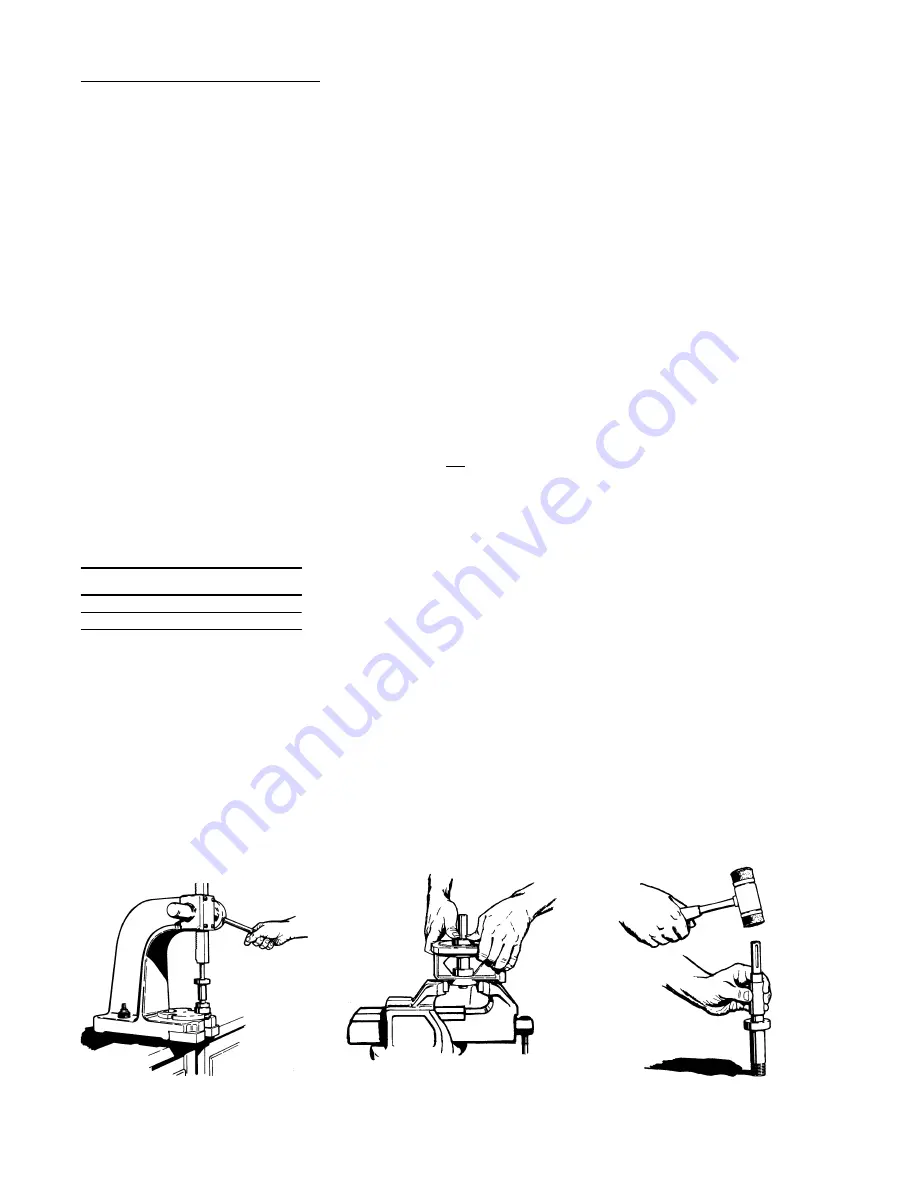
Figure 4-23
Figure 4-24
Figure 4-25
4. Repeat step 3 for the other
bearing.
4E Testing and Final Adjust-
ments
1. Check to be sure that the
rotating assembly turns freely.
Turn the shaft by hand. If it is
tight or rough spots are encoun-
tered, it is likely that at least one
of the bearings was damaged
during disassembly/assembly
operations and will have to be
replaced.
2. Look to make sure that the lip
seals on the bearings are
positioned properly in their
grooves. Correct if necessary.
As the bearings are turned, the
grooves should appear wet with
oil but have no visible grease
present.
3. Recheck the snap ring on the
large bearing end. It should be
firmly in place, and no axial
motion should result from gentle
tapping on either end of the
shaft. (Use a soft mallet so shaft
surfaces are not damaged.)
4. No adjustments are possible or
required. Proceed with the
appropriate pump end assembly
operations. Refer to Section 4
SERVICE - PUMP ENDS (Final
testing is done after the pump
end is in place.)
4D Reassembly
All parts should be visually inspect-
ed and cleaned or replaced as
outlined in 4C above. It is recom-
mended that the bearings be
replaced any time the bearing
pedestal is disassembled for
service.
1. Using an arbor press, install the
bearings on the shaft prior to
installing the shaft into the
pedestal. A steel “donut” with
the proper inside diameter and
outside diameter, refer to Chart
1, should be used between the
arbor face plate and the lower
bearing to insure proper installa-
tion and to prevent bearing
damage. The bearings must
seat against the shoulder for
proper alignment. Refer to Figure
4-23. *Also refer to Alternate
bearing installation procedures.
CHART 1
2. Place the pedestal, pump
mounting surface up, in a vise or
suitable fixture and insert the
bearing assembly. It should be
possible to install the shaft
assembly with firm thumb
pressure. Refer to Figure 4-24.
If more force is required, the butt
end of a hammer handle or
plastic mallet may be helpful.
The shaft assembly should never
be forced or driven in.
3. Install the snap ring (#4) in the
pump end of the pedestal. Be
sure the snap ring is seated
properly in the groove. The
beveled edge of the ring should
face away from the bearing.
4. Install the flinger over the snap
ring. The bearing pedestal is
now ready for pump and motor
installation.
*Alternate bearing installation
procedures.
If an arbor press is not available,
the bearings may be installed on
the shaft using the following
procedure:
This procedure is not recommended
and should only be used in an
emergency situation.
1. Stand a piece of 3/4" pipe for P3
or a 1-1/4" piece of pipe for P15,
with the threads cut off, on a
workbench or similar flat surface,
with the bearing placed on the
correct shaft end.
2. Insert the shaft into the pipe so
the bearing is between the pipe
and the shoulder of the shaft.
Refer to Figure 4-25.
3. Using extreme caution, gently
tap on the end of the shaft until
the bearing rests against the
shoulder. Never attempt to install
the bearings by striking the outer
race.
Page 516
T51 SERIES
Service
4.
P3
P15
Inside Diameter
1"
1 1/4"
Outside Diameter
2"
2 3/4"