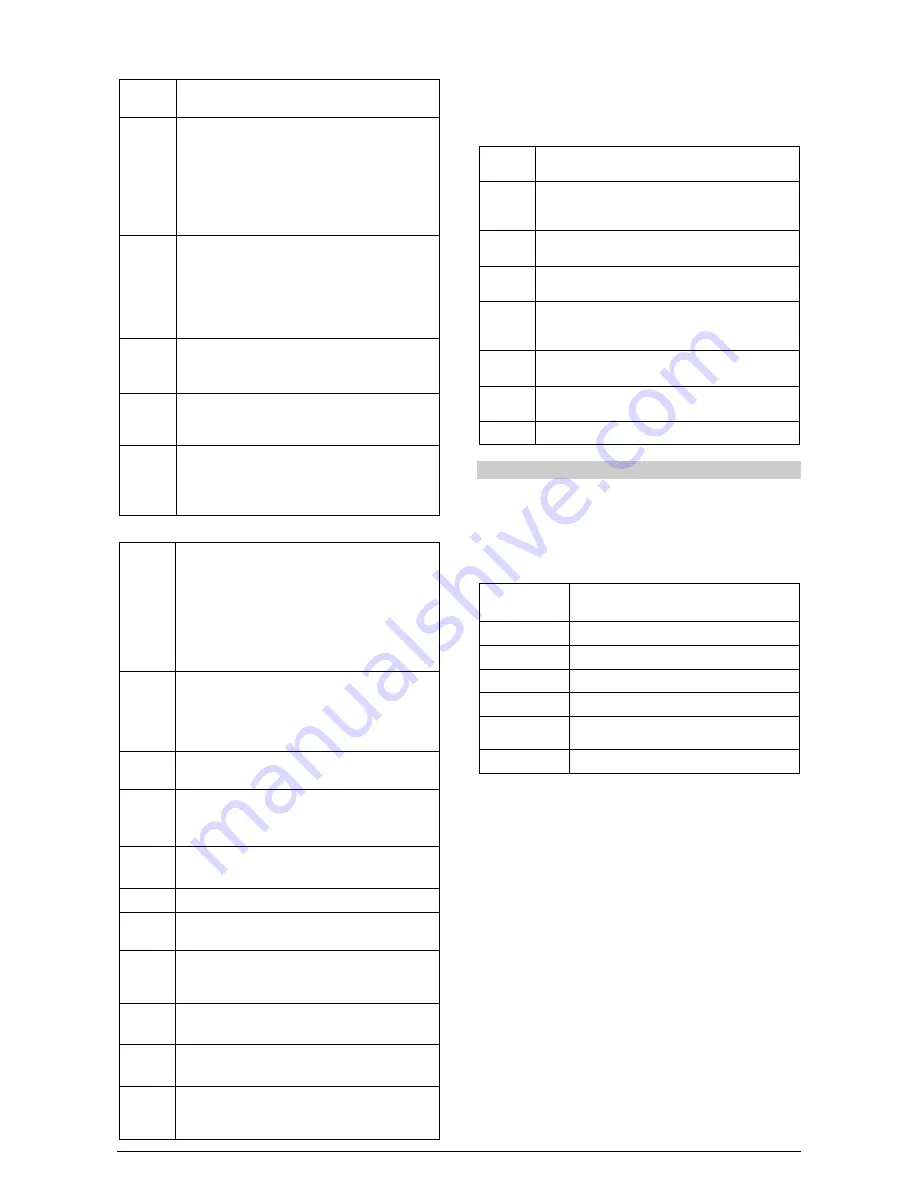
N1040 Controller
NOVUS AUTOMATION
4/7
ALARMS CYCLE
Fva1
Fva2
Functions of Alarms. Defines the functions for the
alarms among the options of the Table 02.
Sp.a1
Sp.a2
Alarm SP. Value that defines the point of activation of
the alarm outputs.
For the alarms programmed with the functions of the
type Differential, these parameters represent the
deviations.
For the
ierr
alarm function, this parameter has no
meaning.
Sp1.e
sp2.e
SP Enable. Configures display of SPA1 and SPA2
also in the Operation Cycle.
YES
SPA1/SPA2 are displayed in the Operation
Cycle
NO
SPA1/SPA2 are not displayed in the
Operation Cycle
bla1
bla2
Blocking Alarms.
