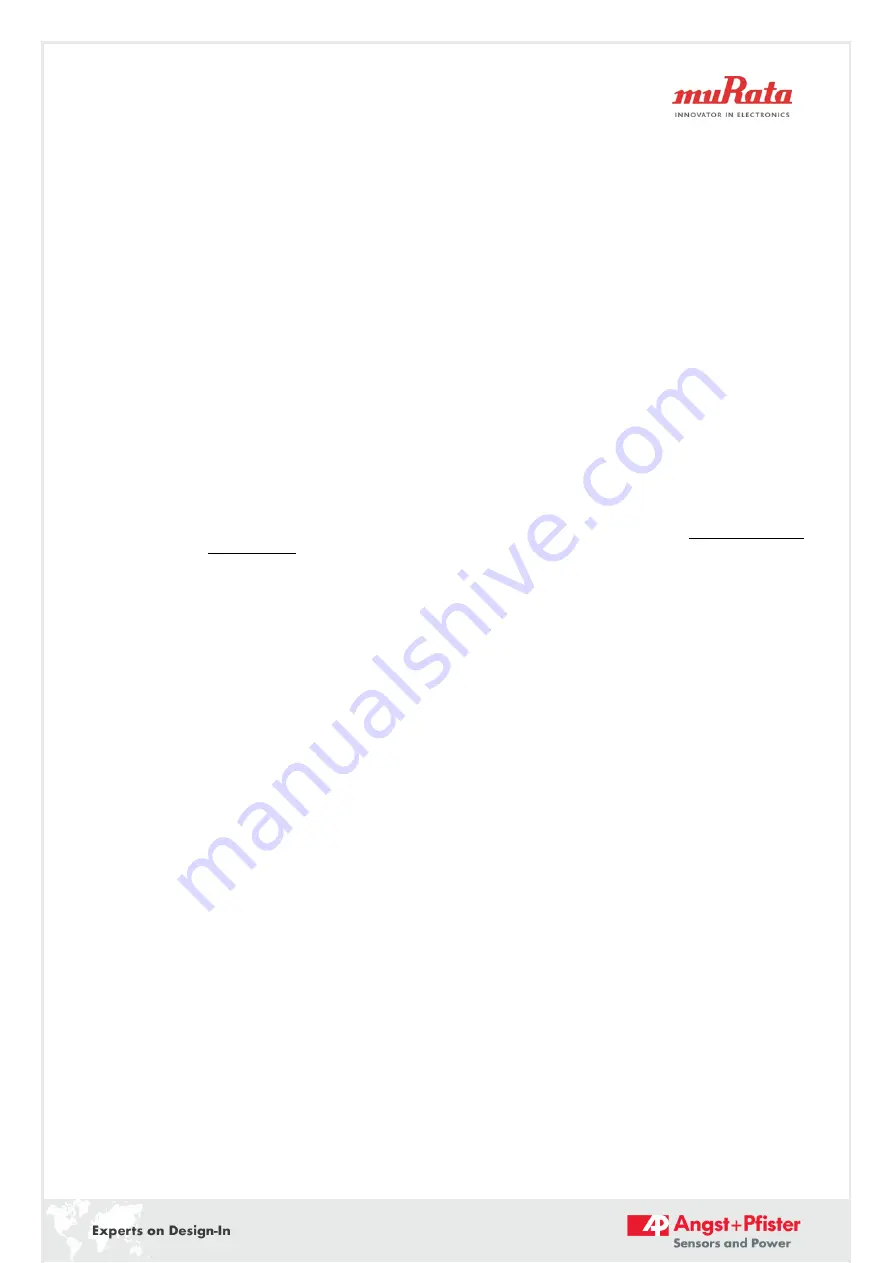
10 (17)
Murata Electronics Oy
Assembly Instructions for Murata's SCC1000 series
TN82
www.murata.com
Rev. 2.0
The process window for lead-free soldering is narrower than for traditional eutectic SnPb solders.
Thus, caution has to be taken care when adjusting the reflow profiles. The reflow profile should be
measured using a thermo-couple measurement system. It is recommended to use at least three
thermo-couples, depending on the application. As a general guide, one thermo-couple should be
placed under a component having the largest thermal mass, one next to the smallest component,
one should be in contact with DIL component's solder joint, and others to the appropriate spots on
a circuit board, e.g. corner, center, bottom of the board etc. The reflow profile should be adjusted
according to the measured data so that each solder joint experiences an optimal reflow profile. The
temperature gradient should be as small as possible across the circuit board. Extreme caution has
to be taken if the circuit board contains components with highly different thermal masses.
5.7 Moisture sensitivity level (MSL) classification
The Moisture Sensitivity Level of the DIL component is Level 3 according to the IPC/JEDEC J-
STD-020D. The part is delivered in a dry pack. The manufacturing floor time (out of bag) at the
customer’s end is 168 hours. Maximum soldering peak temperature for the DIL package is defined
in Table 2.
Following instruction shall be followed:
1. Calculated shelf life in sealed bag: 12 months at < 40 °C and < 90% relative humidity (RH).
2. Maximum soldering peak temperature for the package is defined in Table 2, measured from the
package body.
3. After bag is opened, devices that will be subjected to reflow solder or other high temperature
process must be
a) Stored at <10% RH,
or
b) Mounted within 168 hours of factor conditions ≤30 °C/60%RH.
Note: Do not re-store devices that have exposed >10% RH conditions.
4. Devices require bake, before mounting, if:
a) Humidity Indicator Card is > 10% when read at 23 ± 5 °C
b) 3a or 3b not met.
5. If baking is required, devices may be baked for 24 hours at 85°C.
Note: Also Tape&Reel materials are applicable for baking at 85°C
Note: Packing materials and procedures according to IPC/JEDEC J-STD-033
Note: Level and body temperature defined by IPC/JEDEC J-STD-020D
5.8 Inspection
Optical and visual inspection of solder joints can be done easily, since the solder joints are clearly
seen. A visual inspection of the solder joints with conventional AOI (automatic optical inspection)
system can be used. Also X-ray inspection can be used.
Cross-sectional analysis is also an approved method to inspect how well solder has wetted the
pads of component. Cross-sectional analysis is not used for production inspection, but if required, it
can be used to establish and optimize the component assembly process parameters Cross-
sectioning is a destructive inspection method. An example of a DIL solder joint cross-section is
presented in Figure 8.
10
SCC1xx0_1640-21648-0004-E-0519