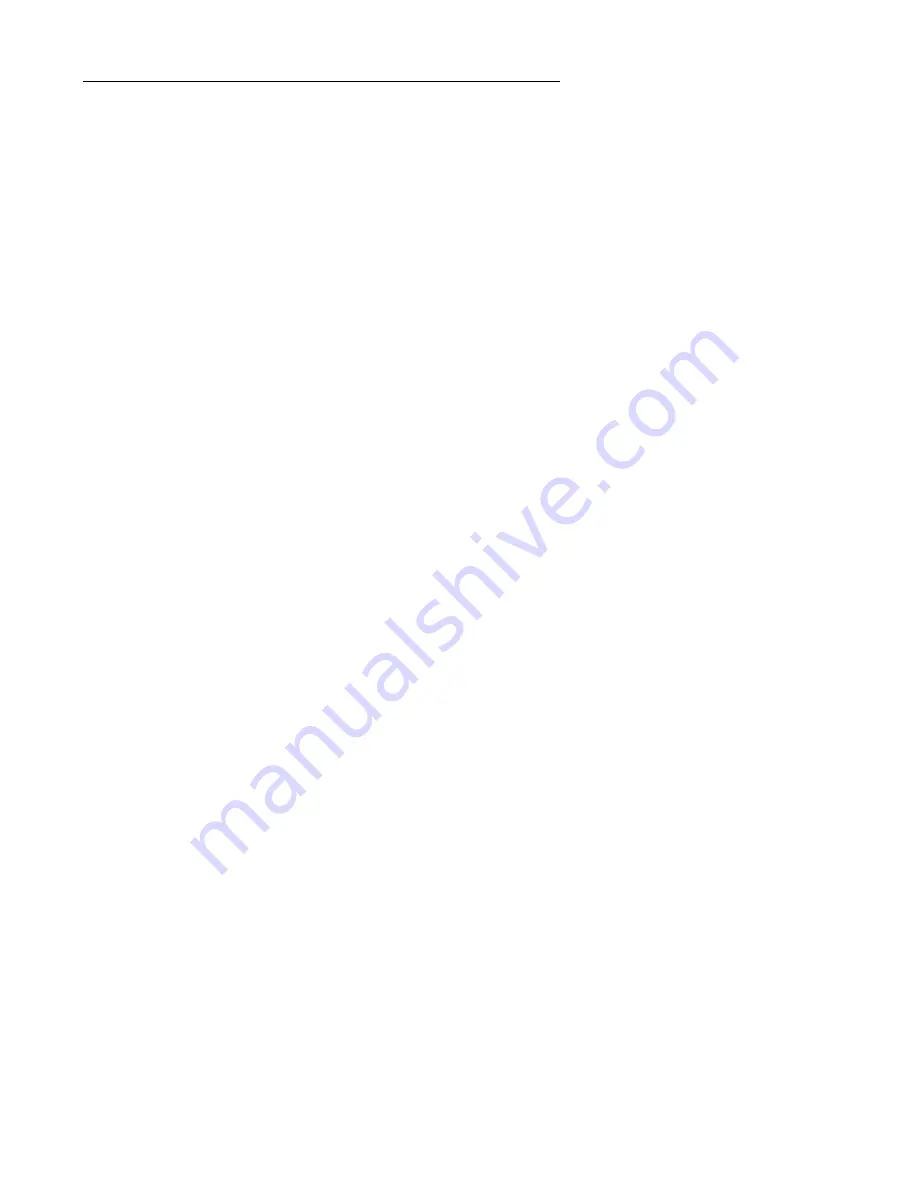
General Instructions
HORIZONTAL CLOSE COUPLED
PUMPS
VERTICAL FLANGE MOUNTED
CLOSE COUPLED PUMPS
FLEXIBLE COUPLED PUMPS
A. Inspection of Equipment
B. Storage
C. Placing Stored Pumps Into
Service
D. Application Considerations
E. Recommended Spare Parts
When properly installed and given
reasonable care and maintenance,
regenerative turbine pumps should
operate satisfactorily for many
years. They do not, however, have
a service life equal to that of low
head centrifugal pumps, which are
not subjected to the typical
differential pressures produced by
the regenerative turbine pump.
