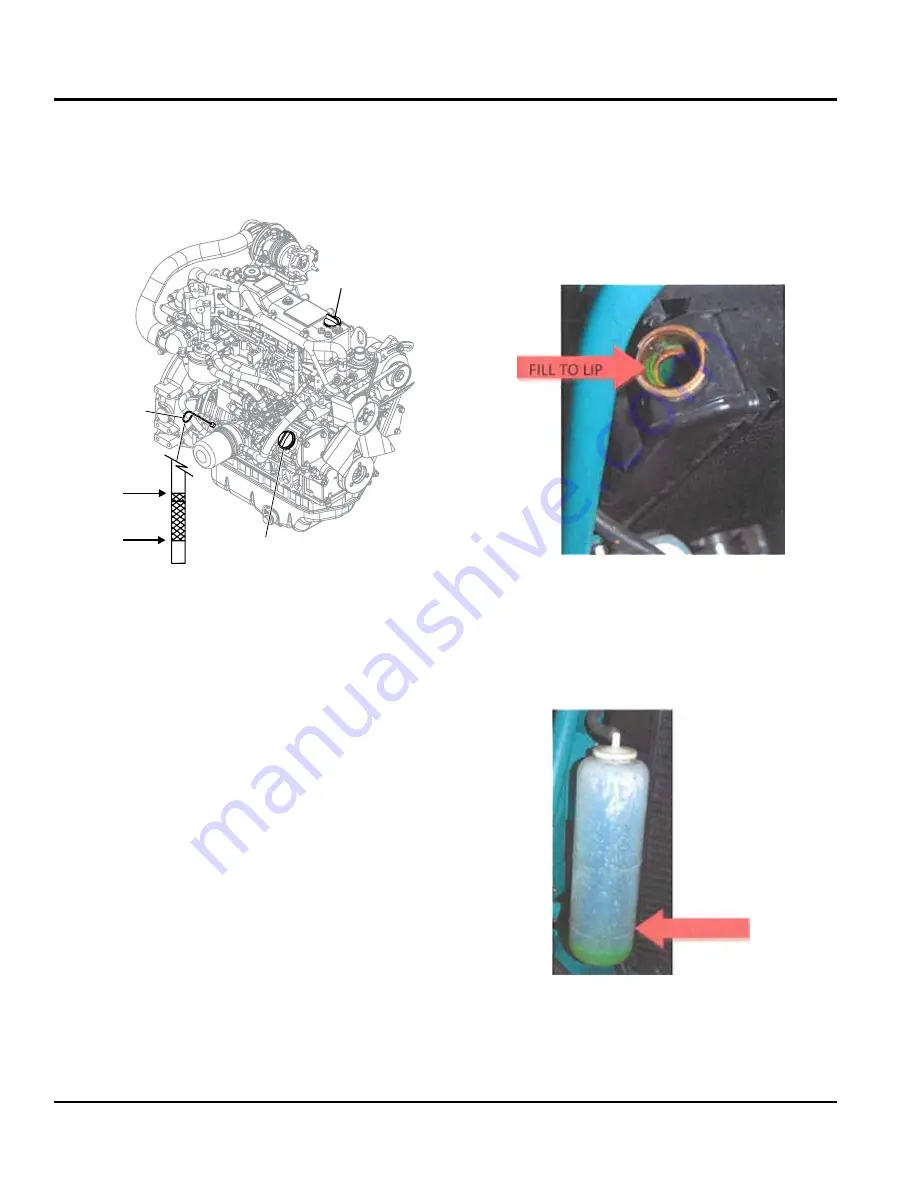
page 14 — HTXD6i/STXD6i Trowel • SeTUp, aDJUSTMeNTS aND CalIBraTIoNS — rev. #0 (03/14/13)
engine oil
1. Ensure engine is level.
2. Remove the oil filler cap (top or side). See Figure 7.
Figure 7. Adding Engine Oil
3. Add the required amount of engine oil at the top or side
engine oil filler port.
4. Wait 3 minutes then proceed with next step.
5. Remove dipstick and wipe clean with cloth.
6. Fully reinsert dipstick.
7. Remove the dipstick. The oil level should be between
the upper and lower) lines on the dipstick.
8. Add more oil if necessary and repeat steps 4 to 7.
9. Reinstall the oil cap and hand tighten. Over-tightening
may damage the cap.
ENGINE OIL
FILLER CAP
ENGINE OIL
FILLER CAP
DIPSTICK
F
L
ADD OIL
FULL
engine Coolant
1. Verify that the radiator drain cock is closed.
2. Remove radiator cap.
3. Pour engine coolant slowly into the radiator until it
is even with the lip of the engine coolant filler port
(Figure 8).
Figure 8. Adding Engine Coolant
4. Reinstall radiator cap.
5. Remove the cap on the reservoir tank.
6. Fill to the low mark (Cold Mark) with engine coolant
(Figure 9).
Figure 9. Reservoir Tank
initial cHeck and adjustments