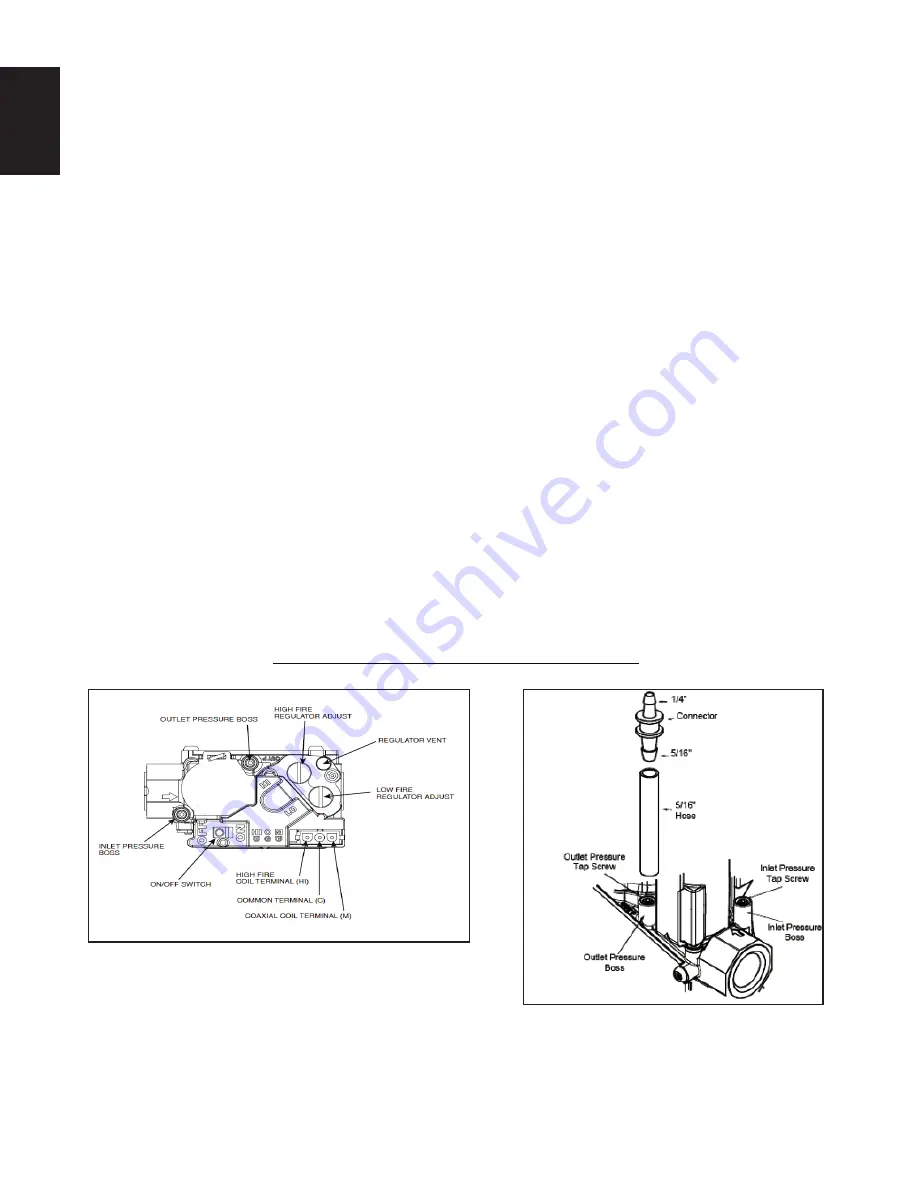
W415-2845 / B / 11.10.20
38
IOM
IOM
H18.4.2A
WHITE-RODGERS 36G54 TWO STAGE GAS VALVE
1. Turn off the gas and electrical supply to the furnace.
2. Back inlet pressure test screw (inlet pressure boss, see FIGURE 31) counterclockwise out one turn
maximum, with a 3/32” Allen wrench. Attach a hose and calibrated U-tube or digital manometer to the inlet
pressure boss. Hose should overlap boss 3/8”. The manometer must have a scale range of at least 0” to
15” of water column.
3. Turn ON the gas and electrical supply and operate the furnace and all other gas consuming appliances on
the same gas supply line. Using a leak detection solution, check for leaks around the gas valve/manifold
connection and the burner ori
fi
ces. Repair any leaks before continuing.
4. Measure furnace gas inlet pressure with burners
fi
ring. Inlet pressure must be within the range speci
fi
ed
on the furnace rating plate. 5-10.5” w.c. (Natural Gas) or 11-13” w.c. (LP).
If the inlet pressure differs from the rating plate, make the necessary adjustments to pressure regulator,
gas piping size, etc. and/or consult with local gas utility.
5. Turn off gas and electrical supply to furnace, remove the manometer hose from the inlet pressure tap
boss, and tighten the inlet pressure tap screw using the 3/32” Allen wrench. (Clockwise, 7 in-lb minimum).
6. Turn on the gas supply and electrical power to the furnace.
7. Using a leak detection solution, check for leaks at pressure boss screw. Bubbles forming indicate a leak.
SHUT OFF GAS AND FIX ALL LEAKS IMMEDIATELY!
8. Turn gas back on and test inlet pressure boss with leak detector.
9. If working on a natural gas system, contact the gas utility. They may insist on any service regulator
adjustments being made by their own staff.
If problems were encountered with obtaining enough pressure,
fi
rst examine the gas piping system to ensure
that it is correctly sized. Pipe sizing is speci
fi
ed in CAN/CSA-B-149.1 & 2, and in NFPA 54 / ANSI Z223.1. Be
sure to check for restrictions, partially closed valves, etc.
In some circumstances, high inlet pressure can be remedied with the use of an in line appliance regulator. If
an in line appliance regulator is used, ensure that it has the capacity to adequately handle the gas volume
required by the furnace and any other appliances receiving gas from the header serving the furnace.
13.4 CHECKING THE INLET GAS PRESSURE
FIGURE 26 - VALVE PRESSURE CHECK KIT
FIGURE 25 - WHITE RODGERS 36G54 GAS VALVE
Содержание WSX-EN Series
Страница 27: ...W415 2845 B 11 10 20 27 IOM FIGURE 14A DIRECT VENT TERMINAL CLEARANCES...
Страница 28: ...W415 2845 B 11 10 20 28 IOM IOM FIGURE 14B NON DIRECT VENT TERMINAL CLEARANCES...
Страница 62: ...W415 2845 B 11 10 20 62 IOM IOM 44 1 24 0 NOTES...
Страница 153: ...W415 2845 B 11 10 20 153 MU...
Страница 154: ...W415 2845 B 11 10 20 154 MU...
Страница 155: ...W415 2845 B 11 10 20 155 MU...