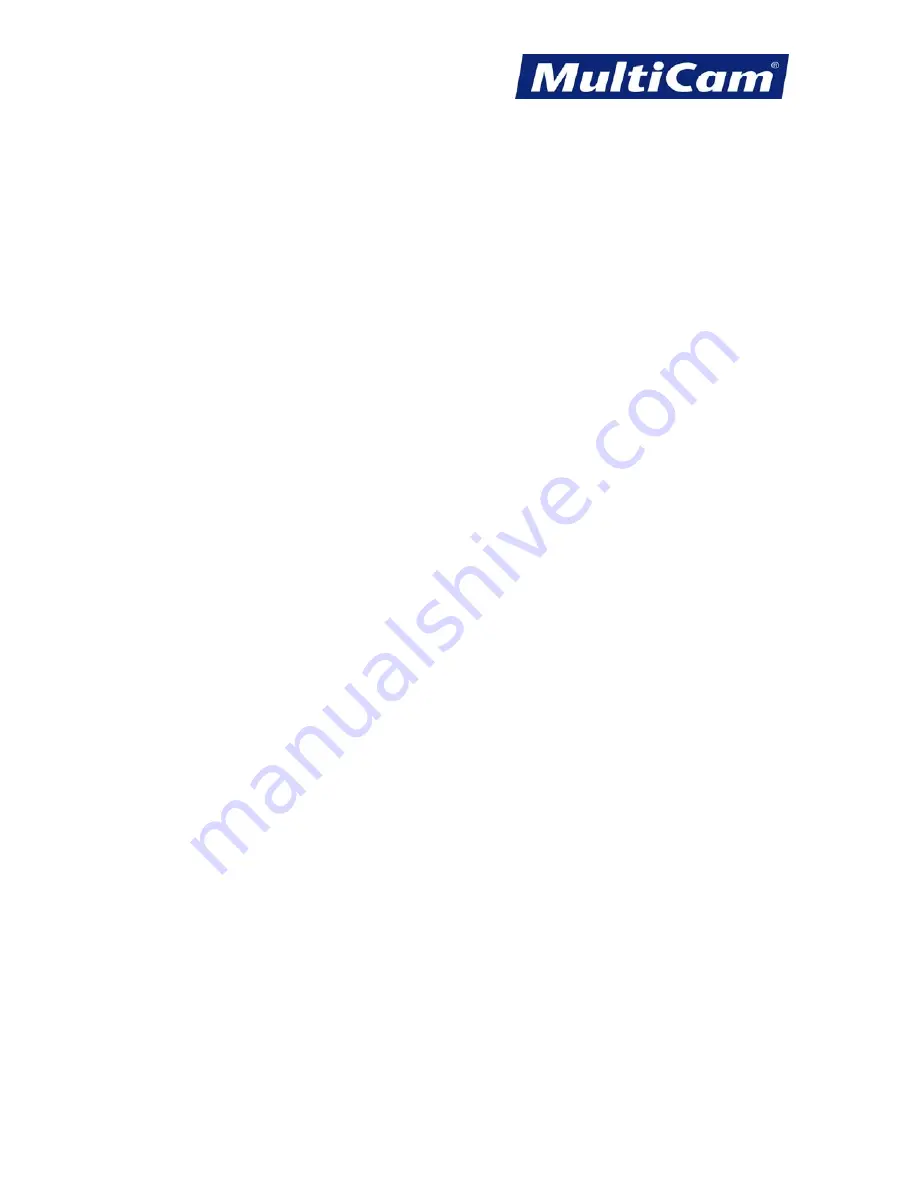
Innovation. Quality. Performance. Best in Industry. Worldwide.
placing hands on the tabletop during the cutting sequence; and observance of proper lock-out procedures when
completing any maintenance or other work on the machine.
(n) The essential characteristics of the tools are sharp points and sides, blunt edges, dense material, and heavy
components.
(o) The conditions that allow the machine to meet the requirement of safety during use, transportation, assembly,
and dismantling when out of service, testing, or foreseeable breakdowns are the solid base on which the machine
is built, the covers over moving parts, the packaging for shipment, the possible requirement of a crane or forklift
to move such pieces as the gantry, the lock-out procedure if followed correctly, optional safety mat and light
curtain devices that will halt the motion of the machine, and the automatic stop of all forward motion in the event
of a fault.
(p) The instructions for ensuring safe transport, handling, and storage operations include the customer hiring a
rigger to facilitate moving the machine; the use of a forklift or crane to move the machine from the delivery van
or truck to the final location; a complete inspection of packaged parts to be completed by the installation
technician and the customer; information regarding any shipping damages reported immediately to the carrier;
insertion of leveling feet so that the machine is at the lowest level possible; and secure anchoring of the machine
components to the floor with adequate space for ventilation.
(q) The operating method to be followed if the machine is involved in an accident or breakdown includes the
operator or installation technician securing the work area so that the installation technician may determine the
cause of the malfunction and troubleshoot a possible workable solution. If a blockage is likely to occur, then the
operator or installation technician will halt any forward motion until it is determined that the blockage can be
prevented.
(r) The adjustment and maintenance information, as well as the preventive maintenance measures to be observed
are as follows:
Safety glasses and hearing protection
should be worn at all times
while operating the machine, and long hair
should be
restrained with a cap or net
when near the machines. Operators should never leave the machine
unattended during the cutting sequence, and labels should be observed at all times.
All machines should be kept clean when not in use. The build-up of chips and dust on the system should be
cleared daily with special attention focused on the gear rack and bearing rails.
All of the bearings should be greased at least twice a month based on an 8-hour work day. The bearings
should be greased more often if the machine is in use more than 8 hours a day.
The Lead Screw Z-axis should be lubricated with a non-aerosol, silicon-based lubricant. Operators are
cautioned
against
using the lithium grease provided by
MultiCam
when lubricating Lead Screws as this
may lead to premature wear of the Lead Screw. Ball Screws, however, can be lubricated with lithium grease.
The filters on the electronics enclosure and vacuum pump should also be cleaned.
Routers * Lasers * Plasma * WaterJets * Knife Cutters
www.MultiCam.com