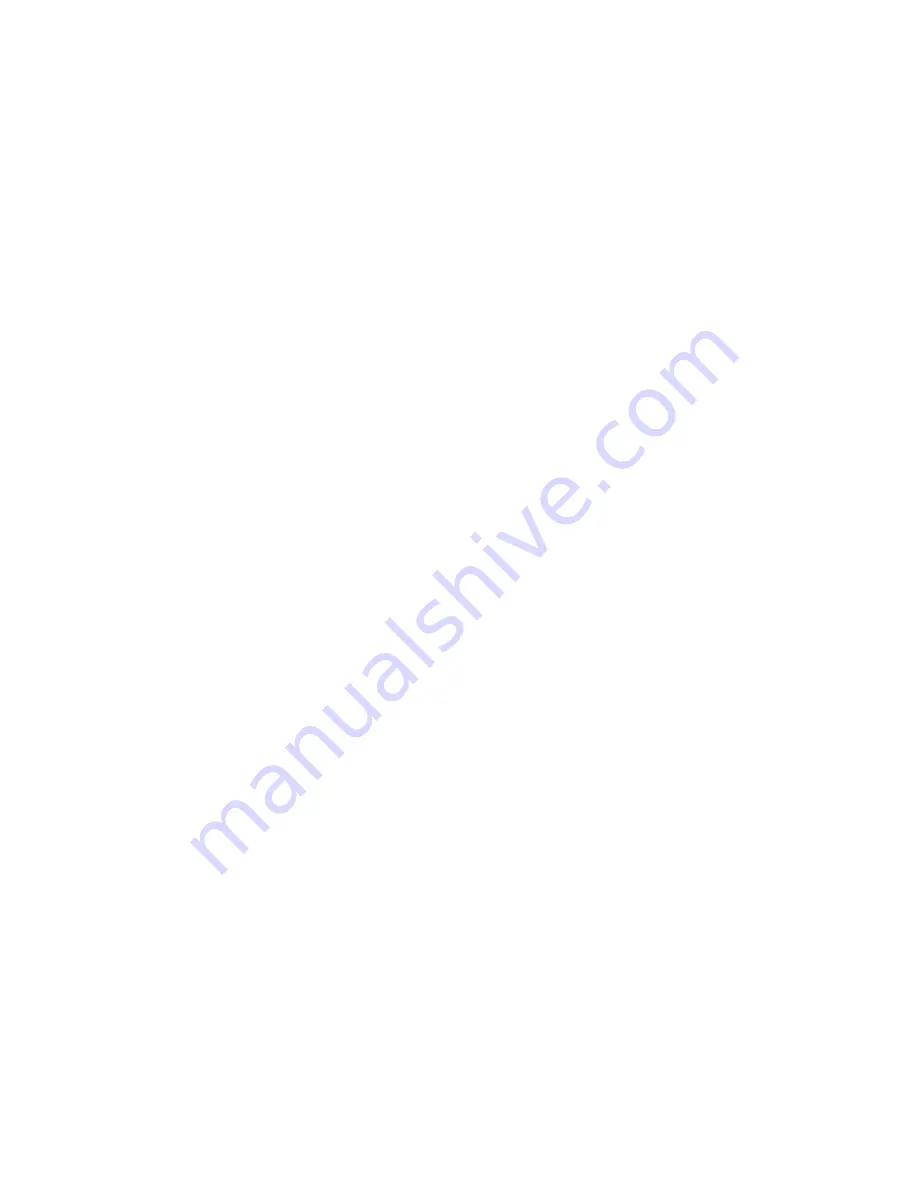
Introduction
MTS Landmark™ Tabletop Load Units - Product Information
41
a pressure-line accumulator to provide fluid storage so that a constant line pressure can be
maintained at the servovalves for maximum performance. The return-line accumulator
minimizes return-line pressure fluctuations.
Pressure control
The load unit can be configured for several pressure configurations:
l
The free flow configuration passes the hydraulic pressure from the HPU (or hydraulic service
manifold) through the manifold to the hydraulic components. This configuration has no
pressure controls; the hydraulic pressure is controlled by the HPU.
l
The on/off configuration applies or removes high-hydraulic pressure to the load unit.
l
The high/low/off configuration applies high or low hydraulic pressure to the load unit.
l
The proportional valve configuration applies high or low hydraulic pressure to the load unit
using a proportional valve to ramp the pressure transitions.
Transducers
The axial load unit includes a force transducer and an LVDT to measure linear forces and
displacements. The axial-torsional load unit includes an axial-torsional force transducer, an LVDT, and
an encoder.
l
Force:
The force transducer (also called load cell or force sensor) measures the amount of
tension or compression applied to it. It has four strain gages that form a balanced Wheatstone
bridge. When forces are applied to the bridge, it becomes unbalanced and produces an
electrical signal that is proportional to the force applied to it. The axial-torsional transducer
includes two Wheatstone bridges; one to measure linear forces and the other to measure
rotational forces. Force transducers are resistive devices and require a DC conditioner to
process the signals from each Wheatstone bridge.
l
LVDT:
The LVDT measures the linear actuator’s travel. The LVDT consists of a transformer
with one primary and two secondary coils wound on a common cylinder. The coil is stationary
inside the actuator. A core is attached to the piston rod of the actuator. As it moves inside the
coil, it produces an electrical signal that represents the position of the piston rod. The phase of
the signal indicates the direction the actuator rod is moving. An LVDT requires an AC
conditioner to process the signal.
l
Encoder:
The encoder measures the amount of rotation produced by the rotary actuator. It is
coupled to the rotary actuator. The absolute encoder produces a unique digital code for each
distinct angle of the shaft.