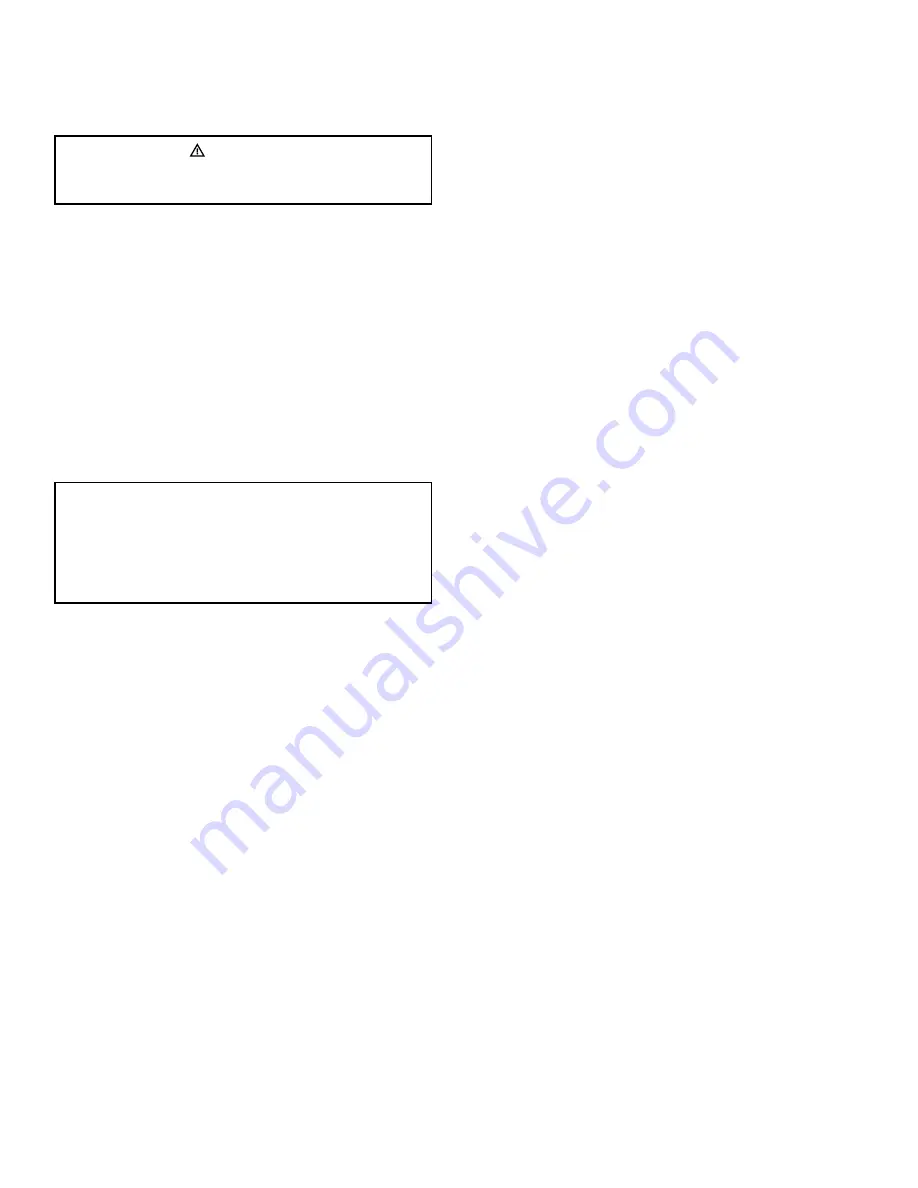
Refrigerant Systems
On units with integrated DX or WSHP cooling, the re-
frigeration system is factory completed, leak tested and
charged with R410a refrigerant. The type of refrigerant
and charge is based on calculated volumetric capac-
ity and stamped on the nameplate. On units with split
refrigerant systems where the condenser or condenser/
compressor sections are remotely installed, the Installing
Contractor is responsible for designing and completing
the refrigerant system, calculating the charge, leak testing,
evacuation, charging refrigerant and adjusting the charge.
Compressors
Scroll type compressors are used by Venmar CES. Main-
tenance and service on compressors must be completed
by a licensed service mechanic. Provincial or state regula-
tions frequently require such qualifications for compressor
maintenance. If a compressor cycles, leaks or has any
defects, contact Venmar CES as soon as possible. See
for maintenance summary,
troubleshooting and
charge.
Condenser
Condenser Fans and Motors, Air Cooled
The units contain direct drive condenser fan and motor
assemblies. The condenser fan motors are three-phase
heavy duty type complete with permanently lubricated
ball bearings, inherent three-phase protection and NEMA
Class B insulation. Motor shafts are coated for rust pro-
tection. Each motor is mounted on a bracket which is
constructed on heavy gauge steel. Fan guards are fur-
nished on the top for safety purposes. The condenser fan
motors are cycled to provide head pressure control down
to 50°F [10°C] ambient.
Condensers, Water Cooled
Water cooled or water source heat pump units may
contain either plate or coaxial water cooled condenser/
evaporator. Periodically, plate and coaxial heat exchang-
ers should be chemically cleaned to ensure optimum
condenser efficiency. Frequency of cleaning will depend
on individual water conditions hence a suitable cleaning
schedule should be arranged based on experience and
knowledge of the building or local water supply loop.
Coils
Dirt on the surface of the coil reduces its ability to transfer
heat which lowers the efficiency of the unit, resulting in
poor air quality and expensive operating costs. Because
of the condensate on the coil, the dirt often becomes wet
and contributes to the growth of microbial organisms.
Negligence in maintenance may result in serious health
related indoor air quality problems.
The coil should be kept clean for maximum performance.
To achieve maximum efficiency, clean the coil often during
periods of high demand or when dirty conditions prevail.
Venmar CES recommends cleaning the coil a minimum of
once per year to prevent dirt buildup in the coil fins where
it may not be visible.
Coil fins can be cleaned by using steam with detergent,
hot water spray or a commercial chemical coil cleaner.
After cleaning the coil, be sure to rinse thoroughly.
Cleaning Procedure
1. Shut down the unit by closing the main disconnect at
the power inlet.
2. Open panels or doors to gain access to both sides
of the coil section.
3. Remove soft debris from both sides of the coil with a
soft brush.
4. Using a steam cleaning machine, clean the leaving
airside of the coil first (going downward) then clean
the entering airside. Use a block-off to prevent the
steam from penetrating a dry section of the unit.
5. Allow the unit to dry thoroughly before restoring
power.
6. Damaged coil fins (excluding brazed aluminum)
should be straightened by using a fin comb.
7. Close all panels and doors once the coil is dry.
8. Restore electrical power to the unit.
CAUTION
Do not use acidic chemical coil cleaners. Do not use al-
kaline chemical coil cleaners with a pH value greater than
8.5 or lower than 6 (after mixing) without using an alu-
minum corrosion inhibitor in the cleaning solution. Using
these types of cleaners may result in unit damage.
WARNING
Disconnect the main power switch to the unit before per-
forming service and maintenance procedures.
VCES-VHC-IOM-1F – VHC-36, -42 & -50
24