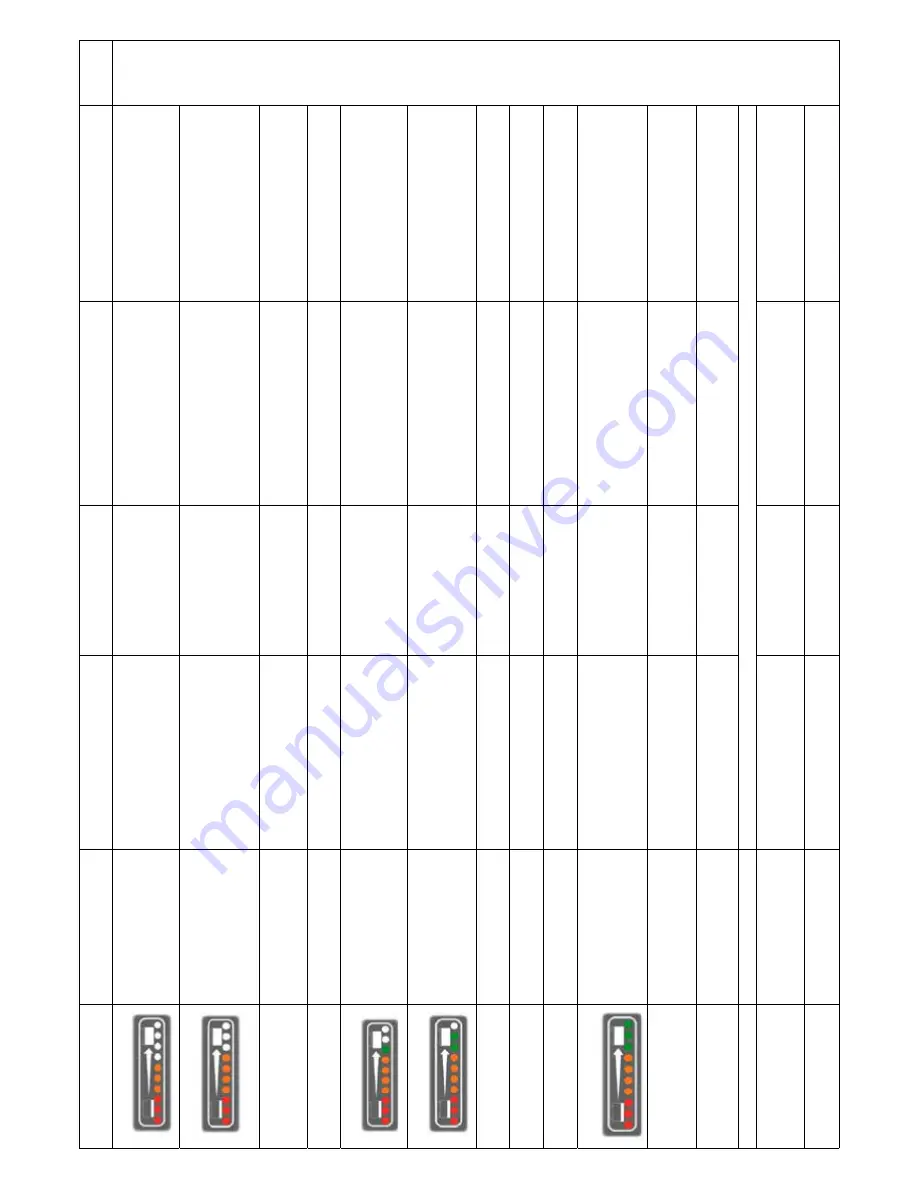
25
Number of bars flashing on display
Fault
Possible Cause
Ef
fect on Product
Investigate the Following
Action Required
If Fault
Persists.
* 6 Bars flash continuously
.
* Control system is Inhibiting drive.
* Faulty controller
.
* Machine will not operate.
* Check controller for water damage.
* Replace controller
.
*7 Bars flash once with pause
* Accelerator pedal trip.
* Accelerator pedal being activated without
seat switch being activated (nobody on seat)
Or seat switch momentarily deactivated while
accelerator pedal being activated during forward
/ reverse operation.
