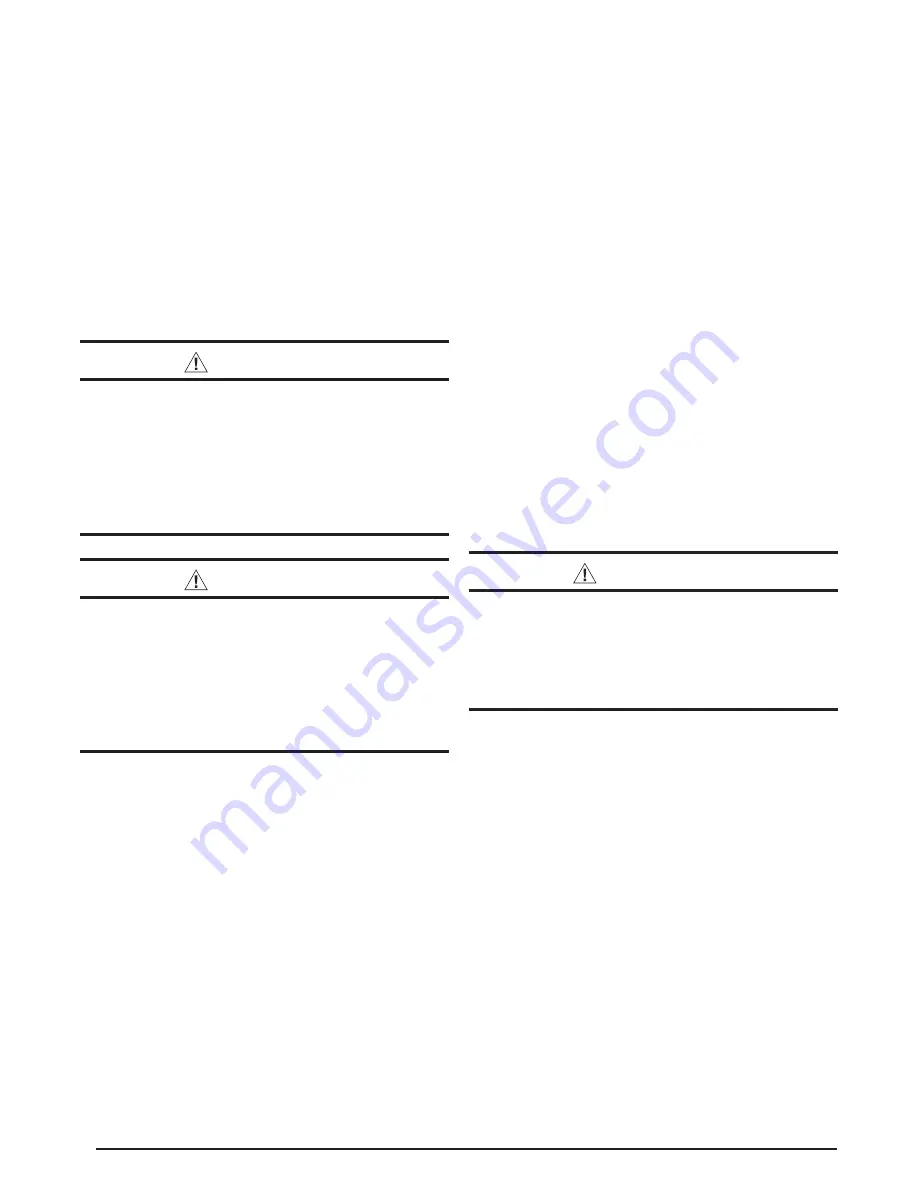
4
INSTALLATION/VERIFICATION OF THE
SYSTEMS EXPANSION DEVICE
After outdoor and indoor unit placement has been determined,
refer to the Quick Reference Data sheet for information
on the appropriate fixed orifice metering device to use for
the equipment. Verify that the installed expansion device
matches those requirements or install the correct expansion
device. Note: Some outdoor units may include the correct
indoor orifice expansion device for the installation application
but is dependent upon the actual unit match. The correct
expansion device or kit is available for all approved Nortek
listed applications from the parts department.
Connecting Refrigerant Tubing Between the Indoor
& Outdoor Unit
CAUTION:
When connecting refrigerant line-sets together,
it is highly recommended that dry nitrogen be
flowing through the joints during brazing to
prevent internal oxidation and scaling. Copper
oxides, internal to the system can damage the
compressors bearings and seals, block small
orifices and microchannels or otherwise damage
components.
CAUTION:
When performing brazing operations always
protect the system components and seals from
the possibility of heat damage. Remove all
caps, plugs and Schrader valve cores on piping
system components just prior to assembly and
brazing. Use good brazing practices to protect
components from the heat and flame of the
brazing torch.
After outdoor and indoor unit placement has been determined,
route refrigerant tubing between the equipment in accordance
with sound installation practices.
• Refrigerant tubing should be routed in a manner that
minimizes the length of tubing and the number of bends
in the tubing. If precise forming of refrigerant lines is
required, a copper tubing bender is recommended. Avoid
sharp bends and contact of the refrigerant lines with metal
surfaces.
• Refrigerant tubing should be supported in a manner that the
tubing will not vibrate or abrade during system operation.
• Tubing should be kept clean of foreign debris during
installation.
• Every effort should be made by the installer to ensure that
the field installed refrigerant containing components of
the system have been installed in accordance with these
instructions and sound installation practices to insure
reliable system operation and longevity.
• The maximum recommended interconnecting refrigerant
line lengths is 75 ft. and the vertical elevation difference
between the indoor and outdoor sections should not exceed
20 ft.
• A filter dryer is provided with the unit and must be installed
in the liquid line of the system. If the installation replaces a
system with a filter dryer already present in the liquid line,
the filter dryer must be replaced with the one supplied with
the unit. The filter dryer must be installed in strict accordance
with the manufacturer’s installation instructions.
• Optional equipment such as liquid line solenoid valves,
low ambient, etc., should be installed in strict accordance
with the manufacturer’s installation instructions.
• After the completion of all brazing operations and when
the components have been properly cooled, replace all the
seals, Shrader cores and caps which had been previously
removed. It is recommended that all seals be either
lubricated with a light coat of refrigerant oil. Always verify
that oil applied matches the oil type listed on the compressor
nameplate. A thread sealant which is compatible with
the system refrigerant and oil can be sparingly applied if
desired.
CAUTION:
If repairs are necessary to the refrigerant line-
set or indoor setup after the initial installation,
then when servicing, cover or seal openings to
minimize the exposure of the refrigerant system
to air to prevent accumulation of moisture and
other contaminants.