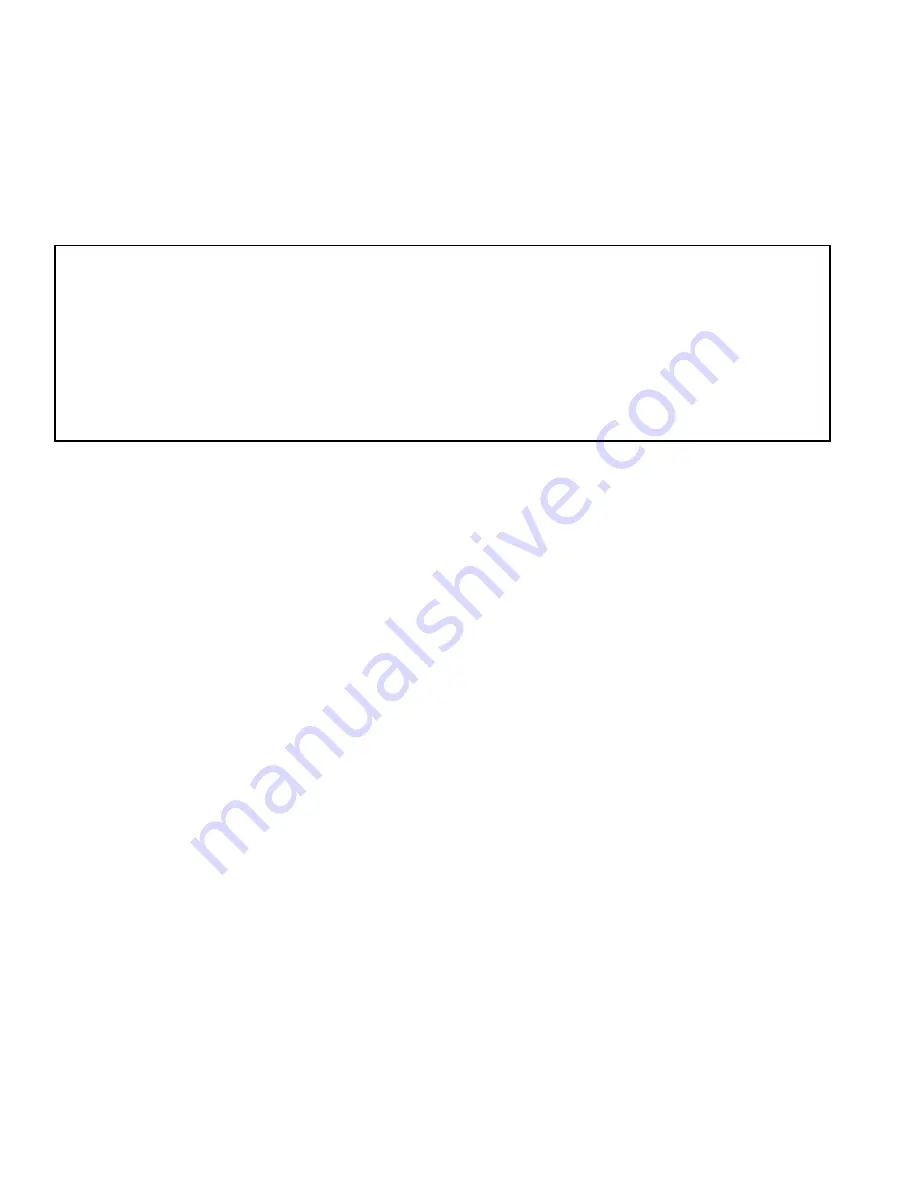
18
Pipe System Flushing Procedure
Before connecting the chiller to the condenser and chilled water loop, the piping loops must be flushed with a detergent and hot water (110-130º F) mix-
ture to remove any dirt and organic residue. After removing residue, continue flushing with a dilute phosphoric acid, sulfamic acid or citric acid and water
mixture to remove inorganic scale in the pipe. Cleaning chemicals such as Nu-Calgon “Imperial Grade” Scale Remover part number 4360-84 or equivalent
suitable for both organic residue and scale removal may be substituted. Otherwise detergents and acids shall not be combined unless approved by the
chemical manufacturers. Only chemicals compatible with 316 stainless steel, copper and carbon steel shall be used. (Any concentrations of hydrochloric or
sulfuric acid or chloride containing chemicals shall not be allowed to come in contact with copper brazed 316 stainless steel heat exchangers).
Caution:
The use of unapproved chemicals in the chilled or condenser water supplies may damage the heat exchangers. These chemicals in-
clude, but are not limited to, hydrochloric acid, sulfuric acid, muriatic acid, and household bleach. Damage caused by the use of these and other
unapproved chemicals is not covered by warranty. The only approved chemicals for heat exchanger cleaning are phosphoric or sulfamic acids in
concentrations of 10 percent or less by volume. For more information contact your Multistack representative.
While flushing, 30-mesh Y-strainers (or equivalent) must be in place in the system piping and examined periodically as needed to remove collected residue.
The flushing process shall take no less than six hours, or until the strainers are clean after flushing. Old pipe systems with heavy encrustation shall be
flushed a minimum of 24 hours and may require as much as 48 hours before the filters run clean. Detergent and acid concentrations shall be used in strict
accordance with the respective chemical manufacturers instructions. After flushing with the detergent and/or dilute acid concentrations, the system loop
shall be purged with clean water for at least an hour to flush out all residual cleaning chemicals.
Pressure Relief Piping and Refrigerant Monitoring
Multistack chiller modules use a small refrigerant charge (typically 0.6 lbs. per ton) and are often exempt from many requirements of ASHRAE 15 Standard.
Pressure relief valves are not standard on water-cooled modules and must be special ordered if required by local codes.
Water Treatment / Specifications
Supply water for both the chilled water and condenser water circuits must be analyzed and treated by a professional water treatment specialist familiar
with the operating conditions and construction materials used in Multistack modular chiller heat exchangers, headers and associated piping. Water quality
for modular chillers using 316 stainless steel brazed plate heat exchangers and carbon steel headers must be maintained within the following parameters:
Water Specifications
Specifications with 25 Percent Glycol
ph >7 and <9
ph >7 and <9
Total Dissolved Solids (TDS) Less than 1000 ppm
Total Dissolved Solids 1,000 - 10,000 ppm
Hardness as CaCO
3
30 to 500 ppm
Conductivity
1,000 - 15,000 ppm
Alkalinity as CaCO
3
30 to 500 ppm
Hardness as CaCO
3
30 - 500 ppm
Chlorides Less than 200 ppm
Alkalinity as CaCO
3
> 500 ppm
Sulfates Less than 200 ppm
Chlorides < 200 ppm
Sulfates < 200 ppm