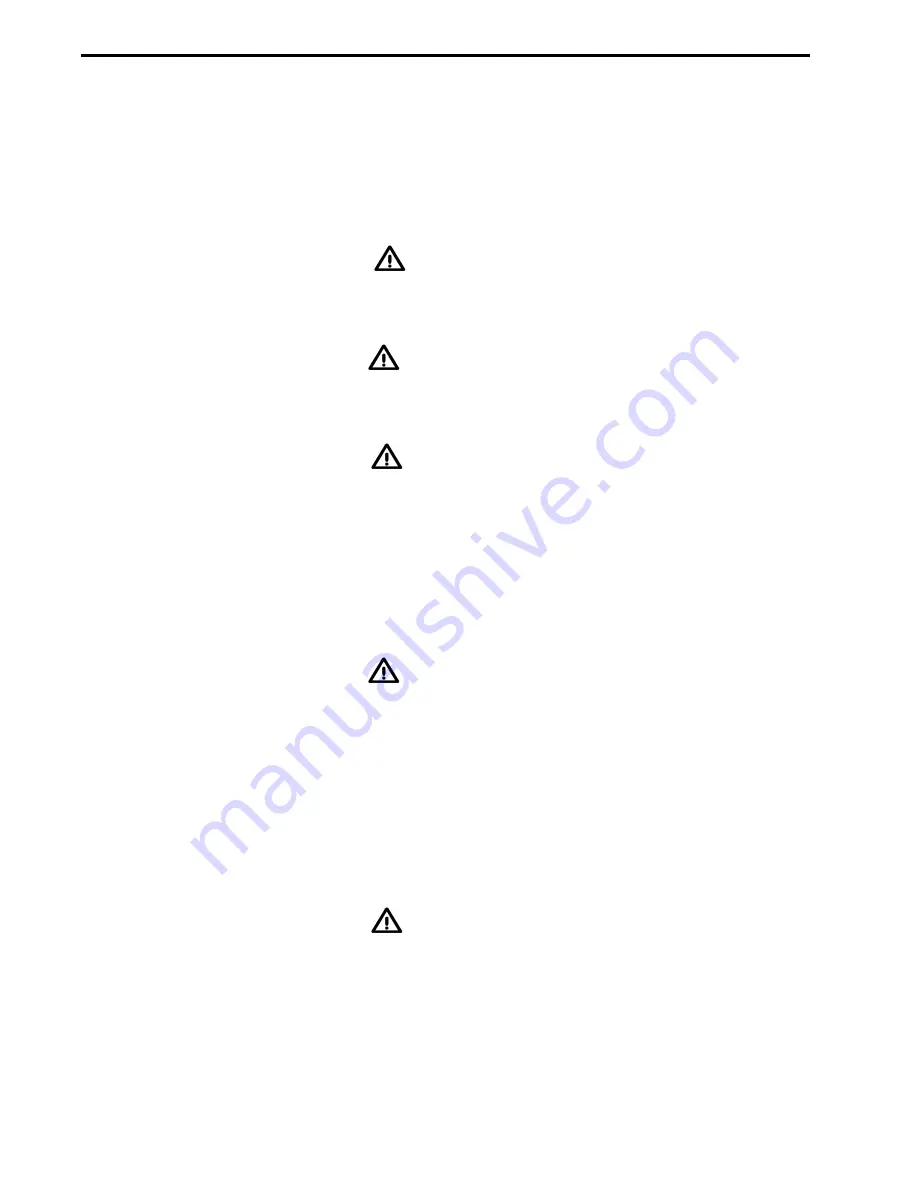
________________________________________________________________________________________________________________________________________________________________________________________________________________________________________________________________________
SYMBOLS
Nilfisk uses the symbols below to signal potentially dangerous conditions. Always read this information
carefully and take the necessary steps to protect personnel and property.
DANGER!
Is used to warn of immediate hazards that will cause severe personal injury or death.
WARNING!
Is used to call attention to a situation that could cause severe personal injury.
CAUTION!
Is used to call attention to a situation that could cause minor personal injury or damage to the machine or other
property.
________________________________________________________________________________________________________________________________________________________________________________________________________________________________________________________________________
GENERAL SAFETY INSTRUCTIONS
WARNING!
Keep sparks, flame and smoking materials away from the batteries. Explosive gases are vented during
normal operation.
Remove all jewelry when working near electrical components.
Disconnect one of the battery terminals when servicing electrical components.
Never work under a machine without safety stands or blocks to support the machine.
CAUTION!
Carefully read all instructions pertaining to a service function before performing that function.
Take precautions to prevent hair, jewelry, or loose clothing from becoming caught in moving parts.
SAFETY
1
BA 500
Service Manual