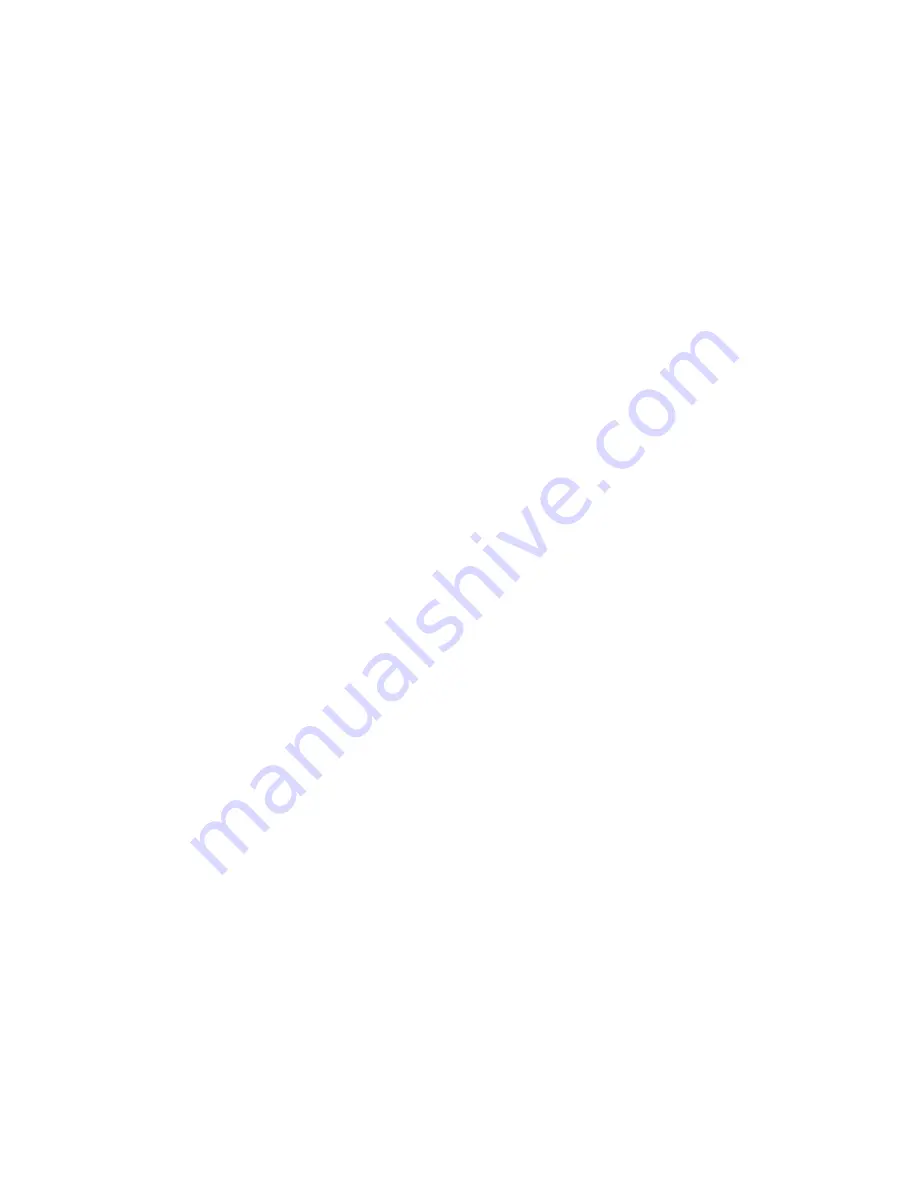
22 QuantumDrive-4000 Manual
91-0027 Rev. E
Copyright © Nutfield Technology, Inc.
6/2010
9.
Heat Sink Requirements
WARNING: The servo driver board MUST be attached to an additional heat sink
before applying power. Failure to provide proper heat sinking could result in
damaged components and could void the manufacturer’s warranty.
Each servo drive board has two output amplifiers and two voltage regulators, which
require heat sinking. These devices are mounted to an “L”-shape heat sink attached to
the board. This heat sink is not sufficient for normal operation. The servo drive heat
sink must be attached with at least two screws to a larger thermally conductive surface
such as an aluminum plate. Make sure that the surface is flat and that the two plates are
in good contact with each other. NTI recommends selecting a heat sink surface with
exposure to the outside surface of the host system. The use of thermal paste is a good
idea for demanding applications.
The amount of heat that needs to be dissipated depends on several factors including the
size of the galvanometer and mirror, the galvanometer stator resistance, the command
waveform and duty cycle, and the ambient temperature.
As a guideline, one Quantum Scan 7 galvanometer and servo drive with 10mm mirrors
running an aggressive vector pattern, requires about 325 square centimeters of surface
area. This can be achieved with heat sink fins if surface area is limited. Blowing air
across the heat sink will also reduce the surface area requirements. In this example, the
galvanometer and servo driver consume about 30 watts of power, most of which is
dissipated in the servo drive.
It is suggested that the temperature of the servo driver heat sink near the output
amplifiers not exceed 55 degrees Celsius. Some trial and error may be required in each
application to reach the appropriate amount of heat sinking.