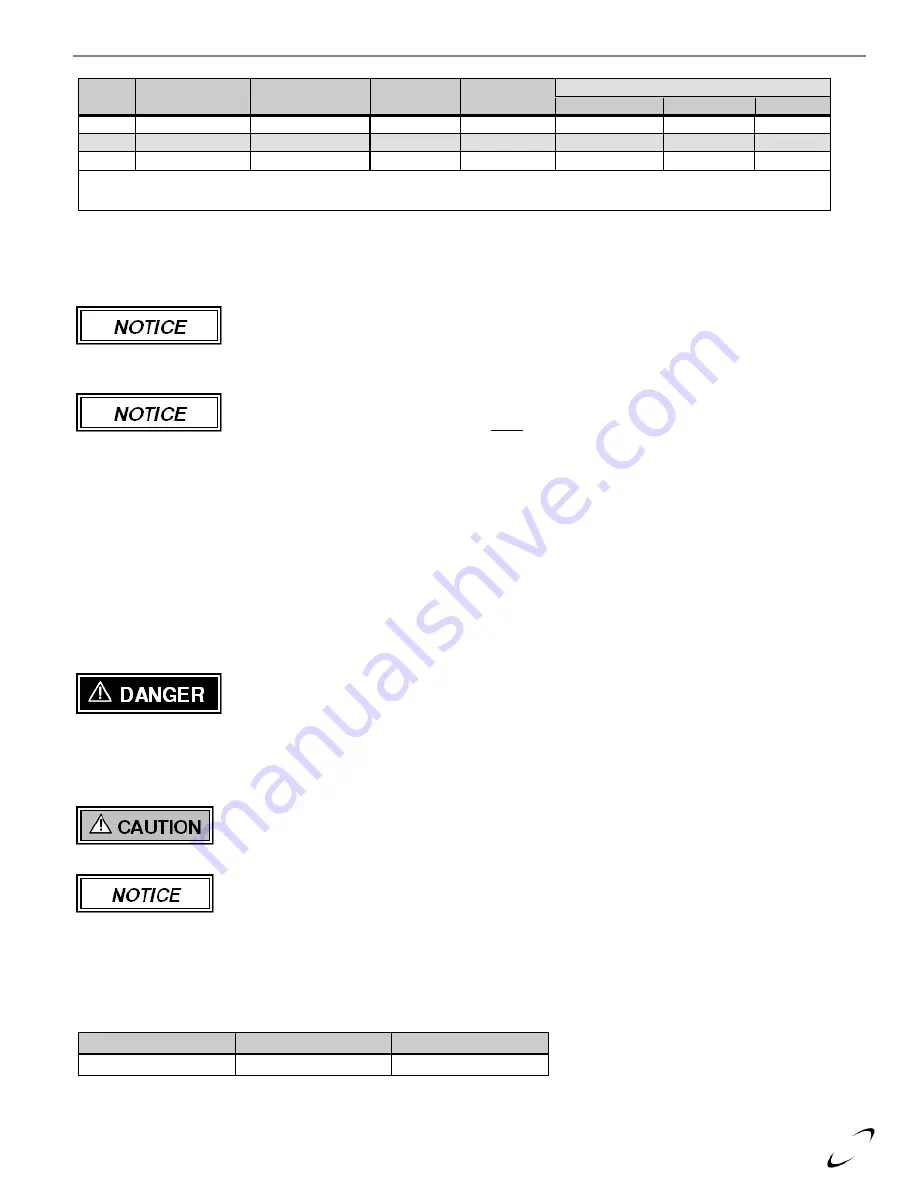
Ti Series Installation and Operation Instructions
│
Trinity
29
Table 9-3 Minimum Circulator and Pipe Sizes
Model
Restriction
Head Loss
Minimum
Pipe Size
Min. Flow
(GPM)
Max. Temp.
Rise
Minimum Primary Loop Pump Size
B&G
Grundfos
Taco
100
1
7' at 6 GPM
1
"
4.5
45
F
NRF-22
UP 15-58
008
150
8' at 7 GPM
1
"
6
45
F
PL-30
UP 26-99
0011
200
7' at 10 GPM
1-1/4
"
8
45
F
PL-36
UP 26-99
0011
Notes:
1 – Must use pump model specified for Ti150 when using a safety flow switch.
Air Removal
– The boiler and system plumbing layout must be configured to promote the removal of air from the water. Air
vents and bleeders must be strategically placed throughout the system to aid in purging the air from the system during
commissioning of the boiler. The system must also employ the use of a strategically located air removal device, such as an air
scoop or micro-bubbler, designed to remove the air from the water as it flows through the system.
Follow the installation instructions included with the air removal device when placing it in the system;
air removal devices generally work better when placed higher in the system. Always locate air
removal devices in areas of the system that have a guaranteed positive pressure, e.g., in close proximity to the water fill and
expansion tank.
Trinity boilers are equipped with an automatic air removal device to aid in the purging of air from the
boiler during the initial fill. This device is
NOT
intended, nor is it sufficient to remove the air from the
system plumbing, even if the air makes it back to the boiler. A strategically located air removal device must be installed in the
system.
Low Water Cutoff / Flow Switch
– The Trinity Ti boiler is not provided with a LWCO or Flow Switch, however one is to be
field installed in any application where the boiler is located above the radiation or where local authorities require it. NTI
recommends installing a LWCO or flow switch to prevent the boiler from firing without water in the heat exchanger. When
used, Low Water Cut Off and Flow Switch devices must be installed in accordance with the manufacturer’s instructions and the
following:
LWCO must be at least 6” above the top of the boiler.
Flow Switch must be installed in a 1” diameter line directly in series with the boiler at all times. NTI recommends a
“McDonnell & Miller” model number “FS8-W”.
The normally open contacts of either a LWCO or Flow Switch must be wired in series with the boiler’s 24V limit
circuit, see wiring schematic for more details.
Operating the boiler without sufficient water level will result in overheating and may result in property
damage, fire, personal injury or loss of life.
Expansion Tank
– The expansion tank must be sized in accordance with the water volume of the system as well as the firing rate
of the appliance. It is important to locate the expansion tank, and make-up water fill, on the inlet side of any circulator in the
system, as doing so will guarantee the lowest pressure in the system will be at least equal to the tank and make-up water pressure.
See examples in Figures 9-2 and 9-3.
Ensure the expansion tank cannot become isolated from the boiler anytime the system is operating.
Failure to follow these instructions may result in discharge of the Pressure Relief Valve may result in
property damage or personal injury.
The installation of flow checks, motorized valves or other shutoff devices (other than for the purpose of
servicing) are not permitted between the location of the “Closely Spaced Tees” and the expansion tank;
see Figures 9-2 and 9-3.
Indirect Fired Water Heater
– The indirect fired water heater is in series with the boiler during a demand for DHW. Therefore
it is important to use an Indirect Fired Water Heater that has minimal head loss. Indirect fired water heater head loss must not
exceed those specified in Table 9-4. See Table 9-3 for minimum circulator specifications.
Table 9-4
Maximum Indirect Fired Water Heater Head Loss (Boiler Side) at Minimum Flow
Ti100
Ti150
Ti200
6’ at 5 GPM
10’ at 6 GPM
14’ at 8 GPM