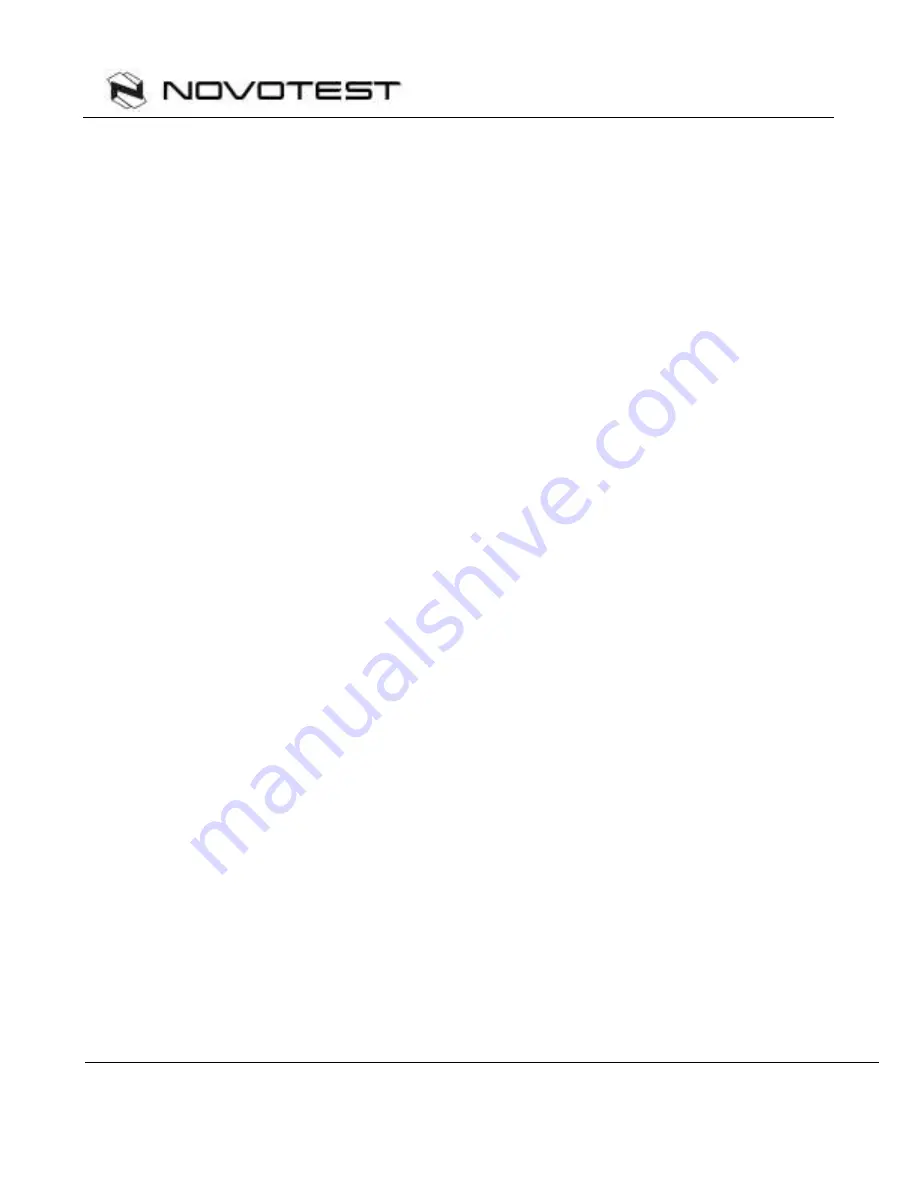
Development and manufacturing of non-
destructive testing units and system
Ultrasonic Flaw Detector NOVOTEST UD2301
2
1. List of Abbreviations used
The manual has the following abbreviations and symbols:
AFS
– automatic signaling of defects;
TVG
– time varied gain;
NDT
– nondestructive testing;
CB
– calibration block;
US
– ultrasonic.
2. Introduction
2.1. Appointment of flaw detector
Flaw detector is designed for testing of products for the presence of
defects such as discontinuity and homogeneity of materials, semi-
finished products and welds for measuring depth and coordinates of
defects, measure the thickness and sound velocity in the material.
Flaw detector implements shadow, echo and mirror-shadow testing
methods. Flaw detector allows user to create, record and stored in
nonvolatile memory temporary implementation of pulsed ultrasonic
signals to subsequent transmitting to the PC for analysis and
presentation in the form of a document. Integrated liquid crystal
display (LCD) provides a mapping of ultrasonic signals in the form of
A-scan, as well as images of cross sections of testing objects in the
form of B-scans.
Flaw detector can be used in mechanical engineering, aerospace,
metallurgy, mounting hardware, power equipment, as well as for the
testing of transportation facilities.
2.2. Testing
For proper ultrasonic testing user must have testing methods for
similar products and special requirements for ultrasonic testing.
These requirements include: the definition of the task of testing,
selection of suitable control techniques (testing schemes), the