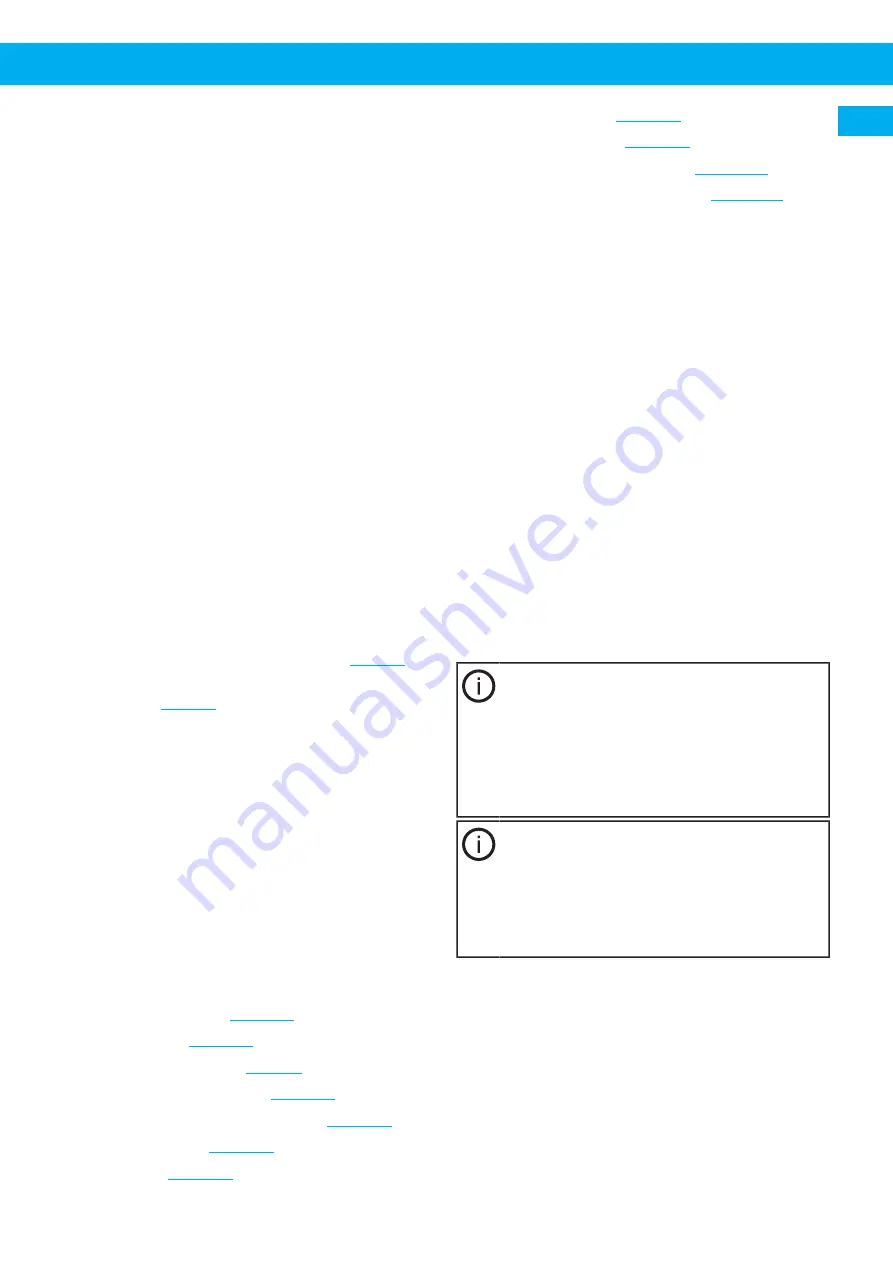
FlexFilter EX
FlexFilter EX. The transport velocity in the pipes may
vary depending on how much of the vacuum system is
used (infrequent use).
To keep the pipes clean a principle called “flushing”
may be used. Flushing can be applied by fitting a valve
at the end of the pipe system. By not using the rest
of the system, and opening the “flush valve”, a high
amount of air will flush the pipes clean. By “flushing”
each branch of the vacuum system separately, the risk
of dust deposits is minimized.
In larger vacuum systems it is recommended to install
valves in order to isolate one FlexFilter EX for main-
tenance while the others remain in normal operation.
To reduce the risk of impact sparks and explosion as a
result of unknown material coming into the inlet duct,
install an explosion safe pre-separator.
If the dust is abrasive it may be necessary to use thick-
walled (or rubber-coated) material in bends and other
exposed areas.
To avoid pressure losses, the duct system should be
as short as possible and designed with two or more
branches. Use larger diameters on the clean side to re-
duce pressure losses.
The distance to the suction source should be less than
25 meters.