Because of the high differential
pressures expected in a regenera-
tive turbine pump, close running
clearances are used to reduce
internal losses. Abrasive particles,
even microscopic ones, in high
enough concentrations, can open
up the close clearances between
internal components. For critical
services it is recommended that
you keep an identical pump for
stand-by use.
1A Inspection of Equipment
Immediately upon receipt of the
shipment, inspect the equipment
for damage or missing compo-
nents. Check the shipping
manifest and report any damage or
shortage to the Transportation
Company’s local agent. Inspect
the crate and any wrapping
material before discarding. Parts
or accessories are sometimes
wrapped individually or fastened to
the skid. Put the instructions that
came with the shipment in a safe
place where they will be available
to those who will be using them for
installation and service.
1B Storage
If the pump is to be stored before
use, it should be inspected as
described in 1A, recrated and
stored in a dry location. Standard
shipping containers are not
suitable for outdoor storage. In
some areas, it may be necessary
to cover the pump's exterior
surface with oil or other rust
inhibiting coating. For storage
beyond 30 days, Ethylene Glycol
or another protective fluid must be
used inside the pump. Fluids used
in the pump should be selected for
compatibility with the pump's
materials. This is very important
when optional seal and gasket
materials have been used.
Protective caps on the inlet and
outlet must also be used. Caps
alone are not sufficient protection.
1C Placing Stored Pumps Into
Service
Special care must be taken when
placing stored pumps into service.
First clean the outside and flush
out the inside. Try to turn the
pump using the coupling. If the
impellers do not break loose
immediately, fill the pump with
water and try again in a few hours.
If this doesn’t work, refer to the
disassembly/reassembly instruc-
tions in Section 4. Loosen the
thrubolts clamping the assembly
together, three full turns, no more.
Fill the pump with water. Apply
torque, 50 foot pounds maximum,
to the coupling.
On close coupled units, access to
the shaft is between the pump and
motor. A vise grip or other plier
type gripping device may be used
directly on the shaft or lock collar,
depending on the motor model
used. Applying torque to the motor
fan blades is not recommended.
The pump should turn before the
50 foot pounds is reached.
Continue turning the pump while
tightening the thrubolts to their
original positions.
1D Application Considerations
1D1 Electrical Wiring
All electrical equipment and wiring
should conform to local and
National Electrical Codes. Use the
motor manufacturer’s instructions
for connecting the motor. Note the
correct rotation and wiring dia-
grams on the assembly. Make
sure the motor rotation and speed
matches that required for the
pump.
1D2 Construction Materials
While it is reasonable to assume
that good judgement has been
used in selecting all the materials
in the pump for compatibility with
process fluids, actual conditions
sometimes vary from original
specifications. Also, typical
material selection charts do not
consider all the temperature,
pressure, and fluid variables. The
customer’s engineer should be
consulted for final judgement on
the best materials for critical
process applications.
1D3 Valves
The first valve to be considered for
a regenerative turbine pumping
system might be a pressure relief
valve. Because this type of pump
has a horsepower requirement
similar to that of a positive dis-
placement pump (constantly rising
hp along with pressure increases)
a relief valve can be effectively
used to limit horsepower. This is
helpful when a non-overloading
motor is specified. It can be of
critical importance if the system
flow rate can vary widely.
There are almost no circumstances
where a flow modulating valve will
work successfully in a regenerative
turbine pumping system. The
steep pumping characteristic
produces very large pressure
changes with small variations in
flow rate. As a result, the modulat-
ing flow from the valve introduces
sharp pressure shock waves that
shorten pump life and may cause
damage in other pieces of equip-
ment in the system.
If a shutoff valve is necessary in
the suction line, use a gate, ball,
butterfly, or other full port valve.
Globe or other flow restricting
valves can in some cases reduce
pump flow or increase chances of
cavitation. A swing check valve is
recommended in the suction line
even when the pump inlet is even
slightly higher than the fluid
1.
Page 502
T51 SERIES