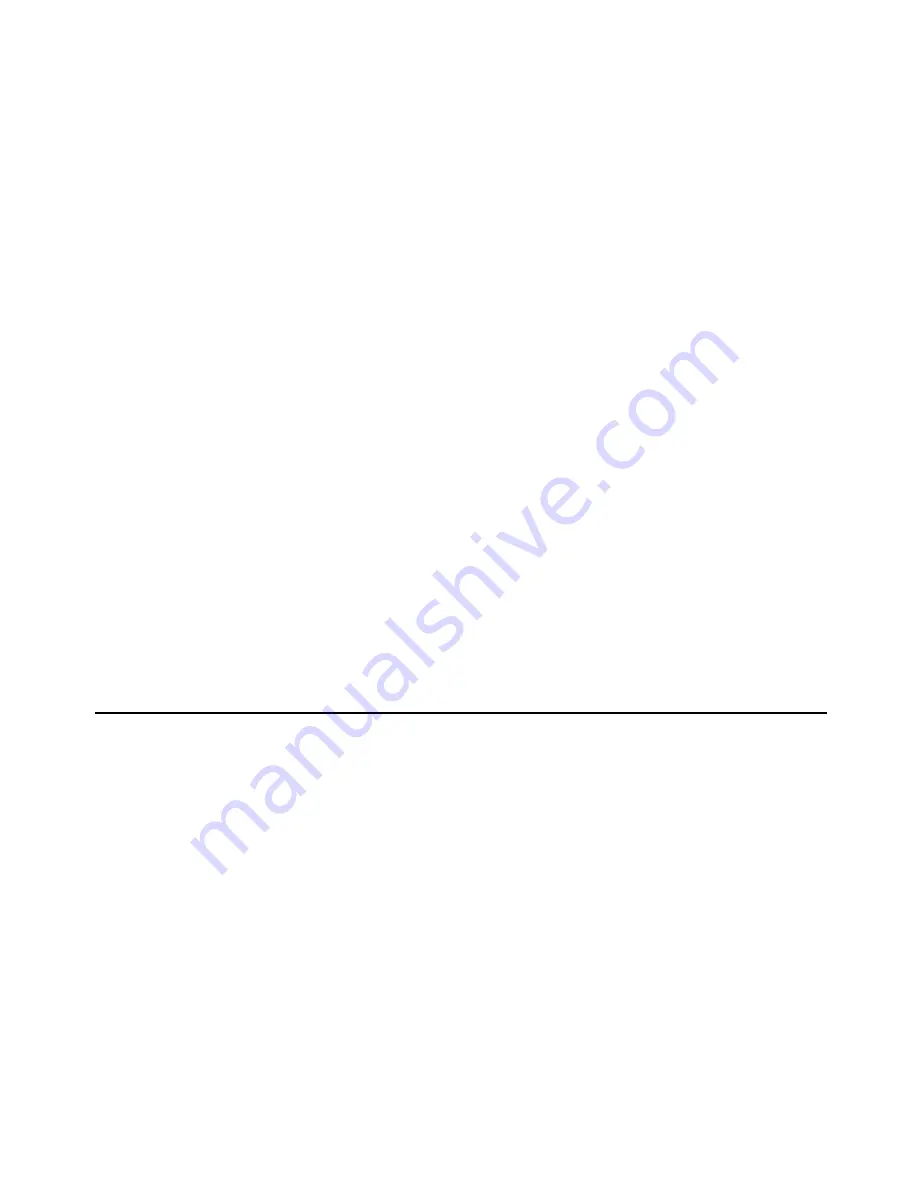
QuantumDrive-4000 Manual 23
91-0027 Rev. E
Copyright © Nutfield Technology, Inc.
6/2010
10. Tuning
NOTE: Each servo driver is factory tuned and matched with a galvanometer and
mirror load. Unauthorized attempts to tune the servo driver in the field may result
in damage to the servo, galvanometer, or mirror. The manufacturer will not cover
damage as a result of unauthorized attempts to tune the servo drive. The customer
may be assessed an additional fee if the servo driver and galvanometer have to be
factory tuned as a result of unauthorized tuning in the field.
Tuning the servo drive refers to adjusting the terms in the servo loop to optimize
performance for a given set of parameters. The parameters are:
Galvanometer Model (rotor inertia, coil resistance, inductance, position detector
sensitivity, etc.)
Mirror Inertia
Maximum Rotor Angular Displacement
Command Waveform (Step, Vector, Raster, Sinusoid)
Performance (Speed, Accuracy)
Supply Voltage (+/- 15 to +/- 24 volts)
Once the parameters are determined, a technician trained in the skill of servo tuning can
set up a servo driver board with a given galvanometer/mirror combination and a set of
operating parameters.
10.1 Servo Tuning Potentiometers (Personality Board)
Reference the Jumpers and Potentiometer drawing in Section 6.2.
10.1.1 Position Proportional (R22)
Position Proportional
(R22)
is a pot used to adjust the gain of the position proportional
term.
10.1.2 Integrator (R47)
Integrator
(R47)
is the pot used to adjust the gain of the servo loop at DC. This is useful
for the scanner to achieve its commanded location at steady state.