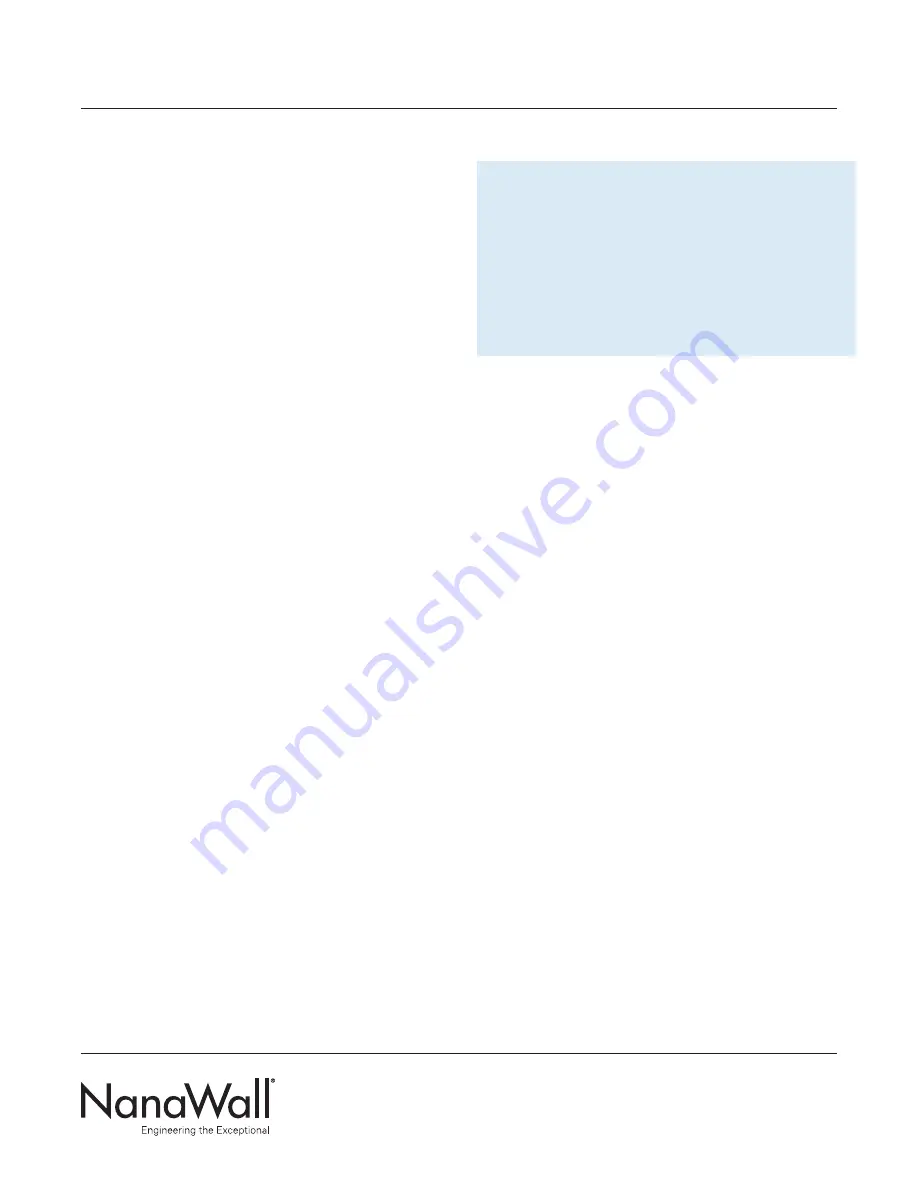
Use appropriate anchorage devices depending on the
project lateral load requirements and adjacent substrate
material and construction. If the factory pre-drilled holes
are sufficient, then 5/16” (8 mm) diameter screws can
be used. Make sure they are corrosion resistant and that
the screw head is small enough to fit inside the slot in
the middle of the head track, otherwise it will interfere
with the running carriages. Anchorage devices should
penetrate (embedment) or hold sufficiently to the
opening to withstand necessary lateral loading.
Attention should also be made to the minimum edge
distance that must be maintained for different substrates.
Generally, for wood frame, minimum embedment is
2 1/2” and minimum edge distance is 3/4” (19 mm),
for concrete minimum embedment is 1 1/4” (32 mm)
and minimum edge distance is 2” (51 mm).
Step A6
For all anchorage options, set the assembled part of the
upper track into the rough opening at the proper position,
relative to the support structure and the finish floor.
Step A7
Support the upper track
temporarily in a safe manner
.
Step A8
Place hard plastic horseshoe shims tightly at every fixing
point between the upper track and the header. Anchor
the head track with appropriate screws through the pre-
drilled holes or as needed.
See Sheet 6 of the Installation
Manual
.
Step A9
Assemble and install other segments of the upper track
in a similar manner. Make certain that the angles between
different upper track components are exact. If the
stacking bay has parallel legs, make sure that the legs are
exactly parallel.
IMPORTANT:
ADJUST EACH ANCHORAGE
POINT AS NEEDED TO MAKE THE UPPER TRACK
ABSOLUTELY LEVEL AND PLUMB. USE A TRANSIT/
LASER AND OTHER SIMILAR PRECISE MEASURING
EQUIPMENT TO MAKE THESE DETERMINATIONS.
MAKE SURE NO SHIMS ARE FORCED TO ENSURE
THAT THE UPPER TRACK IS NOT BOWED.
Upper track segments must be joined such that they
are even, tight and aligned perfectly. Otherwise, the
running carriages may wear out prematurely, which
will then not be covered by warranty. Placing shims
at the meeting points of track segments may help in
keeping the segments even, even though there may
not be anchorage holes at this point. See Sheet 5 of the
Installation Manual.
Make sure that all surfaces of the upper track
are clean and free of any debris, especially cuttings
from drilled holes.
Do not attach anything from the side against
the head track.
Step A10
Install the side jamb by pre-drilling holes for the
anchorage devices to connect the side jamb to the
opening.
See Sheet 5 of the Installation Manual.
Use appropriate screws or anchorage devices as
described in Step A5 above.
Set the side jambs in place and support them temporarily
with clamps.
Place hard plastic horseshoe type shims tightly at every
anchorage point between the side jamb and the wall
to make the side jamb absolutely square and straight.
Anchor the side jambs through the pre-drilled holes
and shims.
NANAWALL PRIVASEE OWNER’S MANUAL
PAGE 7 OF 15