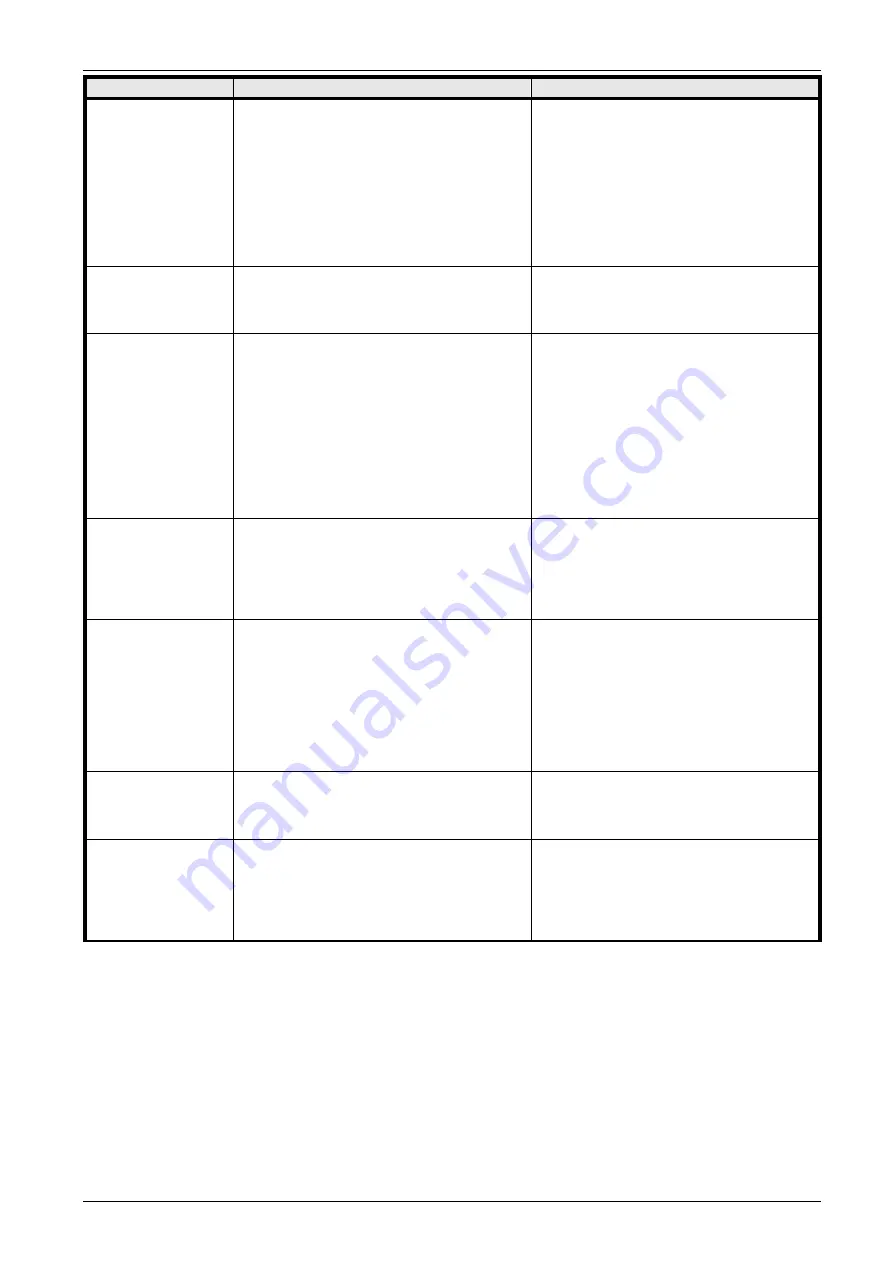
TROUBLESHOOTING
May 06, 2020
Page 16
User Manual No: OM-101A EN
Description
Possible Cause
Corrective Action
3.
Welding wire feeding
problems
A
Contact tip is worn.
B
Liner is worn / dirty.
