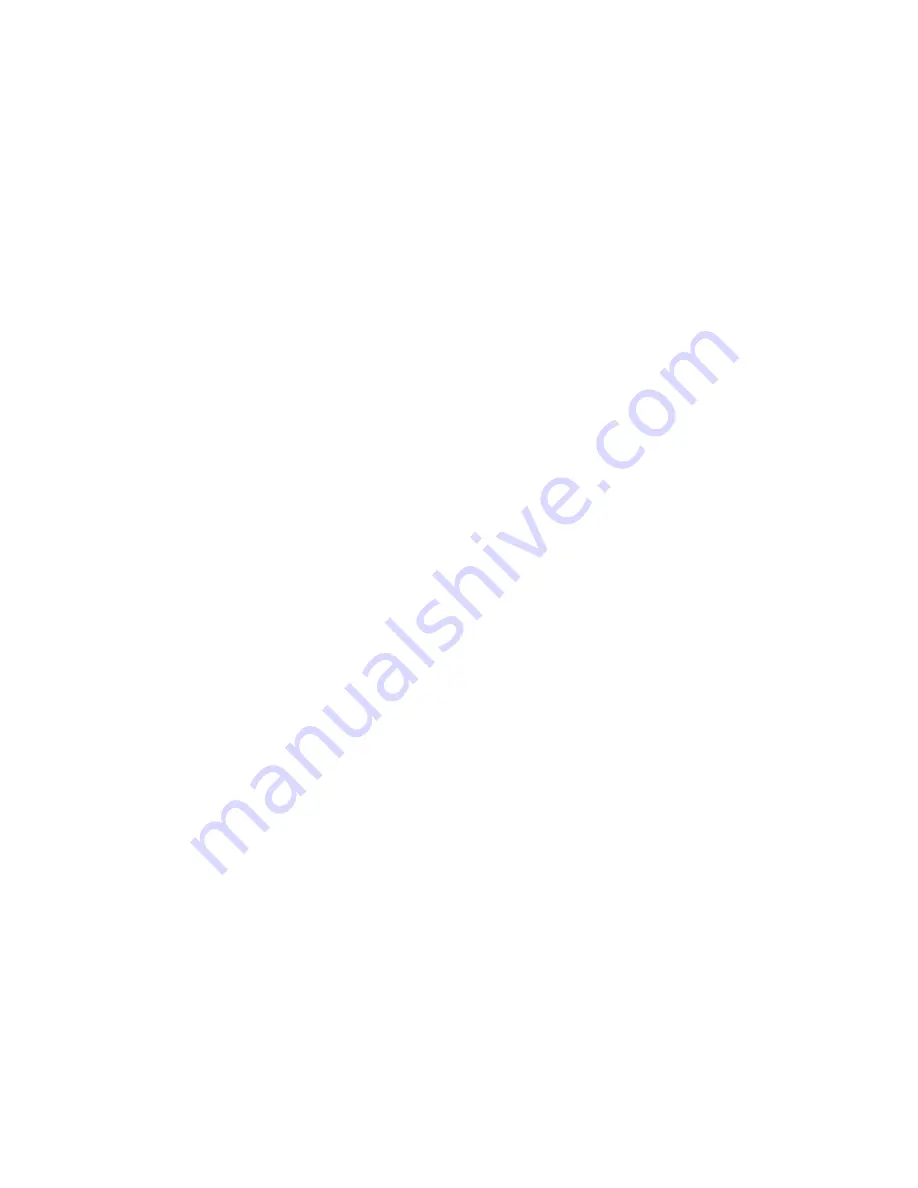
3 – Operating Electric Coil Heaters
3.1 Minimum Airflow
Ensure that sufficient airflow as marked on the nameplate
is passing through the heater. Airflow should be evenly dis-
tributed across the entire face of the heater. Use air turning
vane at duct elbows and splitter damper at duct branch-
offs to streamline the airflow in the heater. Use suitable
airflow sensing device or interlock the heater with fan. An
insufficient airflow will lead to the opening of the auto-reset
thermal cut-out or damage to the heating elements.
3.2 Warning
The air flowing through the duct where the heater is in-
stalled shall not contain any combustible particles, nor any
flammable vapor or gas.
3.3 Air Temperature
The air temperature should not exceed 120°F [49°C] at
the heater outlet.
3.4 Minimum Static Pressure and Air Direction
The heater is protected by a differential pressure switch.
To keep the contact of this switch closed, it is necessary
to maintain a minimum total pressure of 0.07” of water for
a constant flow.
3.5 Manual Reset Thermal Cut-out
This protection device is standard on all heaters of less
than 300V and 30 kW and is optional on all other heat-
ers. Please check the auto-reset thermal cut-out before
resetting the manual thermal cut-out. If any defect has
been detected in the auto-reset thermal cut-out, it will be
necessary to replace it before resetting the manual reset
thermal cut-out.
4 – Maintenance
All electric coil heaters have been designed to operate
long term without problems. Those responsible for equip-
ment and maintenance should be aware of the following
suggestions.
4.1 Visual Inspection
It is strongly recommended to complete a periodic inspec-
tion. This precautionary step will help to keep your instal-
lations operating well. Note these eventual first signs of
problems:
• Accumulation of dust on the heating elements.
• Signs of overheating on the heater frame.
• Traces of water or rust on the control box.
4.2 Electrical Inspection
Two weeks after start-up, all electric connections to con-
tactors should be checked and tightened up. Before each
heating season, check the resistance between the heating
elements and ground. It is also recommended to check
the electrical connections to heating elements, magnetic
contactors and main power lugs. This inspection is rec-
ommended monthly during the first four months of opera-
tion. After that, two inspections per heating season are
sufficient.
4.3 Checkpoints
• Check all fuses.
• Check the resistance to ground for each circuit.
• Check the resistance phase-to-phase for each cir-
cuit.
• Check the tightening of connections at all contactors
and heating elements.
• Check all contactors.
4.4 Off-season Maintenance
Where tubular heating elements are used, it is strongly
recommended that you start the heating system from time
to time. This precaution will prevent moisture from perco-
lating through the terminal gaskets into the heating ele-
ment and accumulating in the insulating powder. Should
a heater be shut off for a long period, we recommend that
you check carefully the resistance to ground for each cir-
cuit. It is important not to power a heater when too low a
resistance to ground has been measured. It is also recom-
mended to pay attention to any other heater operating in
normal conditions. Control components such as step con-
trollers or modulating valves (SCR) should be maintained
and checked according to respective Manufacturer’s in-
structions. Any defective components should be replaced
only with identical original parts.
VCES-VHC-IOM-1F – VHC-36, -42 & -50
80