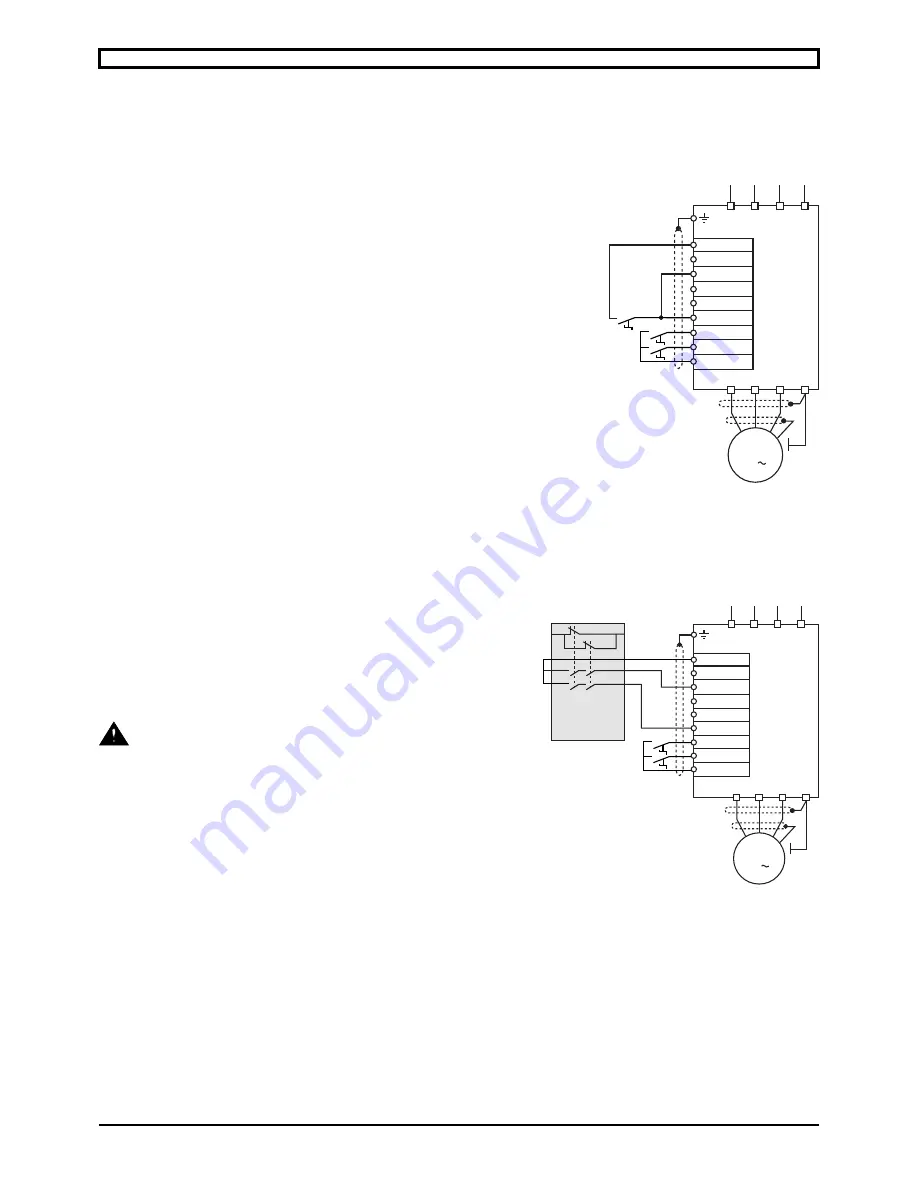
27
CONNECTIONS
Powerdrive MD2S Installation guide
4972 en - 2017.08 / d
3.3 - STO-1/STO-2 inputs: Safe Torque Off
function
The STO-1 and STO-2 inputs are safety inputs that can be
used to disable the drive output so no torque at the motor
shaft is generated.
They are independent of one another. They are created by
simple hardware not connected to the microcontroller. They
act on two different stages of the IGBT output bridge control.
To enable the drive, the STO-1 and STO-2 inputs must be
connected to the +24V source.
The opening of a minimum of one input locks the output
bridge.
These 2 inputs can be used in conjunction to create a "Safe
Torque Off" function with a logic combining 2 separate
channels.
In this configuration, the "Safe Torque Off" function is
guaranteed with a very high level of integrity in conformity
with standards:
- EN 61800-5-2
- EN/ISO 13849-1: 2006; PLe
- IEC/EN 62061: 2005; SIL3
(CETIM approval no. CET0047520)
This built-in function enables the drive to act as a contactor
that switches off the motor power, allowing a deceleration in a
free wheel mode. This corresponds to an uncontrolled stop in
accordance with stop category 0 og IEC 60204-1.
The STO-1 and STO-2 inputs are compatible with self-tested
logic outputs in controllers such as PLCs, for which the test
pulse lasts for 1 ms maximum.
If the data sent by the 2 inputs are not identical, this generates
a drive trip. The RL1 relay opens and the drive indicates
a "t.r./63" trip on the drive 2-digit display or "STO input
inconsistency" trip on the parameter-setting interface.
For correct use, the power and control connection diagrams
described in the following paragraphs must be adhered to.
• The STO-1/STO-2 inputs are safety components
which must be incorporated in the complete
system dedicated to machine safety. As for any
installation, the complete machine must be subject to a
risk analysis. The integrator must determine the safety
category which the installation must comply with.
• The STO-1 and STO-2 inputs, when open, lock the drive,
so the dynamic braking function is no longer available.
If a braking function is required before the drive secure
disable lock is applied, a time-delayed safety relay must
be installed to activate the locking automatically after the
end of braking.
If braking needs to be a machine safety function, it must
be provided by an electromechanical solution since the
dynamic braking by the drive function is not considered
as a secure disable function.
• The STO-1/STO-2 inputs do not provide the electrical
isolation function. Prior to any work carried out on the
drive / installation, the power supply must therefore
be switched of through an approved isolating device
(isolator, switch, etc).
• The line switch integrated as an option in the drive
does not isolate the drive input busbars. During the
installation and maintenance phases, make sure that the
power supply line is disrupted.
3.3.1 - Single channel locking (SIL1 - PLb)
3-phase AC power supply, in accordance with safety standard
IEC/EN 62061: 2005 and EN/ISO 13849-1: 2006 - Single
channel locking (SIL1 - PLb).
U
V
W
Px2
+24V Ref
DO1
STO-1
DI2
DI3
STO-2
DI4
DI5
+24V Ref
M
3
PE
PE
L1 L2
L3
Safe Torque Off/Drive
enable input
Run FWD/Stop
Run REV/Stop
3.3.2 - Double channel locking (SIL3 - PLe).
3-phase AC power supply, in accordance with safety standard
IEC/EN 62061: 2005 and EN/ISO 13849-1: 2006 - Double
channel locking (SIL3 - PLe)
U
V
W
Px2
+24V Ref
DO1
STO-1
DI2
DI3
STO-2
DI4
DI5
+24V Ref
M
3
PE
PE
L1 L2
L3
Output stage of a
safety relay
Run FWD/Stop
Run REV/Stop