* Machine will not drive.
* Ensure accelerator pedal is not activated without
seat switch being activated. Ensure firm contact
with seat by operator at all times while accelerator
is pressed.
* Operator to be trained.
* 7 Bars flash twice with pause.
“ Emergency stop has been activated.
* Of
f aisle cleaning activated with floor
tool raised.
* Inadvertent pressing of emergency stop or
activation of of
f-aisle cleaning mode.
* Machine will not drive.
* Ensure emergency Stop button has not been
activated and of
f aisle vac switch is in of
f position
with floor tool raised.
* Reset emergency stop button. Switch of
f aisle
vac and raise floor tool.
* Cycle key switch to resume normal operation.
* 7 Bars flash 3 times with pause.
* V
ac Motor system short circuit.
* V
ac motor wiring fault / motor fault.
* V
ac motor will not operate.
* Check vacuum motor and wiring
* Replace motor and any damaged wiring.
* Cycle key switch to resume normal operation.
* 8 Bars flash continuously
.
* Control system trip.
* Seat switch failure.
* Machine does not operate.
* Check seat switch wiring.
* Replace wiring as required.
* 9 Bars flash once with pause.
* Flashing beacon failure to operate.
* Beacon short circuit.
* Flashing beacon does not operate
in accordance with safety require
-
ments.
* Check wiring and connections to device.
* Replace damaged components.
* Cycle Key switch to resume normal operation.
* 9 Bars flash 3 times with pause.
* W
ater pump failure to operate.
* Failure of pump or wiring short circuit.
* No water supplied to cleaning
heads.
* Check wiring and connections to pump.
* Replace damaged components.
* Cycle Key switch to resume normal operation.
* 9 Bars flash 4 times with pause.
* Detergent pump failure to operate.
* Failure of pump or wiring short circuit.
* No detergent supplied in water mix
to cleaning head.
* Check wiring and connections to pump.
* Replace damaged components.
* Cycle Key switch to resume normal operation.
* 9 Bars flash 5 times with pause.
* Solenoid brake circuit failure.
* Failure of solenoid or wiring.
* Machine will not move.
* Check wiring and connections to brake.
* Replace damaged components.
* Cycle Key switch to resume normal operation.
* 10 bars flash continuously
* Supply voltage to controller has
exceeded 40 volts.
* Battery and motor connections may have
become loose.
* Possible long term damage to
controller if fault persists.
* Check battery wiring, trio drive and motor
connections.
* Replace damaged components.
* Cycle Key switch to resume normal operation.
* Bars cycle up and down
continuously (from 1 to 10 and 10
back to 1) and repeats.
* Accelerator pedal movement
detected during V
ario start up se
-
quence (partially pressed or jammed).
* Foot or object on pedal during switch on or
possible jamming of pedal.
* Machine will not operate.
* Remove object and ensure pedal is not jammed
or depressed during switch on of V
ario.
* Cycle Key switch to resume normal
operation .
* Bars cycle from 1 to 10
continuously and repeats.
* Machine inhibit.
* Controller/harness incorrectly wired.
* Machine will not operate.
* Check controller and harness wiring with special
attention to wires p2/03 and p2/10.
* Correct wiring.
* Cycle Key switch to resume normal operation
* No indication on display
.
* Horn and beacon failure.
* Replace 20
Amp fuse (If this doesn’t fix fault replace horn or beacon)
* No indication on display
.
* Brush motors continuously either of
f
or on while in transport mode.
* Microswitch failure.
* Brushes will not operate correctly
.
* Check wiring and microswitch on underside of
machine by brushes ensuring microswitch is clear
of debris.
* Replace/clean damaged components.
* No indication on display
.
* V
AC motor continuously either of
f
or on.
* Microswitch failure.
* V
acuum will not operate correctly
.
* Check wiring and microswitchs behind floor tool
handle.
* Replace/clean damaged components.
Contact Service Agent.
Содержание TTV 678
Страница 28: ...28 Notes TTV 678 Schematic Diagram...
Страница 29: ...29 Notes...
Страница 31: ...31...