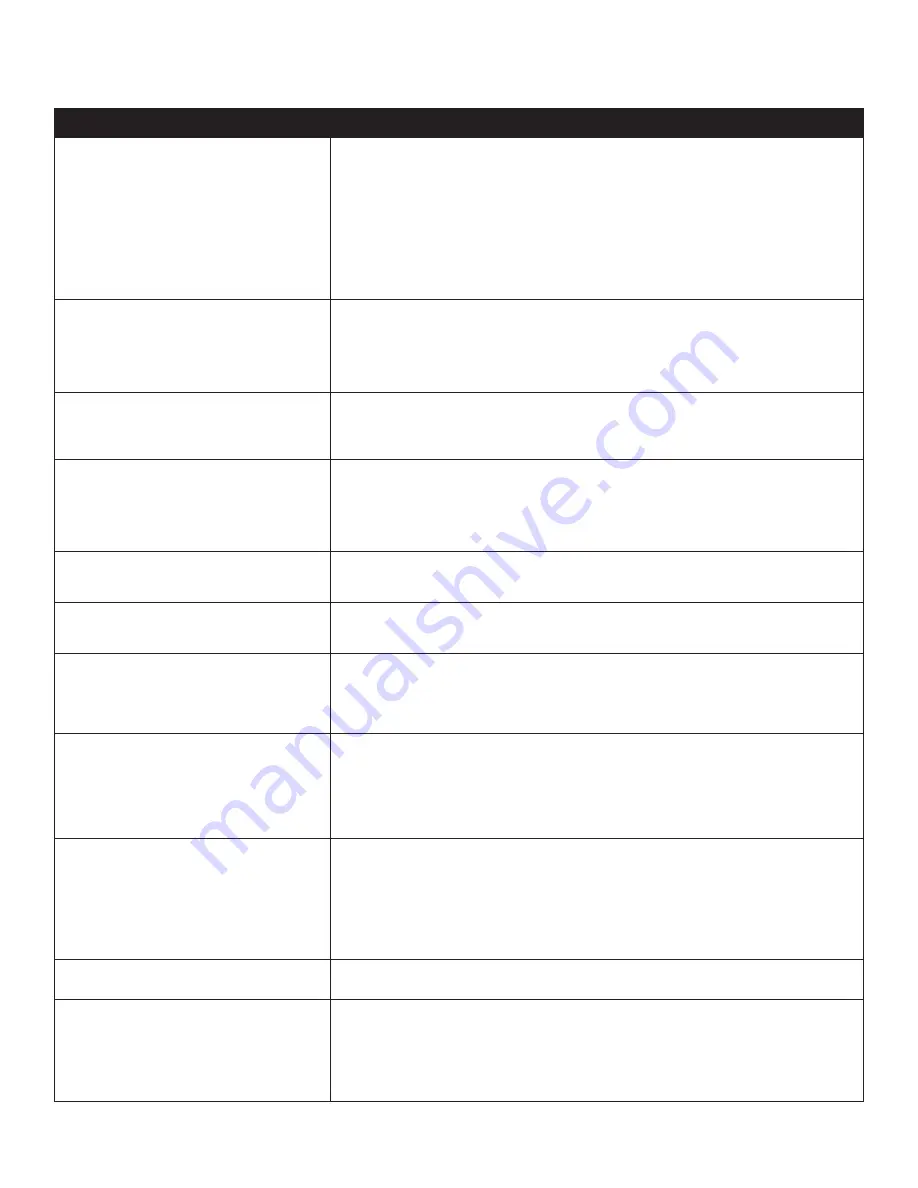
26
Problem
Possible Solutions
1. CONDITIONER DELIVERS UNTREATED WATER
A. Bypass valve is open
B. No salt in brine tank
C. Injector or screen plugged
D. Insufficient water flowing into brine tank
E. Hot water tank hardness
F. Leak at distributor tube
G. Internal valve leak
H. Flow meter jammed
I. Flow meter cable disconnected or not plugged into meter cap
J. Improper programming
A. Close bypass valve
B. Add salt to brine tank and maintain salt level above water level
C. Replace injectors and screen
D. Check brine tank fill time and clean brine line flow tank control if plugged
E. Make sure distributor tube is not cracked. Check O ring and tube pilot
F. Make sure distributor tube is not cracked. Check O ring and tube pilot
G. Replace seals and spacers and/or piston
H. Remove obstruction from flow meter
I. Check meter cable connection to timer and meter cap
J. Reprogram the control to the proper regeneration type, inlet water hardness, capacity or flow meter size.
2. CONDITIONER FAILS TO REGENERATE
A. Electrical service to unit has been interrupted
B. Timer is not operating properly
C. Defective valve drive motor
D. Improper programming
E. Meter not metering
A. Assure permanent electrical service (check fuse, plug, chain or switch)
B. Replace timer
C. Replace drive motor
D. Check programming and reset as needed
E. Verify by opening faucet and checking current flow - if no flow replace bypass/meter assembly
3. UNIT USES TOO MUCH SALT
A. Improper salt setting
B. Excessive water in brine tank
C. Improper programming
A. Check salt usage and salt setting
B. See #7
C. Check programming and reset as needed
4. LOSS OF WATER PRESSURE
A. Iron build-up in line to water conditioner
B. Iron build-up in water conditioner
C. Inlet of control plugged due to foreign material broken loose from pipes
by recent work done on plumbing system.
D. Parallel connectors plugged
A. Clean line to water conditioner
B. Clean control and add resin cleaner to resin bed. Increase frequency of regeneration
C. Remove piston and clean control
D. Inspect parallel connections and clean as required
5. LOSS OF RESIN THROUGH DRAIN LINE
A. Air in water system