12.3 Installation
Connect the pipe to the flanged inlet (see
/D)
Connect the pipe (clean side) to the outlet of the con-
trol filter (see
/C).
13 Electrical installation
13.1 Installation abstract
The FlexFilter EX is, as a stand-alone unit, simply a
filter with a feed out function. However, in order for
the FlexFilter EX to function properly and operate in
a safe way, several specific settings must be made to
the control system controlling the filter.
It is highly recommended that the FlexFilter EX is in-
stalled together with a Nederman control system such
as the HV Control Panel EX. HV Control Panel EX fulfils
all functionality and safety requirements.
13.2 Electrical components
Terminal box cover (see
/6)
Terminal box (see
/7)
TVFD solenoid valves (see
Cylinder position sensors (see
/15)
Cable gland, control system cable (see
/2)
Terminals (see
Terminal box fuse (see
/5).
Explosion Relief Panel Sensor (see
)
Solenoid valve cleaning cylinder (see
13.3 General requirements
To ensure proper function and required level of pro-
tection with regards to the equipment category, lis-
ted EC directives and standards, the fulfilment of the
following points are to be considered as minimum re-
quirements:
The electrical installation must be done by a certified
electrician. Note that not only national and local elec-
tric regulations must be fulfilled, but also the special
conditions for installations in areas classified as zones
with explosive atmospheres according to ATEX.
Check that proper measures have been taken to avoid
all types of electrical stray currents to and/or from the
piping system and electrical wiring.
Check that the correct voltage is connected to the ter-
minals in the terminal box (Table 1). Control signals
must be fused properly to avoid heating of the cables
in case of damage, short circuit or malfunction.
A lightning conductor must be installed if the FlexFil-
ter EX is installed outdoors. The installation of light-
ning conductors must follow national and local regula-
tions for such protection devices.
A signal from the Explosion Relief Panel Sensor
must immediately trigger a full stop of the op-
eration of the FlexFilter EX and close both slide
valves of the TVFD. Furthermore, the indic-
ation of a burst explosion relief panel should
trigger a work area alarm (visual and sounding),
warning employees and others of detected ex-
plosion and possible fire in the FlexFilter EX.
To minimize possible secondary damage and
spread of fire, it is important to develop the
proper documentation and checklists of how
to handle a fire in the filter. Such documents
should be developed in co-operation with the
local fire authorities and take into account the
properties of the collected material.
It is highly recommended that a fire alarm is connec-
ted to the filter control system. A triggered fire alarm
should immediately trigger a full stop in the operation
of the FlexFilter EX and close both slide valves of the
TVFD.
13.4 Terminal box requirements
The terminal box is a category 3D component with
special requirements indicated by the marking “X”. To
achieve the proper level of protection, special require-
ments regarding the system control, signal voltage
EN
39
Содержание FlexFilter EX Single
Страница 8: ...FlexFilter EX Figures B C A D E F G 15 45 15 45 15 45 1 1 m 3 ft R 1 m 3 ft 2 8 ...
Страница 12: ...FlexFilter EX D C A E F B G 4 12 ...
Страница 13: ...FlexFilter EX 1 2 3 5 6 4 7 9 8 5 13 ...
Страница 14: ...FlexFilter EX 4 5 6 3 2 1 6 1 6 4 9 5 8 7 3 2 7 14 ...
Страница 15: ...FlexFilter EX 5 s 1 s 30 min A B C USV LSV 8 A E E A B C D G F 9 15 ...
Страница 16: ...FlexFilter EX 10 11 12 16 ...
Страница 17: ...FlexFilter EX x1 x3 A B 13 17 ...
Страница 18: ...FlexFilter EX A A B B 14 18 ...
Страница 19: ...FlexFilter EX 15a x1 M12x30 x2 x2 1 2 3 15b 17 A B 16 19 ...
Страница 20: ...FlexFilter EX 17a 17b 17c 20 ...
Страница 21: ...FlexFilter EX 17d 1 3 2 6 10 bar 4 5 A 18 1 2 3 4 5 19 21 ...
Страница 22: ...FlexFilter EX A B 20 22 ...
Страница 23: ...FlexFilter EX 1 3 8 13 6 4 9 10 11 5 5 14 7 12 12 14 2 15 15 16 16 21 23 ...
Страница 25: ...FlexFilter EX 1 8 A GND 1 7 2 4 5 6 3 23 A B C 24 25 ...
Страница 26: ...FlexFilter EX 25 26 ...
Страница 27: ...FlexFilter EX A B 26 A B 27 27 ...
Страница 381: ...FlexFilter EX 20 回收利用 本产品的设计使组件材料可以回收利用 不同类型的材 料请按当地相关规定处理 有关产品达到使用寿命进行 报废时如有不确定 请联系经销商或 N e d e r m a n ZH 381 ...
Страница 387: ...www nederman com ...