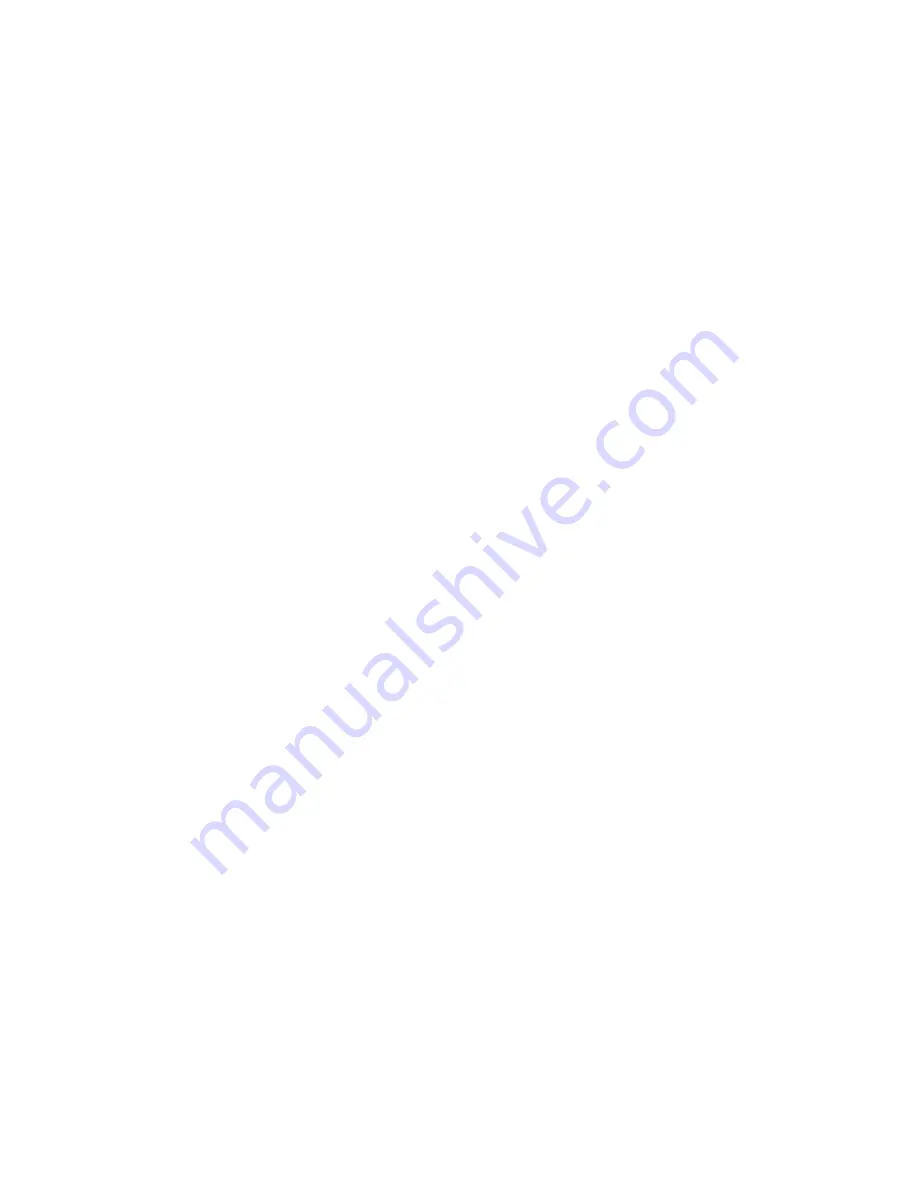
3. The rotor can seize in the stator and twist the end of the crankshaft. Then the tapers have got to be
good. The woodruff key gets cut in half, if you are lucky.
4. The whole lot can seize and go round with the motor, taking the studs out of the back of the primary
chain case. (So if you see your wiring harness all disappearing down the hale at the back of the chain cue
accompanied by a crunching noise you'll know what has happened--the wires are wrapped round the
crankshaft like a bobbin!)
Now the good news---they are not all like that! About 1974 Uncle Joseph, patron saint of the British bike
owner, started to weld the magnets to the centers-and they are identified by a little W about }in high
stamped on the centre. I have never seen one of these exploded.
In the meantime-keep an eye on your rotors, remember Lucas stuff is guaranteed for a year-by Lucas, not
Norton, and don't buy any rotor not stamped with a W, Pt. No. 54202275.
I've never seen the W but the welded rotor is also numbered 54201143 and is also recognized by the
centre sleeve, half steel hall alloy, an welded one. all steel on normal rotor.
THE CLUTCH: An ordinary coil spring, as used on most other clutches, gets progressively harder to
squash as it is compressed from the free position. The clutch needs a certain spring force to prevent it
from slipping, and with this conventional spring action the force to lift the clutch gets greater and greater
as the plates are separated and the springs compressed. This means the muscles in your left hand have
more and more to do as the clutch plates are separated. With a big bike, i.e. lots of torque, so strong
springs, this can be hard work.
A diaphragm spring doesn't rely on the torsion of a coil of wire, but as it is compressed the metal in the
centre of the spring is compressed and the outer edge is stretched. The load to compress the clutch goes
up as the "flat" position is approached, and as the plate goes through the flat position the load drops
again for a bit and then rises again as the spring begins to become conical the other way. If the
dimensions are chosen to use the force as it starts to fall to hold the clutch together and prevent slip the
force needed to lift the clutch actually gets less as the plates are separated-so-you don't need such a
strong left arm. See diag. 2, which (I hope) shows how the force at full lift is greater than the damping
force for a coil spring, but less than the clamping force for a diaphragm spring, as the plates are
separated from the clamped to the free position.
How the diaphragm spring actually produces this miraculous effect is difficult to explain-but it's the same
effect as when you take a steel tape measure-the sort made of curved thin steel strip-and bend it back on
itself -it becomes stiff, and then, with a click, goes easy. You can get the same effect by putting a
Commando spring on the floor and treading on the middle. Support the spring in a clutch drum so there's
room for it to go well over centre. If you are about 15 stone you will feel the clutch suddenly go over
centre with a sort of click as you put your weight on it-unfortunately if you are only 8 stone you will have to
find a friend of the same dimensions so you can do it together. Or obtain a pair of lead wellies. Here
endeth the lesson.
The clutch itself has had one or two interesting modifications over the years. To start with the friction
plates were steel with postage stamps of cork compound stuck on both sides. The life and reliability of
these plates was good (nor so, in some cares, when the postage stamps all fall off and stick together in
one place : the results are interesting clutch slips and drags and will not clear) but eventually the edges of
the plates would dig into the splines on the centre. This made the clutch hard to free-off as the plates got
stuck in their notches, Then the solid cardboard-I mean friction material-plates mere introduced and the
notching problem disappeared, but another problem
19