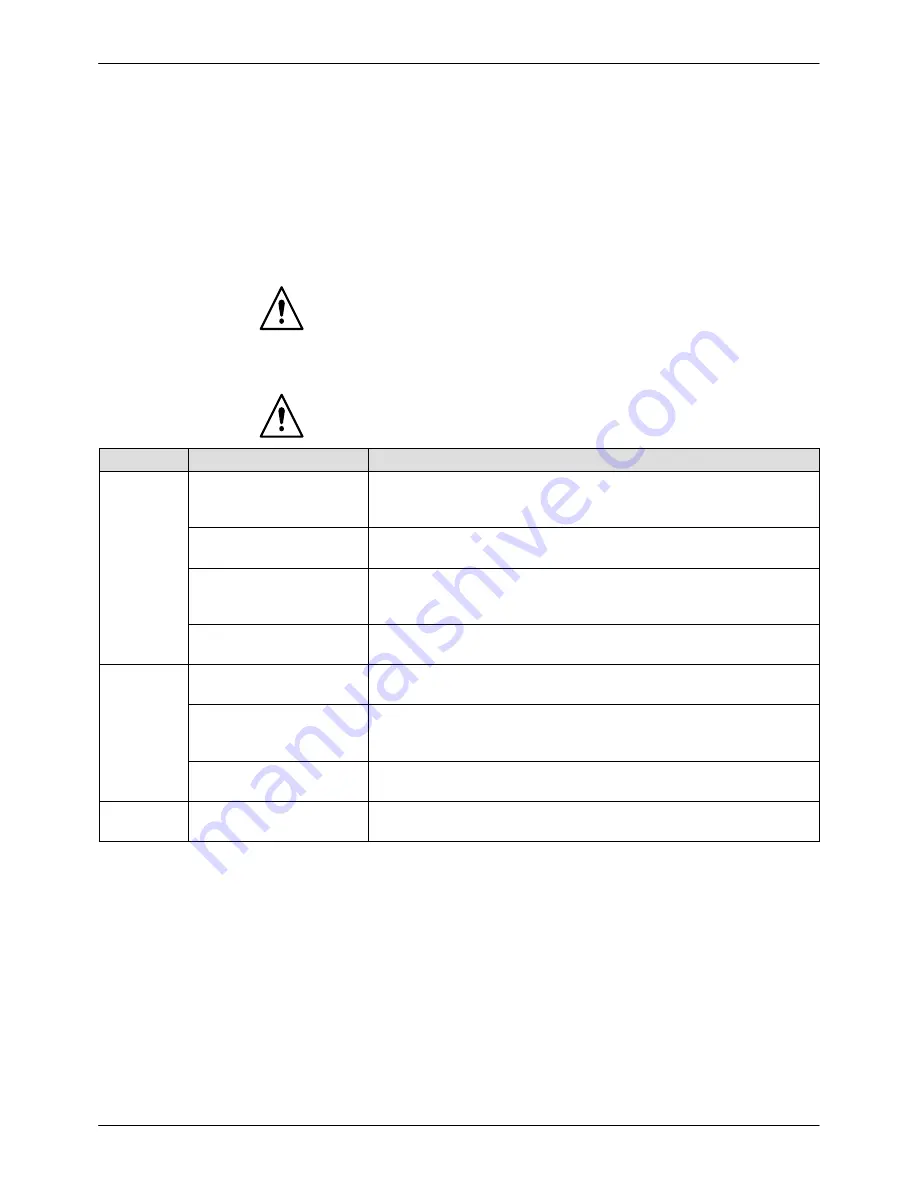
Rhino
R
VE Bulk Unloaders, 125-mm Frame
30
Part 1608271-04
E
2019 Nordson Corporation
Maintenance
This section details the preventative maintenance procedures for the
unloader. The frequencies listed are only guidelines. Always perform
preventative maintenance procedures according to your facility
maintenance schedule.
It may be necessary to adjust frequencies due to the facility environment,
process parameters, material being applied, or experience.
WARNING:
Never use halogenated hydrocarbon solvents to clean
aluminum parts or to flush any system. Cleaning agents, coatings and
paints, or adhesives may contain halogenated hydrocarbon solvents.
Obtain and read the SDS for each material and solvent being used.
WARNING:
Always relieve system pressure before servicing equipment.
Trigger all dispensing devices and bleed off system pressure.
Frequency
Item
Task
Daily
Material Supply
Make sure that the material supply is free of dust and other
contaminates. Contaminates may affect pump performance or
clog the applicator.
Lines and Hoses
Check all hydraulic and pneumatic connections and tighten them
if required. Inspect all pneumatic tubing for bends or kinks.
Solvent Chamber
Check the level of fluid in the solvent chamber. Refill the solvent
chamber with fluid if necessary. Refer to the pump manual for
the solvent chamber fluid type and part number if necessary.
Customer-Supplied Air
Filter/Separator
Drain the accumulated water if necessary.
Weekly
Drum Unloader
Clean the top of the unloader cylinders. Clean any material from
the top of the follower plate and around the follower plate seals.
Follower Plate Seals
Inspect the follower plate seals for damage or signs of excessive
material leakage and replace if necessary. Refer to the
Rhino
VE Follower Plate Module
manual for replacement procedures.
Regulator Settings
Check the air motor regulator and elevator regulator settings and
adjust if necessary.
−
−
−
−
−
−
Pump
Refer to the
Rhino SD2/XD2 Pumps
manual for maintenance
procedures.