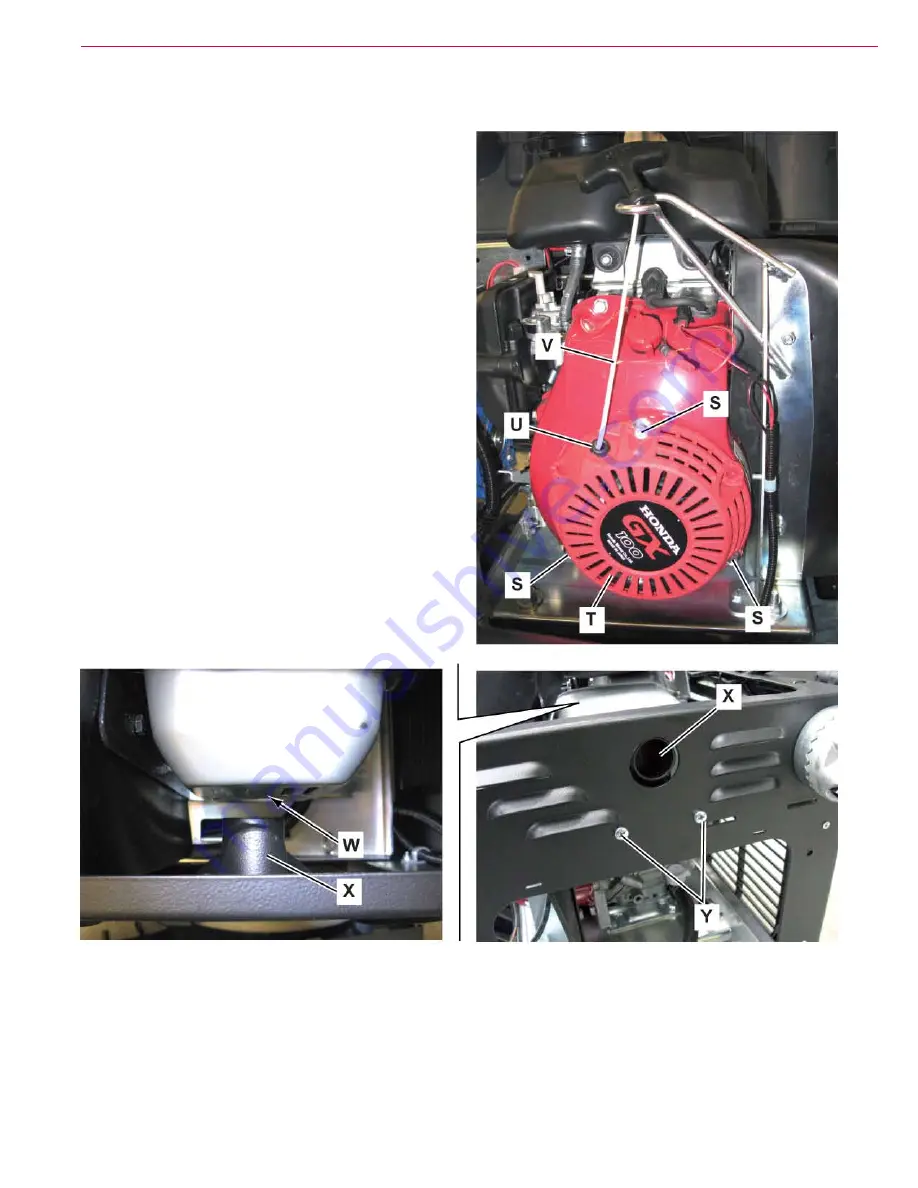
Petrol Engine System
95
Service Manual – SW900
P200334
Assembly
12 Assemble the components in the reverse order of
disassembly, and note the following:
• After assembling the engine belt, perform the
belt check/adjustment (see the procedure in
the relevant paragraph)
• When installing a new engine:
– Check if there is oil in the engine
– Check for proper alignment of the engine
exhaust pipe (W) to the machine exhaust
end pipe (X); if necessary loosen the
screws (Y) and adjust Then tighten the
screws (Y)
– Remove the three screws (S) and turn the
case (T) for 120° to turn the outlet hole
(U) of the engine pull-start cord (V) in
the position shown in the figure. Tighten
the screws (S)
Petrol Engine Assembly Removal/Installation (Continues)
Содержание SW900
Страница 12: ...General Information 12 Service Manual SW900 Machine Nomenclature SW900 B know your machine P200251 ...
Страница 13: ...General Information 13 Service Manual SW900 Machine Nomenclature SW900 B Continues P200252 ...
Страница 14: ...General Information 14 Service Manual SW900 Machine Nomenclature SW900 B Continues P200253 ...
Страница 15: ...General Information 15 Service Manual SW900 Machine Nomenclature SW900 B Continues P200254 ...
Страница 16: ...General Information 16 Service Manual SW900 Machine Nomenclature SW900 P know your machine P200255 ...
Страница 17: ...General Information 17 Service Manual SW900 Machine Nomenclature SW900 P Continues P200256 ...
Страница 18: ...General Information 18 Service Manual SW900 Machine Nomenclature SW900 P Continues P200257 ...
Страница 19: ...General Information 19 Service Manual SW900 Machine Nomenclature SW900 P Continues P200258 ...
Страница 23: ...General Information 23 Service Manual SW900 Dimensions P200259 ...
Страница 119: ...Side Broom System 119 Service Manual SW900 Wiring Diagram SW900 B P200343 Wiring Diagram SW900 P P200344 ...