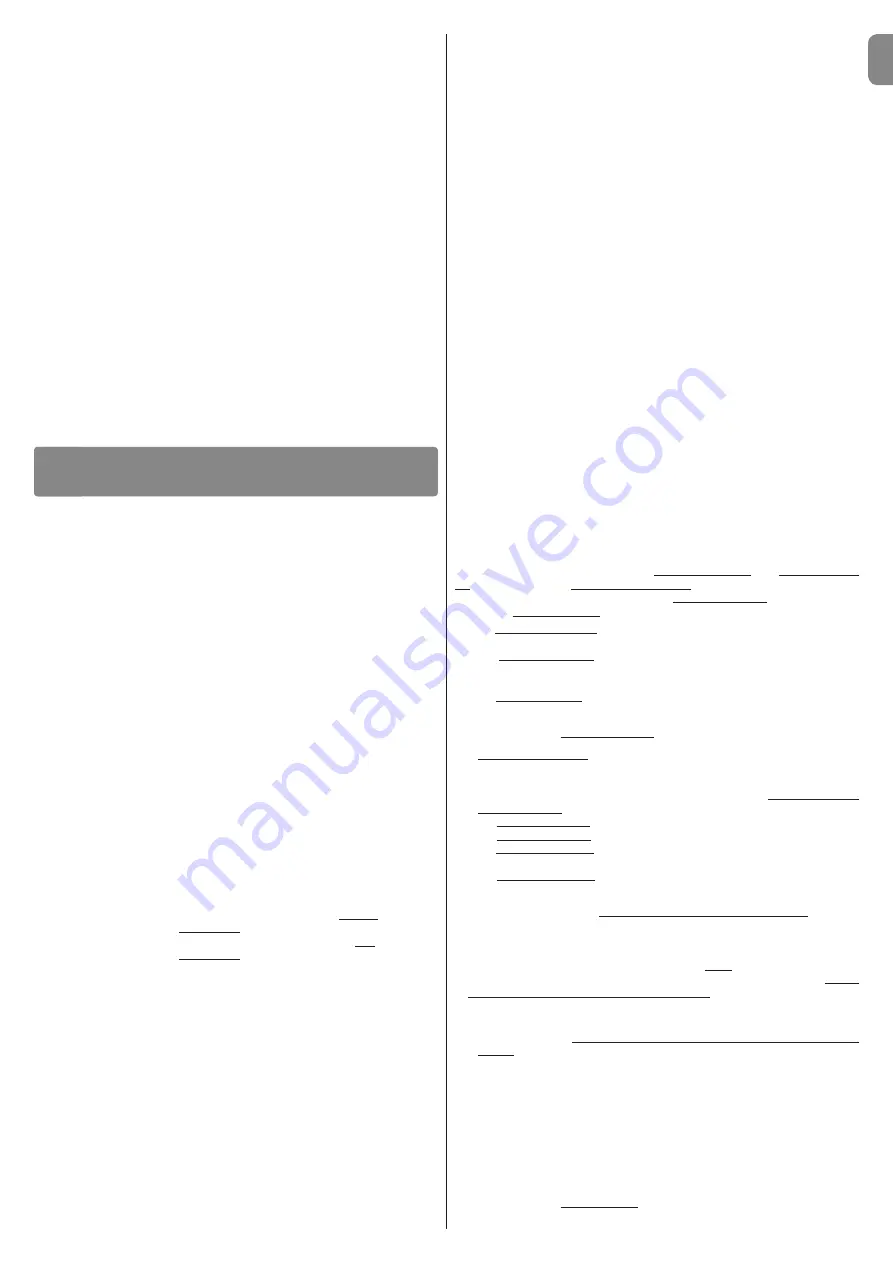
EN
English –
3
2.3 - Typical system
Fig. 2a
shows an example of an automation system set up with
Nice
compo-
nents:
a
) Control unit;
b
) Gearmotor;
c
) Flashing light;
d
) Photocell;
e
) Digital keyboard
- Transponder reader - Key selector;
f
) Photocell post;
g
) Opening mechanical
stops;
h
) Closure mechanical stops;
i
) Electric lock.