B. Drain line flow control is too large
A. Assure that well system has proper air eliminator control. Check for dry well condition.
B. Ensure drain line flow control is sized
6. IRON IN CONDITIONED WATER
A. Fouled resin bed
B. Iron content exceeds recommended parameters
A. Check backwash, brine draw and brine tank fill. Increase frequency of regeneration. Increase backwash time.
B. Add iron removal conditioner system
7. EXCESSIVE WATER IN BRINE TANK
A. Plugged drain line flow control
B. Brine valve failure
C. Improper programming
D. Not drawing brine
A. Clean flow control
B. Replace brine valve
C. Check programming and reset as needed
D. See #8 - A
8. SALT WATER IN SERVICE LINE
A. Plugged injector system
B. Timer not operating properly
C. Foreign material in brine valve
D. Foreign material in brine line flow control
E. Low water pressure
F. Improper programming
A. Clean injector and replace screen
B. Replace timer
C. Clean or replace brine valve
D. Clean brine line flow control
E. Raise water pressure
F. Check programming and reset as needed
9. CONDITIONER FAILS TO DRAW BRINE
A. Drain line flow control is plugged
B. Injector is plugged
C. Injector screen is plugged
D. Line pressure is too low
E. Internal control leak
F. Improper programming
G. Timer not operating properly
A. Clean drain line flow control
B. Clean or replace injectors
C. Replace screen
D. Increase line pressure (line pressure must be at least 20 psi at all times)
E. Change seals and spacers and/or piston assembly
F. Check programming and reset as needed
G. Replace timer
10. CONTROL CYCLES CONTINUOUSLY
A.Faulty hall sensor on circuit
A. Replace circuit board
11. DRAIN FLOWS CONTINUOUSLY
A. Foreign material in control
B. Internal control leak
C. Control valve jammed in brine or backwash position
D. Timer motor stopped or jammed teeth
E. Timer not operating properly
A. Remove piston assembly and inspect bore. Remove foreign material and check control in various regeneration positions
B. Replace seals and/or piston assembly
C. Replace piston and seals and spacers
D. Replace timer motor and check all gears for missing teeth
E. Replace timer
TROUBLE SHOOTING
Содержание EcoSmart ECS Series
Страница 2: ......