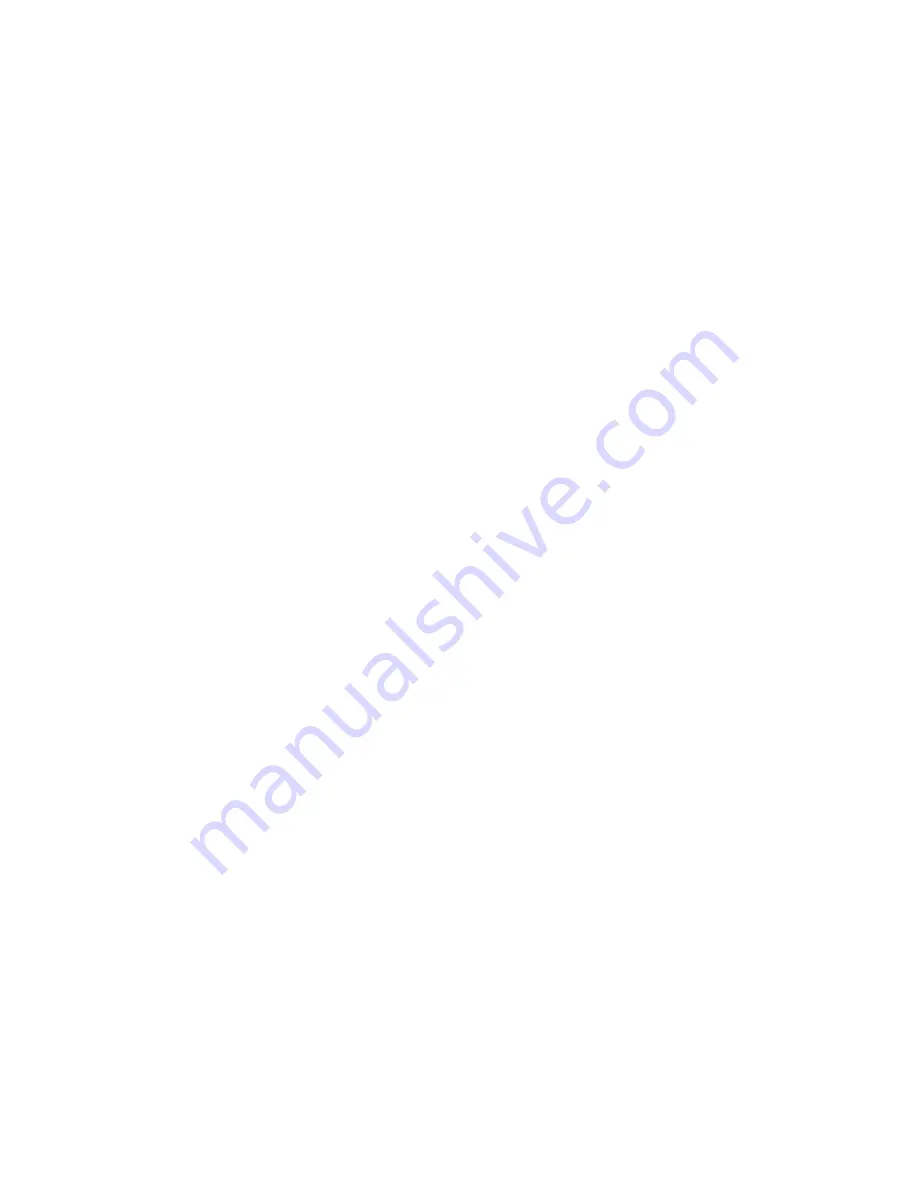
(With a ‘71 or later machine on its centre stand you could take out the front bolt on the machine itself as
there is practically no weight on it so long as the head steady has not been removed). Screw this into the
end of the spindle.
The first modification on Mk 11A 850s whilst it retained the stupid }in locating screw for the spindle, has
less bearing area because bushes and spindle are shorter and neither has it the 1 / 16in oil feed holes.
Still worse, hardly any oil was put in at the works, the feed wicks are very tight in the spindle bore so that
any oil; which might be in the centre of the spindle is unlikely to reach the disc wicks which are under the
core plugs and which are intended to feed oil to the outer edge of each bush.
The second modification on Mk III at long last secures the spindle in the engine plate cross tube with two
cotter pins--bicycle crank type-but the other faults, tight wicks and no oil remain.
An improvement is to drill the centre of the offside core plug 13/64in, tapping size far 1/4in BSF (26T) or
1/4in UNF (28T). Use a pilot drill, say 1/8in, first so that the Rapping drill does not drill oversize; tap the
hole. By screwing an a }in set screw against a suitable washer and spacer you can pull the core plug out,
take out the disc wick and run a drill, the 13/64in will do, down the middle of the feed wick and put a
similar hole in the centre of the disc wick. With a Wesco or similar pressure oil can you can now inject oil
through the right hand wick into the spindle centre where it will pass along to the nearside wicks. Replace
the disc wick and refit the core plug--it will tighten in if you fit it as before, nut convex side out, and expand
it with a hammer and suitable soft drift. Complete the job by fitting a short 1/4in cheese head set screw
and fiber washer. Then periodical oiling with a Wesco is all that is necessary. 1 know NVT say SAE140 or
EP90 but I use engine oil if nothing else available -any is better than none at all!!
Finally, referring once again to the original set-up which has the grease nipple. Having dismantled the
parts and got rid of all grease, a small Tecalemit grease gun will operate with oil but must have the
grease cleared out first. Mine works well and I used it at Andover and still do at Parkroad. Care must be
taken however as these will build up a high enough pressure to blow the end cap off also.
Failing this get a friend to hold the machine as far over to the left as possible--footrest rubber on ground-
but not weight of machine on it!!! Remove the grease nipple and -inject oil with Wesco can.> >
REAR SUSPENSION UNITS don't usually give much trouble, but many owners prefer 150Ib (sidecar)
spring in place of the 1261h springs fitted standard. This helps the handling in a strange way-and it also
helps the dampers if you fit the Girling covers over the units at the same time. More than doubles the life
of the units, or fit rubber gaiters.
The early black curved chainguard was better for the chain and in styling -it was fitted on pre-1971
Fastbacks-but if you can't find one, the later 850s had a plastic effort which slotted onto the end of the
alleged chainguard to stop the oil from spraying all up your hack and all over your luggage.
As a word of warning, there are two ways of breaking a Commando frame (well three, if you count
the pave at MIRA).
1. Have the rear isolastic mounting too tight-this will break the frame where the tubes from the
seat knobs downwards meet the gussets for the battery carrier.
2. Put a carrier on the back without supports to the pillion footrests. )f this doesn't break the rear
loop it will bend it downwards, and then it will break when your try and straighten it. Watch out for
carriers which foul the top of the damper unit-this can break off the damper eye with interesting
consequences.
26