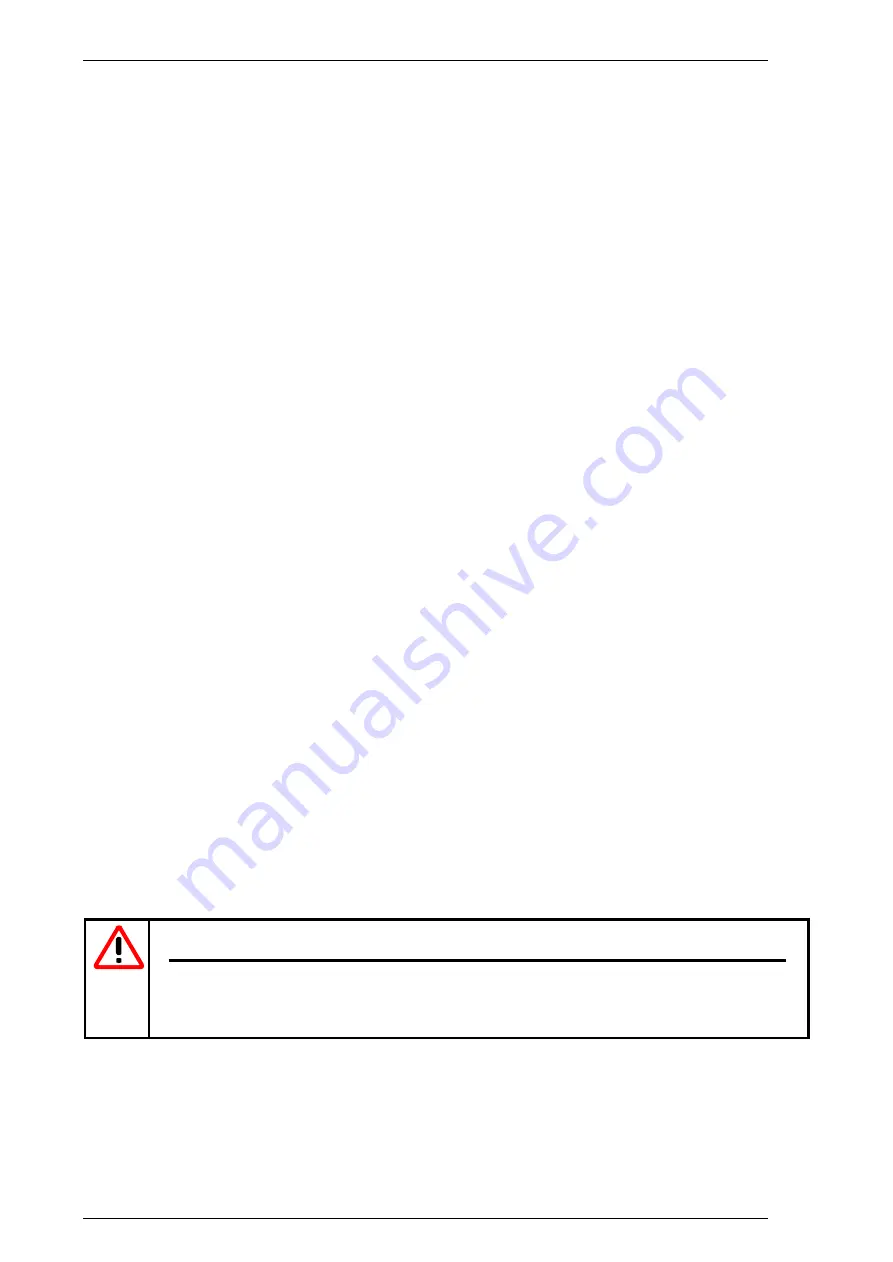
NORDAC SK 1000E Hardware description
10
BU1100 GB
2.3
Wiring guidelines
The servo controller is developed for operation in industrial environments where high values of
electromagnetic interference are expected. In general, correct installation ensures safe and problem-
free operation. If limit values exceeding the EMC guidelines are probable, the following information
may be useful.
(1) Ensure that all equipment in the cabinet is securely earthed using short earthing cables that have
large cross-sections and which are connected to a common earthing point or earthing rail. It is very
important that every connected controller (e.g. an automation device) is connected, using a short
cable with large cross-section, to the same earthing point as the servo controller itself. Flat
conductors (e.g. metal brackets) are preferable as they have low impedance at higher frequencies.
The PE lead of the motor controlled by the servo controller must be connected as directly as
possible to the earth connection of the cooling element together with the PE of the relevant servo
controller electrical system. The presence of a central earthing rail in the control cabinet and the
bringing together of all PE conductors to this rail normally ensures safe operation. (See also the
chapters: Line and motor connections, EMC)
(2) Where possible, shielded cables must be used for the control circuits. Carefully terminate cable
ends and ensure that the wires do not run over longer sections unshielded.
The shields of analog setpoint cables should only be earthed on one side on the servo controller.
(3) The control cables must be kept distant from load cables by using separate cable ducts, etc. If
cables intersect, then an angle of 90° should be used where possible.
(4) Ensure that the contactors in the cabinet are interference protected, either by RC circuits in the
case of DC contactors or by free-wheeling diodes for AC contactors,
whereby the interference
traps must be positioned on the contactor coils
. Varistors for over-voltage limitation are also
effective. This interference suppression is particularly important when the contactors are controlled
by the servo controller.
(5) Shielded or armoured cables must be used for the load connections between motor and brake
resistor. These must be applied to as much surface as possible on the shield angles directly on the
servo controller with the supplied earthing clamps.
(6) When the drive is to operate in an environment sensitive to electromagnetic interference, it is
recommended that noise suppression filters are used to restrict the cable-dependent and radiated
interference from the servo controller. In this case, the filter must be mounted as closely as
possible to the servo controller and fully earthed.
In addition, the servo controller must be installed, together with the line filter, in an EMC-proof
enclosure with EMC-proof cabling.
The safety regulations must be complied with under all circumstances when installing
the servo controller!
Note
The control cables, line cables and motor cables must be laid separately. In no case
should
they
be
laid
in
the
same
protective
pipes/installation
ducts.
The test equipment for high voltage insulations must not be used on cables that are
connected to the servo controller.