YES
- Enables initial blocking;
NO
- Inhibits initial blocking.
xya1
xya2
Alarm Hysteresis. Defines the difference between the
value of PV at which the alarm is triggered and the
value at which it is turned off.
flsh
Allows visual signalization of an alarm occurrence by
flashing the indication of PV in the operation level.
YES
- Enables alarm signaling flashing PV;
NO
- Disables alarm signaling flashing PV.
INPUT CYCLE
Type
Input Type. Selects the input signal type to be
connected to the process variable input. Refer to
Table 01 for the available options.
(J):
Tc
J
-110 to 950 °C / -166 to 1742 °F
(K):
Tc
k
-150 to 1370 °C / -238 to 2498 °F
(T):
Tc
t
-160 to 400 °C / -256 to 752 °F
(Pt100):
Pt
-200 to 850 °C / -328 to 1562 °F
fltr
Digital Input Filter. Used to improve the stability of the
measured signal (PV). Adjustable between 0 and 20.
In 0 (zero) it means filter turned off and 20 means
maximum filter. The higher the filter value, the slower
is the response of the measured value.
Dp.po
Selects the decimal point position to be viewed in both
PV and SP.
vn
i
t
Selects display indication for degrees Celsius or
Fahrenheit:
(
- Indication in Celsius;
f
- Indication in Fahrenheit.
0ffs
Offset value to be added to the PV reading to
compensate sensor error. Default value: Zero.
Spll
SP Low Limit. Defines the SP lower limit of.
Spxl
SP High Limit. Defines the upper limit for adjustment
of SP.
Lbd.t
Loop Break Detection Time. Time interval for the LBD
function. Defines the maximum interval of time for the
PV to react to a control command. In minutes.
1e.ov
Percentage value to be applied to the output on any failure
of the sensor that is connected to the controller input.
bavd
Digital communication Baud Rate selection. In kbps.
1.2, 2.4, 4.8, 9.6, 19.2, 38.4, 57.6 and 115.2.
Addr
Communication Address. Number that identifies the
controller in the serial communication network,
between 1 and 247.
CALIBRATION CYCLE
All types of input are calibrated in the factory. In case a
recalibration is required; it shall be carried out by a specialized
professional. In case this cycle is accidentally accessed, do not
perform alteration in its parameters.
pass
Password
.
This parameter is presented before the
protected cycles. See item Protection of Configuration.
(alib
Calibration
.
Enables the possibility for calibration of
the indicator. When the calibration is not enabled, the
related parameters are hidden.
inL(
Input Low Calibration
.
Enter the value corresponding
to the low scale signal applied to the analog input.
ink(
Input High Calibration
.
Enter the value corresponding
to the full scale signal applied to the analog input.
rstr
Restore
.
Restores the factory calibration for all inputs
and outputs, disregarding modifications carried out by
the user.
(j
Cold Junction
.
This screen is for information purpose
only.
Pas.(
Password Change. Allows defining a new access
password, always different from zero
Prot
Protection. Sets up the Level of Protection. See Table 04.
CONFIGURATION PROTECTION
The controller provides means for protecting the parameters
configurations, not allowing modifications to the parameters values,
avoiding tampering or improper manipulation. The parameter
Protection (
PROt
), in the Calibration level, determines the
protection strategy, limiting the access to particular levels, as shown
by the Table 04.
PROTECTION
LEVEL
PROTECTION CYCLES
1
Only the Calibration cycle is protected.
2
Calibration and Input cycles.
3
Calibration, Input and Alarms cycles.
4
Calibration, Input, Alarms and Tuning cycles.
5
All cycles are protected, but the SP screen in
the operation cycle.
6
All cycles are protected, including SP.
Table 04 – Levels of Protection for the Configuration
ACCESS PASSWORD
The protected levels, when accessed, request the user to provide the
Access Password for granting permission to change the
configuration of the parameters on these levels.
The prompt
PASS
precedes the parameters on the protected levels.
If no password is entered, the parameters of the protected levels can
only be visualized.
The Access Password is defined by the user in the parameter
Password Change
(
PAS.(
), present in the Calibration Level. The
factory default for the password code is 1111.
PROTECTION ACCESS PASSWORD
The protection system built into the controller blocks for 10 minutes
the access to protected parameters after 5 consecutive frustrated
attempts of guessing the correct password.
MASTER PASSWORD
The Master Password is intended for allowing the user to define a
new password in the event of it being forgotten. The Master
Password doesn’t grant access to all parameters, only to the
Password Change
parameter (
PAS(
). After defining the new
password, the protected parameters may be accessed (and
modified) using this new password.