These parts are positioned according to a typical standard layout. With refer-
ence to
fig. 2a
, locate the approximate position for installation of each com-
ponent making up the system.
IMPORTANT
• Before installation, prepare the
electrical cables needed for your system, referring to
fig. 2b
and “Table 1 -
Technical characteristics of electrical cables”. • During installation of ducting for
electrical cables and the introduction of cables into the control unit enclosure,
be aware that due to possible water deposits in the junction boxes, the con-
necting ducts may form condensation inside the control unit which is liable to
damage the electronic circuits.
2.4 - Installation of control unit
To mount the control unit, proceed as shown in
fig. 3
:
01.
Open the control unit box by undoing the relevant screws (
fig. 3-A
);
02.
Prepare the electrical cable routing holes (
fig. 3-B
);
03.
Mount the box (
fig. 3-C
);
04.
The electrical connections can now be made: see chapter 3.
Important!
– To prepare the inlets for the electrical cable ducting, holes must
be drilled in the lower side of the control unit box.
Note
– If necessary, the lat-
eral cable inlet may be used, but only with the aid of suitable duct fittings.
To install the other devices present in the automation, refer to the relevant in-
struction manuals.
ELECTRICAL CONNECTIONS
3
The electrical connection of the various devices (photocells, digital keyboard,
transponder card readers, etc.) contained in the automation with the control
unit must be made by means of the Nice “Bluebus” system.
3.1 - Description of electrical connections
See
fig. 6
and
Table 3
.
3.2 - Electrical connections of MC824L control unit
After mounting the control unit box and preparing the electrical cable holes
(chapter 2.4 and fig. 3), make the electrical connections:
IMPORTANT!
– All electrical connections must be made with the unit disconnected
from the mains power supply and with the buffer battery disconnect-
ed, if present in the automation.
– Connections must be made exclusively by qualified personnel.
–
The
electrical power line must be fitted with a device that enables complete
disconnection of the automation from the mains. The disconnection device
must have a gap between contacts that ensures complete disconnection
in the conditions of overvoltage category III, in compliance with installation
regulations. If necessary, this device guarantees rapid and safe disconnection
from the mains, and therefore should be located in view of the automation.
However, if located in a concealed position, it must have a system that blocks
against inadvertent or unauthorised reconnection to prevent all risks. The dis-
connection device is not supplied with the product.
01.
First connect the electric power cable (
fig. 4
) and secure by means of the
cable clamp;
02.
Then connect the electric cables of motors M1 and M2, observing the
symbols on the label (
fig. 5
):
a)
connect the motor that activates the lower leaf (the second to start the
opening manoeuvre) to terminal M1;
b)
connect the motor that activates the upper leaf (the first to start the
opening manoeuvre) to terminal M2.
IMPORTANT! – If there is only one gearmotor in the system, con-
nect it to terminal M2 leaving terminal M1 free;
03.
Then connect the electric cables of the various devices present, with refer-
ence to
fig. 6
and paragraph 3.3.
Note
– To facilitate cable connections,
the terminals can be removed from their seats.
3.3 - Connection of other devices to MC824L
If further devices present in the system need to be powered, for example a
transponder card reader or the key selector light, these devices can be con-
nected to the control unit using terminals “P.P. (positive)” and “STOP (negative)”
(
fig. 6
). The power supply voltage is 24 Vdc, -30% ÷ +50%, with maximum
available current 200 mA.
Note
– The voltage present on terminals “P.P.” and “STOP” remains connected
even when the “Stand By” function is activated on the card.
3.4 - Connected device address assignment to MC824L
To enable control unit recognition of the devices connected to the BlueBus sys-
tem, they need to be routed. This operation must be performed by positioning
the electric jumper correctly on each device; see the relative instruction manual
of individual devices: see
fig. A
and
Table 2
.
At the end of the installation procedure or following the removal of photocells
or other devices, the self-learning procedure for these devices must be per-
formed. See paragraph 3.6.
3.5 - Initial start-up and electrical connections
After powering up the control unit, perform the following checks:
•
After a few seconds, make sure that the “Bluebus” LED (
fig. 7
) flashes regu-
larly with a frequency of about one flash per second.