C
Consumables used are not suitable for the welding
wire diameter or material.
D
MIG/MAG equipment not set-up properly.
E
Welding wire is contaminated.
A
Replace contact tip.
B
Check the Liner; blow it out with clean, dry com-
pressed air. If needed replace it.
C
Use recommended consumables for the welding
wire diameter/material used.
D
Check the feed rolls, feed roll pressure and the
spool brake are adjusted as stated by the
MIG/MAG equipment
’s manual.
E
Use a cleaning felt to clean welding wire in the
MIG/MAG equipment.
4.
Wire feed stops during
welding
A
Wire blockage in contact tip.
B
Wire burns back into contact tip
C
Groove worn in contact tip by welding wire.
A
Check for contamination/clogging, clean or re-
place contact tip.
B
Adjust distance between contact tip and arc.
C
Replace contact tip.
5.
Porosity in the weld
metal
A
Turbulent shielding gas flowing to weld zone
caused by spatter build up inside nozzle or on gas
diffuser.
B
Too low or extremely high shielding gas flow in the
Torch.
C
Shielding gas supply contaminated or incorrect
shielding gas used.
D
Moisture or contamination on the welding wire or
on the work piece
A
Clean the Torch consumables and use nozzle /
gas diffuser anti-spatter spray.
B
Check flow using a gas flow meter then adjust
gas flow rate from 10 LPM (indoors, no drafts)
up to 20 LPM (welding in drafts or outdoors).
C
Check for gas leakages using soapy water or
check for correct shielding gas to the Welding
System.
D
Check the wire and the work piece, use less or
different anti-spatter spray.
6.
Welding arc:
- always varies length
- is unstable
- is erratic
A
Contact tip is worn.
B
Wrong welding parameters.
C
Poor electrical connections in the welding circuit.
A
Change contact tip.
B
Check the MIG/MAG equipment setup parameters
then change parameters.
C
Check / tighten all electrical connections of the
MIG/MAG equipment, Torch and ground cable to
work piece.
7.
Welding wire burns
back to contact tip
A
Incorrect arc voltage/ wire feed speed weld param-
eters for the welding wire wire/material/Torch posi-
tion.
B
Erratic / unstable welding arc.
C
Incorrect contact tip stick-out length for required
weld.
D
Incorrect welding wire stick-out length for required
weld.
E
Ground cable to work piece fault.
A
Adjust arc voltage and/or wire feed speed param-
eters.
B
Refer to Description No. 6 on page 16.
C
Adjust nozzle / tip relationship.
D
Adjust wire stick-out.
E
Replace ground cables and/or connections.
8.
Short contact tip life
A
Contact tip size.
B
Welding wire eroding contact tip due to feed rolls
scoring wire.
C
Exceeding Torch duty cycle.
A
Replace with correct contact tip size.
B
Change feed rolls.
C
Replace with higher rated Torch.
9.
Extreme spatter
A
Incorrect arc voltage/ wire feed speed weld param-
eters for the welding wire / material / Torch posi-
tion.
B
Inadequate shielding gas coverage.
C
Contaminated wire or work piece.
A
Adjust arc voltage and/or wire feed speed param-
eters.
B
Verify shielding gas coverage or gas mixture.
C
Use a cleaning felt to clean welding wire in the
MIG/MAG equipment and work piece.
Содержание SELEKT BRD
Страница 25: ...SPARE PARTS May 06 2020 Page 25 User Manual No OM 101A EN 9 07 PNA SQBT350 SQTB500 SQTB600 Torch Spares ...
Страница 28: ...SPARE PARTS May 06 2020 Page 28 User Manual No OM 101A EN 9 09 TWE SNT2 SNT4 SNT5 Torch Spares ...
Страница 30: ...SPARE PARTS May 06 2020 Page 30 User Manual No OM 101A EN 9 010 BRD SNQ200 SNQ300 SNQ400 Torch Spares ...
Страница 31: ...NOTES May 06 2020 Page 31 User Manual No OM 101A EN us ...