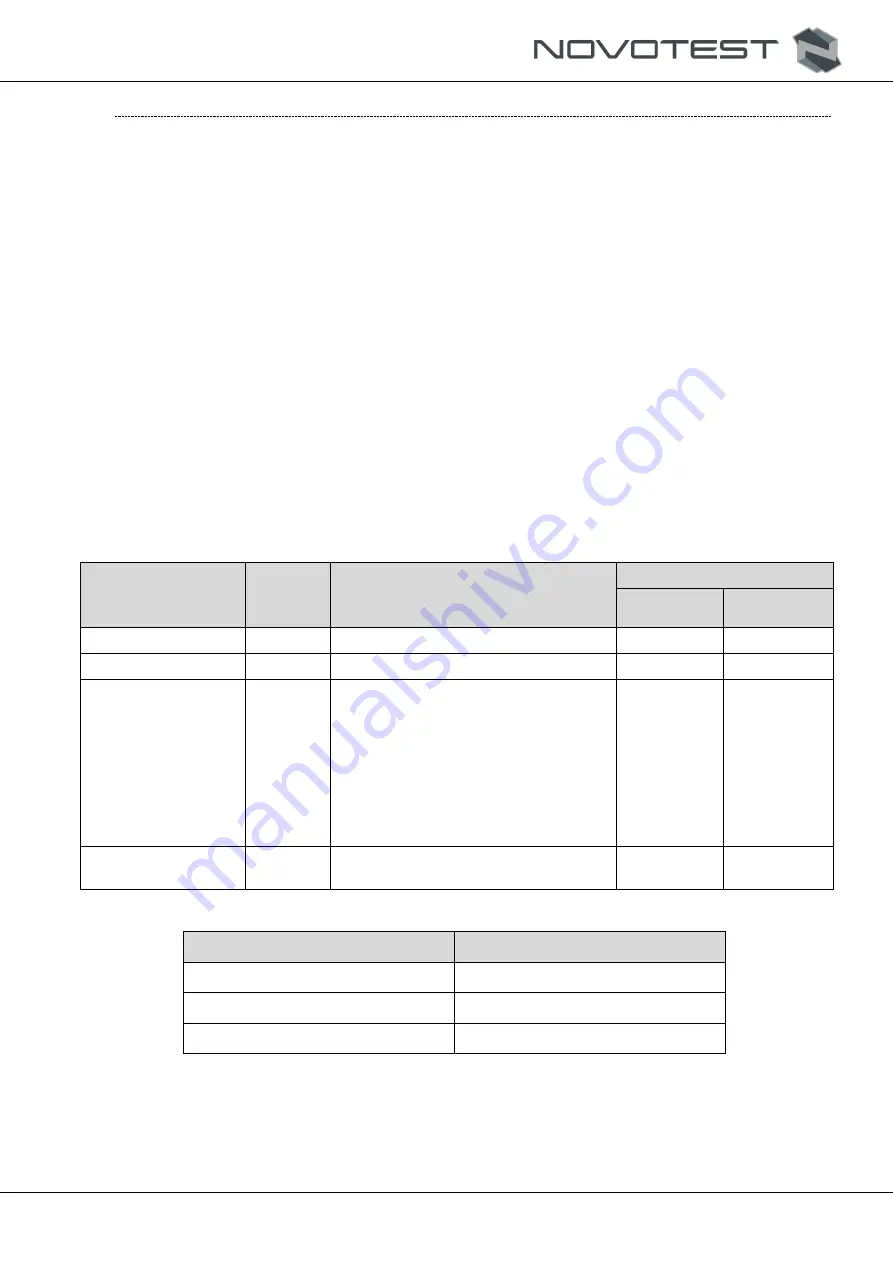
Operating manual
EMA Thickness Gauge NOVOTEST UT-3K-EMA
RDC.ED.UT-3K-EMA.000 OM
Page 9
3.2 Verification
Once the device is commissioned, its primary verification must be done. Periodic verification
should be done during the use of the device and after its repair. It is recommended to verify the device
at least once a year.
The method of verification, hereinafter referred to as verification, applies to EMA Thickness
Gauge NOVOTEST UT-3K-EMA and prescribes the methods and means of primary and periodic
checking.
The device verification must be done by State Metrology Service or other authorized bodies and
organizations having the right of verification.
3.2.1 Preconditions for verification
The following requirements must be fuilfilled at the verification:
– ambient air temperature: from +5
о
С to +30
о
С;
– relative air humidity: max 80% at the tempe25
С;
– air pressure: from 86 kPa to 106 kPa.
3.2.2 Steps of the verification and accessories
When performing the verification, take the following steps and use accessories specified in Tab.
3.1.
Table 3.1 – Steps of the verification and accessories
Verification steps
Clause
Verification accessories
Necessity after
commissioning
and repair
operation and
storage
1. Visual inspection
3.2.3
Yes
Yes
2. Verification
3.2.4
Yes
Yes
3. Determination of
the measurement error
3.2.5
Set of ultrasonic thickness reference
blocks KUSOT-180 or the set of
thickness reference blocks KMT-
176M-1 (KMTC-97);
set of plane-parallel blocks (tab. 3.2).
Yes
Yes
4. Execution of
verification
3.2.6
Yes
Yes
Table 3.2 – Parameters of plane-parallel reference blocks made of the same steel sample.
Thickness, mm
Roughness R
Z,
mcm, less
2 ± 0,01
10
10 ± 0,015
20
60 ± 0,03
20
3.2.3 Visual inspection
The device must be equipped according to c. 1.3 of Operating manual of EMA Thickness Gauge
NOVOTEST UT-3K-EMA.