•
Make sure that the LEDs on the photocells (
fig. 6
) flash (both on TX and RX).
The type of flashing is not important during this stage.
•
Make sure that the flashing light connected to the FLASH output is off.
If the above conditions are not satisfied, switch off the power supply to the
control unit and check the electrical connections previously made.
3.6 - Learning of the devices connected to MC824L
After the initial power-up, the control unit must be able to recognise the devices
connected to the “
Bluebus
” and “
Stop
” inputs.
IMPORTANT! – The learning procedure must be performed even if no
device is connected to the control unit.
The control unit is able to recognise the various connected devices individually
through the self-learning procedure and detect possible faults. For this reason
it is necessary to perform self-learning every time a new device is added or an
existing device is removed.
To indicate when the self-learning procedure is required, LEDs
L1
and
L2
on
the control unit (
fig. 7
) emit a number of slow flashes:
01.
Press and hold down
and “
Set
” keys at the same time (
fig. 7
).
02.
Release the keys when LEDs L1 and L2 start flashing quickly (after approx.
3 seconds).
03.
Wait a few seconds for the control unit to complete the device learning
phase.
04.
At the end of this phase, the “Stop” LED must be lit and LEDs “L1” and
“L2” must be turned off (LEDs L3 and L4 may start flashing).
3.7 - Recognition of mechanical stop positions and other door
positions
After recognition of connected devices (paragraph 3.6), proceed with recogni-
tion of mechanical stop positions, i.e. maximum opening and maximum clos-
ing. Recognition is an
automatic procedure (paragraph 3.7.1)
, however, in
case of difficulty, run recognition using the manual procedure (paragraph 3.7.2)
or with the mixed procedure (paragraph 3.7.3).
• In the automatic procedure, the control unit recognises the mechanical stops and
calculates the best overlaps for the doors (positions “SA” and “SC” in
fig. B
).
• In the manual procedure, the six positions (
fig. B
) are programmed one by
one, while the doors are moved to the required points. The programming po-
sition is signalled when one of the LEDs flashes (L1...L6 - see
Table 4
).
• In the mixed procedure, the “automatic procedure” is run first, after which, with
the “manual procedure”, only positions “SA” and/or “SC” can be changed.
3.7.1 - Learning in automatic mode
01.
Press and hold down “
Set
” and
keys at the same time.
02.
Release the keys when Leds “
L3
” and “
L4
” start flashing quickly (after ap-
prox. 3 seconds).
03.
Check that automation runs the following manoeuvres
in the same se-
quence shown
:
a -
low speed closure of gearmotor M1 through to the mechanical stop;
b -
low speed closure of gearmotor M2 through to the mechanical stop;
c -
low speed opening of gearmotor M2 and gearmotor M1 through to the
mechanical stop;
d -
high speed closure of gearmotors M1 and M2.
Warnings:
• If the first manoeuvre (
a
) closes the door controlled by motor M1, stop the
recognition phase immediately using the “
” or “
” key. Then, reverse the
connections for the M1 and M2 motors on the control unit. Lastly, repeat the
procedure from point 01.
• If the first two manoeuvres (
a
and
b
) are to open the gate, stop the rec-
ognition phase immediately by pressing the “
” or “
” key. Then, on the
gearmotor that has run the opening manoeuvre, reverse the poles of the two
gearmotor wires (clamps 1 and 3 for M1 and clamps 4 and 6 for M2). Lastly,
repeat the procedure from point 01.
04.
At the end of the rapid closing manoeuvre on motors M1 and M2 (point
03 -
d
), LEDs “
L3
” and “
L4
” switch off, indicating that the procedure was
completed successfully.
Warnings:
• During the automatic learning procedure if a photocell trips or a device con-
nected to the “stop” input is activated, the procedure is interrupted and Led
L1 starts flashing. To resume the learning process the procedure must be
started again from point 01.
• The automatic recognition procedure can be run several times and at any
time, even after the installation phase, e.g. after changing the original position
of the mechanical stops.
3.7.2 - Learning in manual mode
Caution!
–
From step 03 onwards: