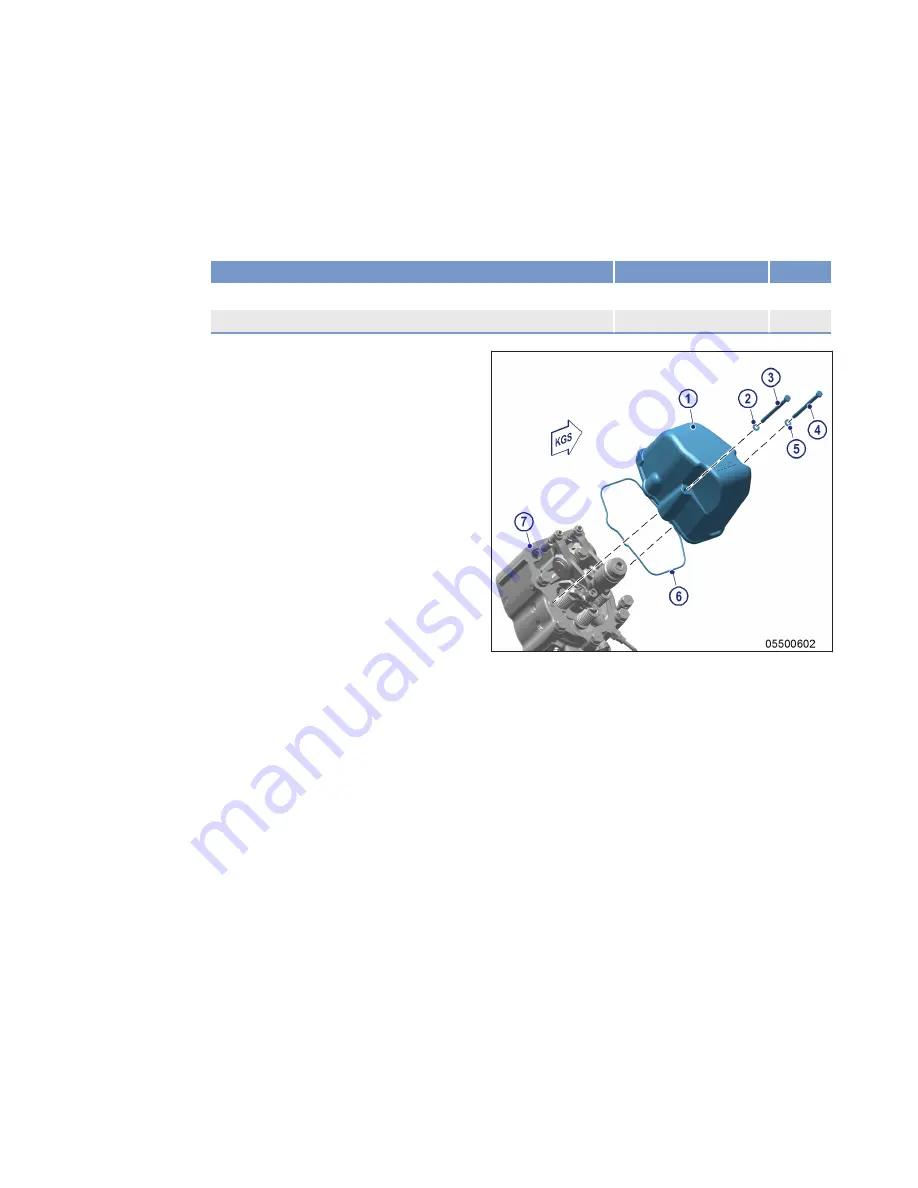
7.5.4 Cylinder head cover ‒ Removal and installation
Preconditions
☑
Engine is stopped and starting disabled.
Special tools, Material, Spare parts
Designation / Use
Part No.
Qty.
Assembly compound (Kluthe Hakuform 30-15)
X00067260
1
O-ring
(→ Spare Parts Catalog)
Removing cylinder head cover
1.
Clean cylinder head covers (1) if severely
soiled prior to removal.
2.
Remove screws (3, 4) with washers (2, 5).
3.
Take cylinder head cover (1) with O-ring (6)
off cylinder head (7).
Installing cylinder head cover
1.
Clean mounting surface.
2.
Check O-ring (6) for damage, replace if necessary.
3.
Coat O-ring (6) with assembly compound.
4.
Place cylinder head cover (1) with O-ring (6) on cylinder head (7).
5.
Install cylinder head cover (1) with screws (3, 4) and washers (2, 5).
MS150112/01E 2014-10
| Task Description | 115
TIM-ID: 0000026826 - 005